Sandwich design for battery box bottom structures
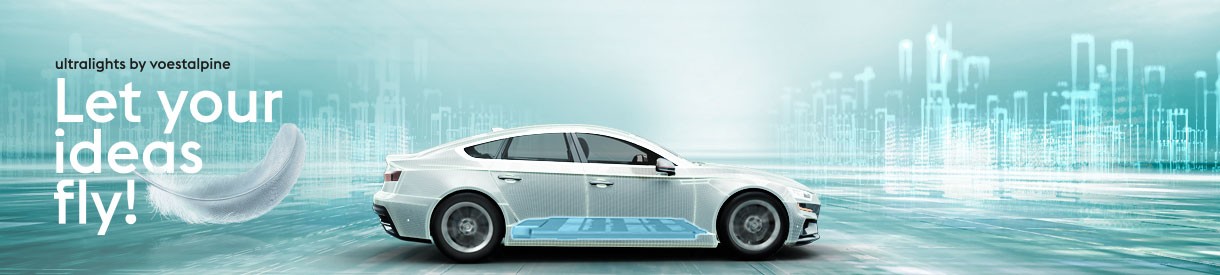
voestalpine serves up the facts
voestalpine has systematically established a great deal of professional expertise in the field of battery boxes and is a manufacturer that offers more than just optimized steels. Sandwich design is a viable option for battery box bottom structures. Researchers and developers at voestalpine get to the bottom of it.
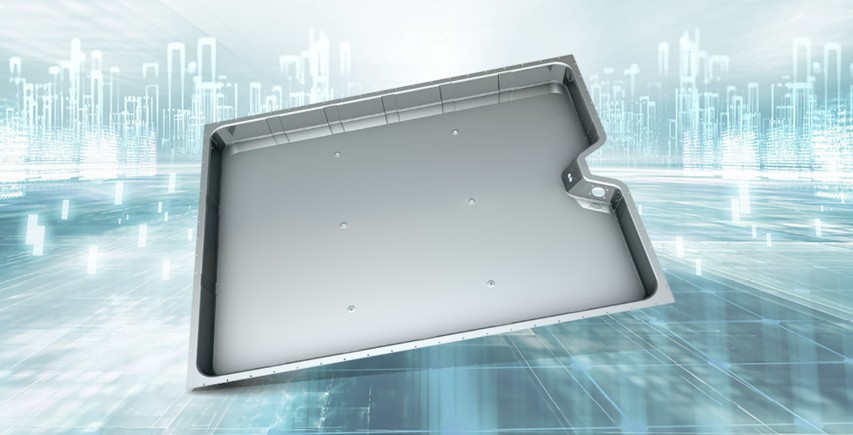
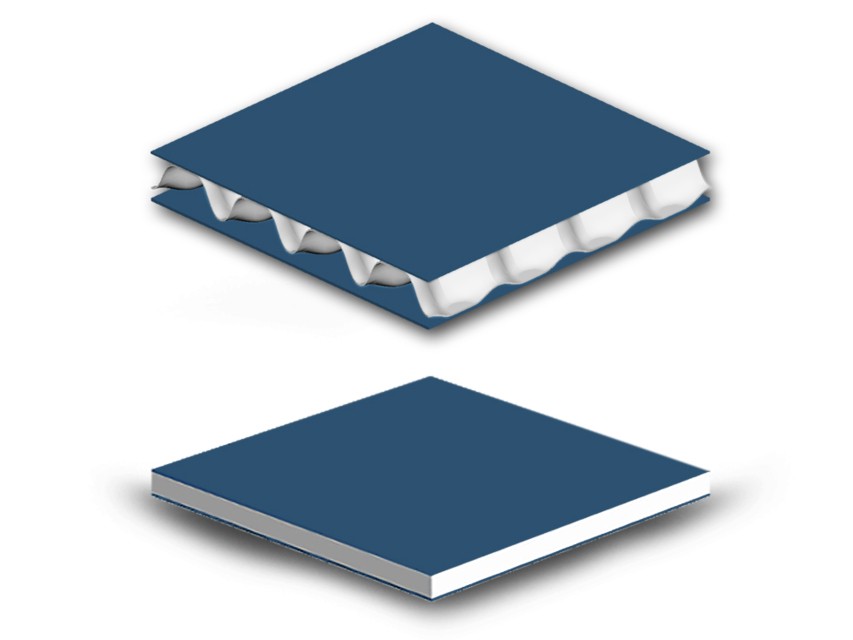
Safety at the bottom on the top of our list
As exposed components, battery box bottom structures must meet the highest requirements with respect to strength and safety in electric vehicles. Obstacles on the road or at the curb, collisions with bollards and other hindrances are sources of danger that call for high-strength structures. Weight is always an issue. Lighter weights lead to energy savings, but the fact that battery boxes feature up to 3 square meters of space in the bottom structure does not make the task any easier.
Sandwich design is one solution
The combination of high-strength steels with lightweight core structures is state of the art. Theoretically. But only the right steels and material combinations can create an ideal solution.
