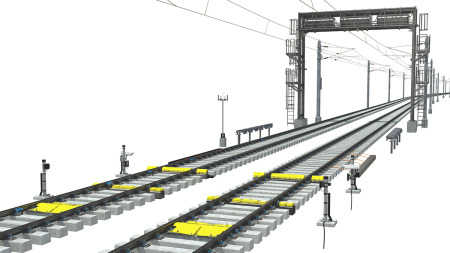
Almost 3,000 installed sensors of our wide product portfolio ensure safety and performance on track – worldwide.
-
1997: Formation of "SST Signal & System Technik GmbH" and start of the development of the hot box detection system PHOENIX MB.
2001: First installation of a PHOENIX MB system in Germany and first supplies to Deutsche Bahn
Installation on the High Speed Line Madrid – Sevilla.2002: Enhancement of the product portfolio with the wheel impact load detection sensor ATLAS.
2003: First installation of a PHOENIX MB system in Australia.
2004: Start of the development of the software CMS (Central Monitoring System).
2005: SST joins the voestalpine Group.
2008: First installation of an ATLAS system in Litauen.
2009 – 2010: Installation of 46 MISTRAL systems for wind and airstream measurement on the High Speed Line Munich - Kassel.
2011: Expansion: A new office in Sydney opens and "Baas R&D" in Waddinxveen is integrated as Dutch branch office.
2014: SST is renamed "voestalpine SIGNALING Siershahn GmbH" and now fully integrated in the voestalpine Group.
2016: Official product launch of the modular Checkpoint solution with interconnected PHOENIX software and hardware at InnoTrans. First installations of the new hot box detection generation PHOENIXMDS HBD.
Since 2016: Update of the central software in the operations control centers of Deutsche Bahn and integration of approx. 3000 devices along the trackside.
2017: Acquisition of DataTraks, USA as wholly-owned subsidiary voestalpine SIGNALING USA – now the competence center for the development of acoustic monitoring. First installation of a PHOENIXMDS Checkpoint with profile validation system, derailment detection, dragging equipment detection and wheel impact load detection in Austria – until 2023 up to 40 locations in Austria will be equipped with modular sensor technologies.
2016 – 2017: Installation of three out of ten acoustic measurement systems on High Speed Lines in Germany to monitor the ICE fleet’s bearings.
2018: First-time use of fiber optic cables for the transfer of the acquired data to cover a larger distance between sensors and cabinet.
2023: Integration of the product portfolio into the zentrak ecosystem
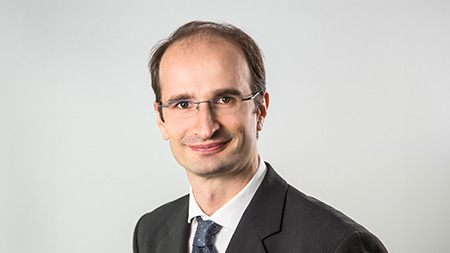
Helmut LIEBMINGER
Member of the Management Board - Chairman
Business Development / Research & Development / Engineering / Human Resources
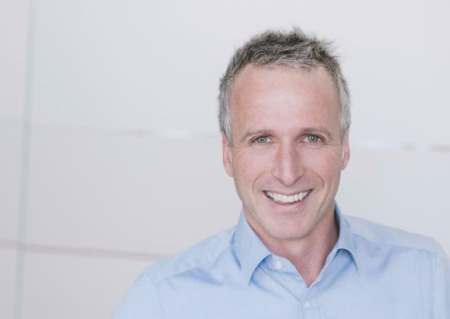
Harald HOPFGARTNER
Member of the Management Board - Sales
Sales & Marketing / Customer Service / Subsidiary Australia
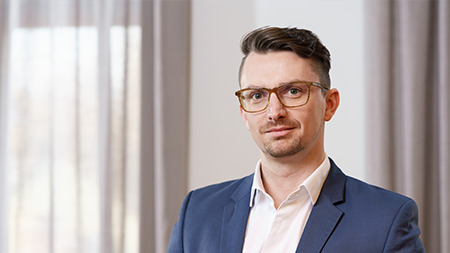
Christian EHMANN
Member of the Management Board - Finance
Finance & Controlling / IT
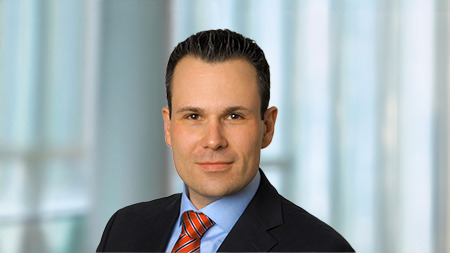
Steve-Patrick STAHL
Member of the Management Board - Operations
Supply Chain Managment / QHSEE / Subsidiary the Netherlands
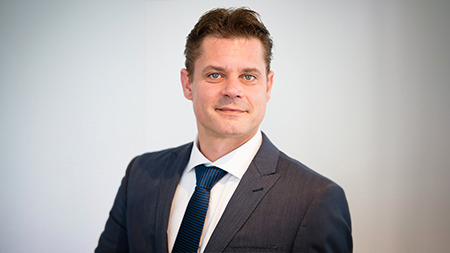
Luuk van de BELD
Senior Vice President - Branch Office Netherlands
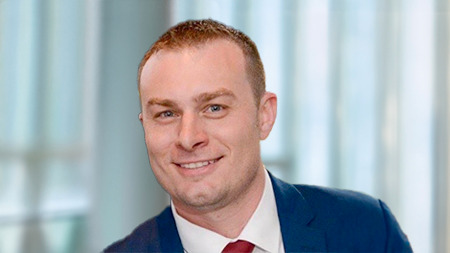
Daniel CRISP
Senior Vice President - Branch Office Australia
Applications
-
Thanks to a wide range of options and variants and compliance to interoperability, zentrak Modular Diagnostic System is suitable for the use in various conditions, including snowy winters and hot and dusty environments like deserts.
