- Rail Steel Production in the most modern Rail Rolling Mill worldwide
- Rail Technologies which are applied - Heat Treatment Technology, Rolling Technology, Tunnel Track Technology (TTT)
- Rail Finishing
- Rail Quality Control
Rail rolling mill - The most modern worldwide for rails production
To meet the demand of its customers on all 5 continents, we operate the largest and most efficient dedicated rail rolling mill in Europe. If the output of only one single year could be strung together, it would bridge the distance between Northern Europe and Southern Africa.
By deploying our ultra-flexible rolling technology, we manufacture weld-free rails up to 120 meters and in more than 120 different rail profiles, which are also available in many premium and super-premium heat-treated steel grades.
Customer benefit which we reflect by the fact we offer the widest product range of all rail manufacturers worldwide including numerous special rail profiles.
However, our competence is not limited to the production of rails in world-leading quality. By combining advanced technologies, process innovation, system expertise for the entire rail track, logistical expertise and service orientation, we can offer our customers a unique benefit package. Based on this wide spectrum of differentiation as compared with other rail producers, we are set to maintain and expand our leadership in delivering the highest value for our customers.
Rail steel production
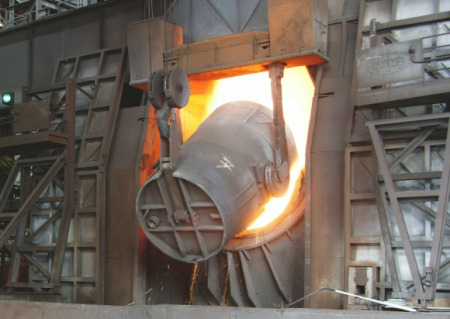
We carry out the production of the railroad track steel at our own steel plant in Donawitz, Austria in process routes that have been optimized for rail manufacture. Our compact LD steel plant is
- one of the most modern in the world and
- focused on the production of ultra-clean special steels for areas of application in the railway, automotive and oil industry.
The intensive cooperation with the steel plant allows the continuous and holistic further development of more innovative rail steels taking the relevant aspects of metallurgy, rolling- and heat-treatment technology into consideration.
Rail technologies
-
High-Performance Heat-Treatment Technology Intelligent cost saving by heat-treated premium grades
Unlike many other manufacturers, we do not use ready-made heat treatment units delivered from plant suppliers. We solely deploy our self-developed technology known and introduced worldwide under its brand name HSH® Technology.
Thus, we are able to heat-treat practically any, even the most complex rail profile, in ultra-long rolling length. We also offer a specific solution for each rail traffic mode.
We rolled out several generations of LCC-optimizing HSH® rail concepts successfully based on metallurgical progress as well as the experience gained from application in hundred thousands of track kilometers. No doubt a unique feature in comparison with other manufacturers.
Today, our updated and patented technology allows us to produce heat-treated rails of consistently topmost quality in sync with the rolling cycle. More than this, our current heat-treatment facility (newly invested in 2009), controlled by more than 100 different parameters, is capable to mass-produce also entirely new rail steels, which are presently in development.
Our worldwide-patented HSH® process is an in-line heat-treatment technology for the manufacture of heat-treated premium and super premium rails. Developed by voestalpine Rail Technology it is directly integrated into the manufacturing process and offers the following benefits for the customer:
- High hardening depth (deep head-hardened)
- Best homogeneity over cross-section and length
- All sections (vignol, grooved and tongue rails) up to 120m in length
- Environmentally-friendly production
The new double heat-treatment plant allows the heat treatment of pearlitic and bainitic rails for diverse areas of application according to the highest quality requirements and without capacity limitations for maximal product availability.
-
The state-of-the-art production of the rails takes place in the rail mill of voestalpine Rail Technology. It combines:
- The most modern production technologies dedicated to the manufacture of rails
- The tightest profile tolerances due to universal rolling technology
- Nearly 100 different rail sections on offer - a globally unique section range that responds to the specific requirements of our customers
- More than 100 years of production experience as a technology leader
All rails are manufactures as required by customers in accordance with EURONORM, AREMA and other international standards (GOST, IR, AS, JIS among many others).
Support and ancillary processes are also carried out in Donawitz with the greatest care and attention: for example the handling of rails is exclusively done by lifting and lowering them with a crane system specially developed to ensure the best possible surface finish.
-
This business area specializes on the development, design and supply of track systems for tunnel construction.
Our references include among others the Gotthard Base Tunnel in Switzerland (all materials were transported on voestalpine’s temporary construction-site rails, including 28 million tons of excavated rock), Crossrail in London (supply of special construction components to reduce noise and vibration), Stuttgart 21 (construction track design) and GKW Inn/Tyrol, one of the largest eco-hydropower plants with a 23km tunnel.
Rail finishing
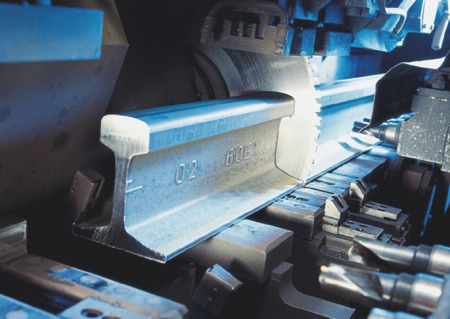
We do rail finishing in accordance with customer wishes, i.e. the rails are drilled, surface treated and bent according to specifications.
Rail quality control
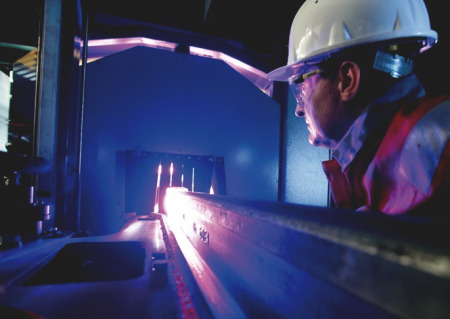
In our testing center, all rails undergo a 100% non-destructive testing in newest facilities. In addition to the mandatory testing procedures defined in international standards, specially developed fully automated processes to measure the cross section as well as to inspect the whole rail surface over the entire rail length are applied.
Proven performance. Besides standard laboratory equipment for rail testing we operate full scale rail wheel test rigs in order to provide laboratory rail testing under real loading and contact conditions.
In addition, an extensive worldwide track test network allows showing the benefits of new and optimized rail grades in different loading scenarios (e.g. light rail, mixed traffic, heavy haul and high speed).
How can we help you?
If you have questions or feedback, please feel free to contact us. We are happy to help!