Sandwichbauweise für Batteriekasten-Unterböden
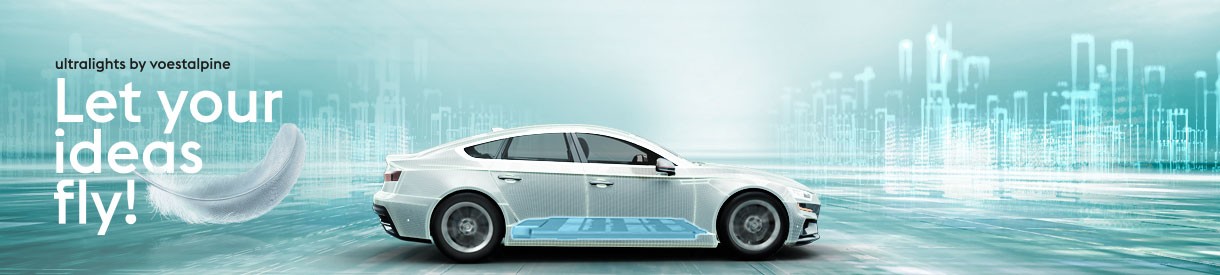
voestalpine serviert Fakten
voestalpine hat im Feld Batteriekasten gezielt Kompetenz aufgebaut und ist für Hersteller ein Partner, der mit Know-how und umfassender Unterstützung mehr als optimale Stähle bietet. Bei Batteriekasten-Unterböden ist die Sandwichbauweise eine interessante Möglichkeit. Die Forscher und Entwickler der voestalpine gingen der Sache auf den Grund.
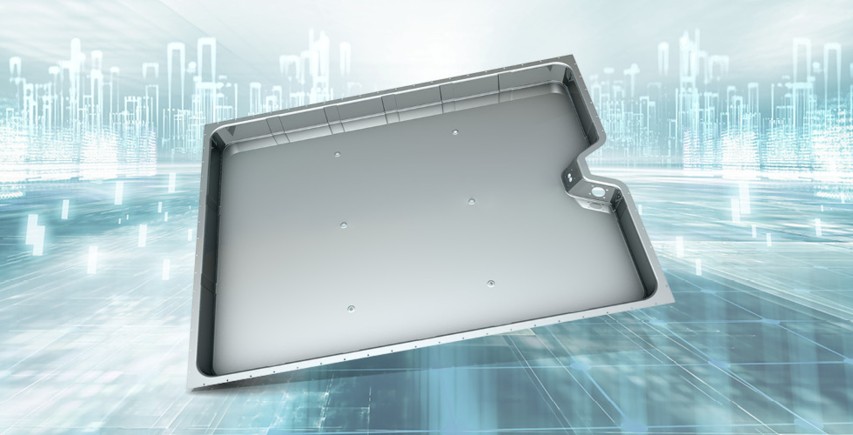
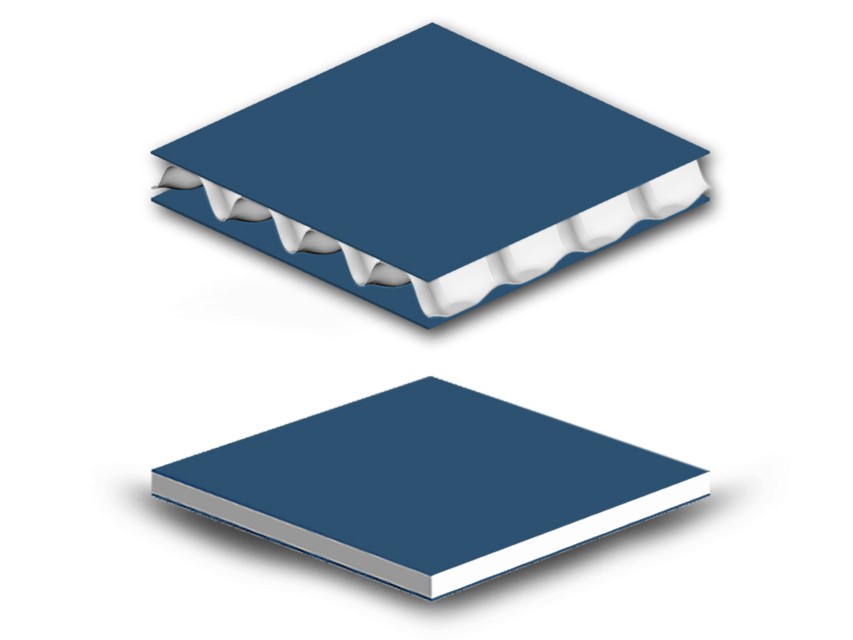
Sicherheit ganz unten steht ganz oben
Als exponierte Bauteile müssen die Batteriekasten-Unterböden in E-Fahrzeugen hohe Anforderungen an Festigkeit und Sicherheit erfüllen. Hindernisse auf den Straßen, Bordsteine, die Kollisionen mit Pollern u.v.m. sind Gefahrenquellen, die hochfeste Strukturen verlangen. Darüber hinaus ist das Gewicht immer ein Thema. Gewichtsersparnis spart Antriebsenergie. Und dass Batteriekästen um die 3 m2 Unterbodenfläche aufweisen, erleichtert die Aufgabe nicht gerade.
Sandwichbauweise ist eine Lösung
Die Kombination aus hochfesten Stählen mit leichten Kernstrukturen ist Stand der Technik. Theoretisch. Aber erst die richtigen Stähle und Materialkombinationen schaffen ideale Lösungen.
