Maintenance of rail in tracks and turnouts
The demand for reduced life cycle costs, increased availability and a growing environmental awareness mean that track maintenance is becoming increasingly important. A customized maintenance strategy is a requirement for ensuring the availability and reliability of railway tracks. Regular grinding of rail in tracks and turnouts is an integral part of a holistic maintenance strategy.
With its grinding technology for rail in tracks and turnouts, voestalpine Track Solutions Germany GmbH, a company of voestalpine Railway Systems, offers innovative maintenance that meets the requirements of infrastructure operators in terms of short down times, cost optimization and safety, as well as responsible environmental protection.
voestalpine Track Solutions Germany GmbH operates several RGH 20C on-track grinding machines. Thanks to the flexibility of these machines, they may be used for preventive and corrective maintenance as well as initial grinding on rail in turnouts, connecting tracks, level crossings and other limited areas.
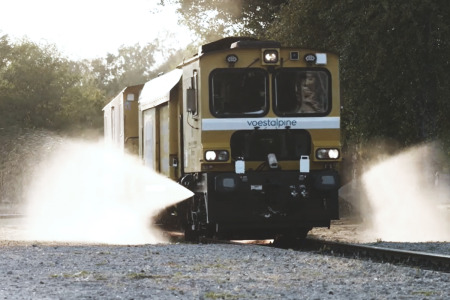
The integrated measurement and testing technology enables continuous logging of the work performed, with no need for manual on-track measurements. This ensures the best possible quality and safety performance. Our goal is to remove only as much material as necessary in order to guarantee customers the maximum possible wear reserve and thus the maximum rail service life. An integrated cleaning system (approved for high-speed lines) completes the machining process.
Fields of application for mobile rail grinding
All European standard gauge lines as well as connecting and industrial railways:
Initial grinding
- Removal of the decarburized layer
- Creation of a homogeneous rail surface
Preventive & corrective maintenance
- RCF damage
- Corrugation
- Re-profiling
Customer benefits:
- Significant extension of rail service life in turnouts and tracks
- Maximum flexibility in the machining of:
- Tongue rails
- Frogs (as far as technically feasible)
- Level crossings
- Minimal residue from rail processing due to the integrated cleaning system
- High cost-effectiveness due to condition-based material removal (“as much as necessary, as little as possible”)
How can we help you?
If you have questions or feedback, please feel free to contact us. We are happy to help!