Test setup
A bollard test was chosen to represent the intrusion of obstacles into the battery box. The round head of the test corpus (diameter of 50 mm) penetrates the surface here (350 x 350 mm). The goal was to withstand a force of 20 kN without any deformation. During test setup, different positions of the test components were taken into account: not mounted (1 mm distance to the clamping frame) or mounted with screws.
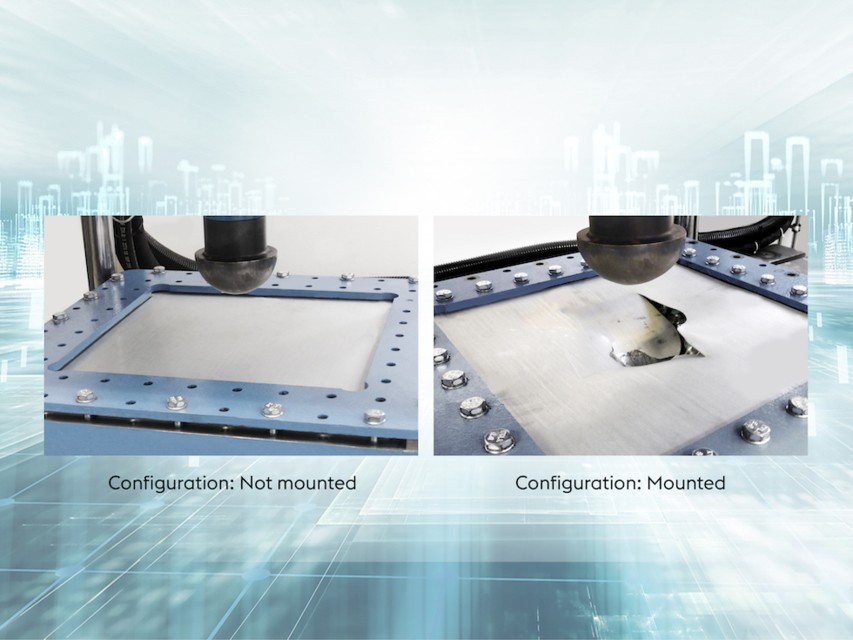
Sandwich structures tested
- The experts at voestalpine assessed a wide variety of steel grades and thicknesses for the outer layers, including dual-phase steels (CR260Y450T-DP) and high-strength complex-phase steels.
- Corrugated steel sheets made of highly formable dual-phase steels (CR290Y490T-DP) and polymer foam with a density of roughly 0.1 kg/dm3 were used in the core material.
- In the field of joining techniques, experiments included various epoxy resins and rubber-based adhesives with different application strategies.
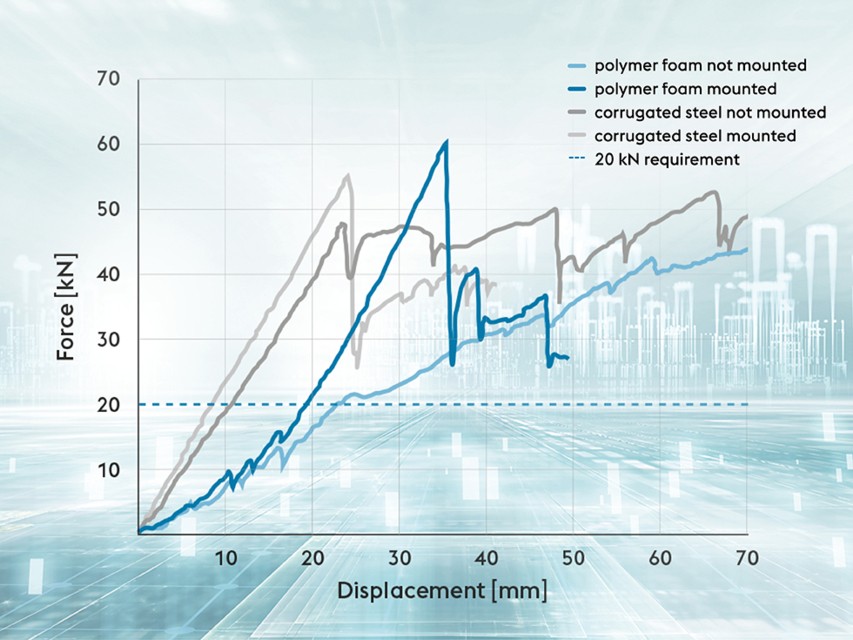
Results tailored to customer demands
Extensive testing showed that it is possible to optimize cost and weight according to individual customer requirements by varying the steel grade, sheet thickness and core material. The results generally indicate high stiffness that is proportional to the specific weight of the sandwich with fracture forces generally exceeding 50 kN. The sandwich thickness was 11.0 mm (foam as the core material) and 13.5 mm (corrugated steel sheet as the core material).
Your reliable partner in the field of battery boxes is voestalpine
The experts at voestalpine are happy to make the results and findings available.
Customer benefits
- Focus on material expertise at voestalpine
- Material and simulation data for every design
- Extensive expertise in the field of joining