Der Testaufbau
Um das Eindringen von Hindernissen in den Batteriekasten abzubilden, wurde ein Pollertest gewählt. Der runde Kopf des Prüfkörpers (Durchmesser 50 mm) dringt hier in die Prüffläche (350 x 350 mm) ein. Gesetztes Ziel war, einer Kraft von 20 kN ohne Verformung standzuhalten. Beim Testaufbau wurden auch verschiedene Lagen des Prüfteils berücksichtigt und ausgeführt: Freiliegend (1 mm Abstand zum Einspannrahmen) bzw. mit Schrauben fixiert.
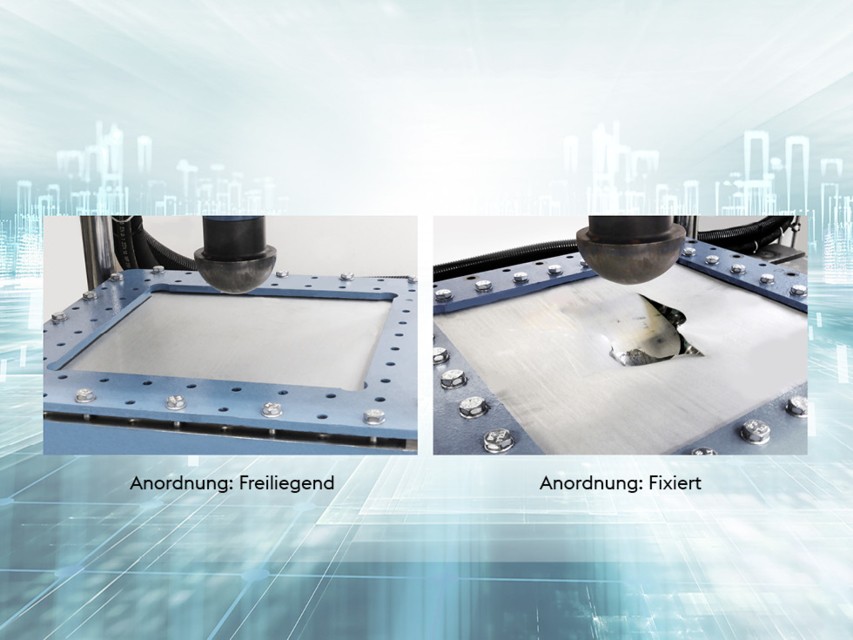
Untersuchte Sandwich-Strukturen
- Für die Außenlagen untersuchten die voestalpine-Experten verschiedene Stahlsorten und Dicken. Das umfasste sowohl Dualphasen-Stähle (z.B. CR260Y450T-DP) sowie hochfeste Complexphasen-Stähle.
- Beim Kernmaterial kamen Stahl-Wellbleche aus hochumformbaren Dualphasen-Stählen (z.B. CR290Y490T-DP) sowie Polymerschaum mit einer Dichte von ca. 0,1 kg/dm3 zum Einsatz.
- In der Fügetechnik wurden gezielte Experimente mit verschiedenen Epoxidharzen und kautschukbasierten Klebstoffen mit unterschiedlichen Applikationsstrategien durchgeführt.
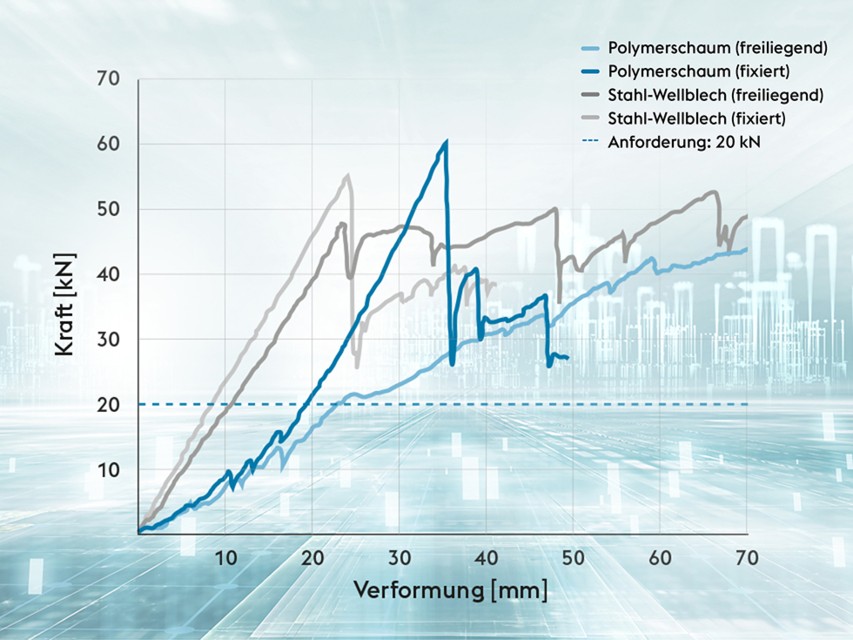
Ergebnisse – nach dem Geschmack der Kunden
Die umfangreichen Versuchsreihen ergaben, dass es durch abgestimmte Variation der Parameter Stahlsorte, Stahlblechdicke und Kernmaterial möglich ist, Kosten und Gewicht nach individuellen Kundenanforderungen zu optimieren. Generell zeigen die Ergebnisse eine hohe Steifigkeit, die im Verhältnis zum spezifischen Gewicht des Sandwich steht, wobei die Bruchkräfte allgemein über 50 kN liegen. Die Sandwichdicke betrug 11,0 mm (Kernmaterial Schaum) bzw. 13,5 mm (Kernmaterial Stahl-Wellblech).
voestalpine steht als Partner für Sie bereit
Alle Ergebnisse und Erkenntnisse stellt voestalpine gern zur Verfügung. Profitieren Sie von:
- Der voestalpine Werkstoffexpertise
- Den Werkstoff- und Simulationsdaten für Ihren Designprozess
- Dem umfangreichen Füge-Know-how