Learn more about Mixed Traffic at voestalpine Railway Systems.
-
The modular design perfectly fits the needs of a variety of customer requirements in the metro segment. Especially fast installation, long intervals between maintenance operations and short working time in the track are key features of zentrak Modular Diagnostic System.
Learn more about Urban Traffic for Metros at voestalpine Railway Systems.
-
Flexible sensor arrangements fulfill a wide range of customer requirements. Additionally, less maintenance work thanks to applied condition-based maintenance algorithms reduces the track downtime and increases customer’s value.
Learn more about Urban Traffic for Trams at voestalpine Railway Systems.
-
Heavy haul freight trains demand special requirements to the infrastructure including enhanced resistance to mechanical stress. zentrak Modular Diagnostic Systemproves that every day by measuring various freight trains in North America and Australia.
Learn more about Freight Traffic at voestalpine Railway Systems.
-
zentrak Modular Diagnostic System is equipped with a high speed data acquisition system, enabling reliable measurements even on high-speed tracks and enhancing security of passenger trains traveling at speeds up to 500km/h.
Learn more about High Speed Traffic at voestalpine Railway Systems.
Products & Services
-
See more information about rolling stock monitoring products at voestalpine Railway Systems.
-
myPHOENIX: voestalpine Signaling Siershahn GmbH created through the service portal "myPHOENIX" the possibility for customers to gain secured access to their personalized area including documentation and repair messages.
Academy: The Railway Systems Academy Campus Siershahn is your competent partner for knowledge transfer and extensive professional development.
Life Cycle Management: In order to keep a high quality level and to let innovation grow, it is necessary to replace outdated parts or products by more efficient components. Learn more about Life Cycle Management.
Awards
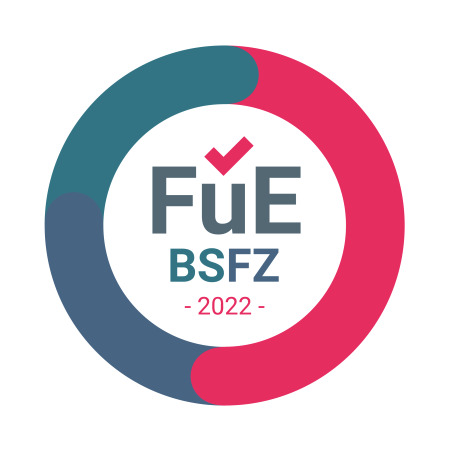
BSFZ Certification Mark
voestalpine Signaling Siershahn has been awarded the seal of quality for research and development by the German Federal Ministry of Education and Research (BSFZ). This BSFZ certification mark certifies the company's innovative competence.
The aim is to develop a diagnostic and monitoring platform for transnational railway systems. For the first time, railway companies, wagon owners and connecting railway operators are to be provided with cross-border information in order to organise integrated operational processes effectively and efficiently. The unique combination of data from existing and new sensor systems will create a database that will enable the identification of critical components and the development of advanced methods for predicting damage and wear behaviour.
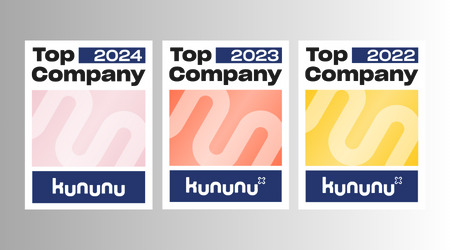
kununu Award
kununu is the leading employer comparison platform in the German-speaking world. To date, employees and job seekers have posted more than 10 million workplace insights in the form of employer reviews, salary information and company culture ratings.
Every year, the platform honours the best employers with the Top Company Award. Approximately 5% of all employer profiles receive this award based solely on kununu ratings. The voestalpine Signaling site in Siershahn, Germany, has received continuous recognition over the last three years since the Top Company Award was introduced.
Current vacancies
Terms & Conditions, Facts
-
voestalpine Signaling Siershahn GmbH
Bahnweg 1
Gewerbegebiet Halsschlag
56427 Siershahn
GermanyLegal Form: Limite Liability Company (GmbH)
Registered Office: Siershahn
Company Registry Number: HRB 5567 at the Regional Court Montabaur
Value Added Tax-Number: DE 185938353 -
Our philosophy places the realization of customer requirements at the core of our business. We utilize our many years of experience, high flexibility as well as motivated employees for the benefit of the customer. We always want to meet the demands and requirements and aim to increase the satisfaction of our customers to keep them as permanent business partners.
Quality is a corporate commitment and therefore an ongoing task for all employees. Everybody should know and be aware of their responsibility as well as the demands.
We commit to the following:
- a continuous improvement in the Quality, Environment, Energy, Health and Safety as well as the Information Security Management Systems,
- fulfilment of the the legal, contractual or other, requirements and commitments,
- providing safe and healthy working conditions to prevent work related injuries and / or illnesses.
For more information, please see our official company policy.
Certificates - Headquarters in Siershahn
- Quality Management: ISO 9001
- Environmental Management: ISO 14001
- Energy Management: ISO 50001
- Health and Safety Management: ISO 45001
- Information Security Management Systems: ISO 27001