What advantages are provided by Backlack bonding?
Legal regulations applicable to industrial motors or the desired extension of the range of electric vehicles with existing battery capacity require increased efficiency in electric machines. A precondition for this is the use of low-loss electrical steels combined with high magnetic permeabilities.
The behavior of the electric motor is additionally influenced by the respective bonding process. Experience has shown that face bonding is the most gentle and versatile bonding method.
Face bonding leads to the best-possible performance and a high degree of motor efficiency for the following reasons:
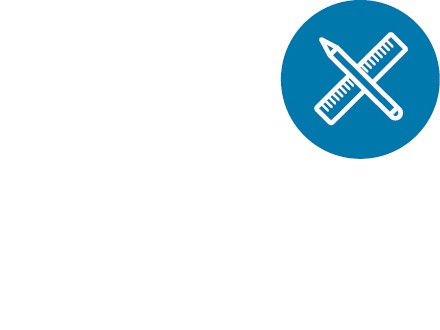
Freedom of design
Backlack allows versatile motor engineering because manufacturing aspects such as the positions for interlocking or weld seams do not have to be considered. This makes it possible to engineer a more efficient electric motor.
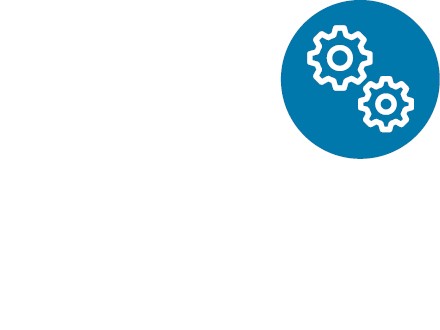
Mechanical stability and dimensional accuracy
Face bonding allows for the maintenance of narrow dimensional tolerances and excellent dimensional stability since the individual laminations are not only connected at discrete points but also utilize the face bonding connection between the laminations.
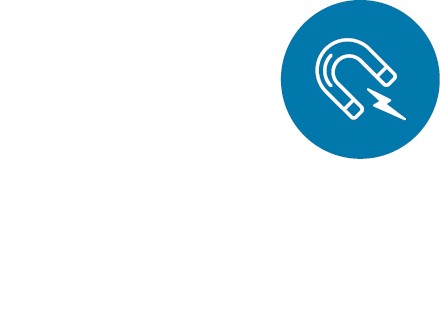
Retention of magnetic properties
In comparison to interlocking and welding, the bonding process is the gentlest bonding method because it does not alter the microstructure either through mechanical deformation (interlocking) or temperature input (welding). This means that magnetic properties are not significantly affected.
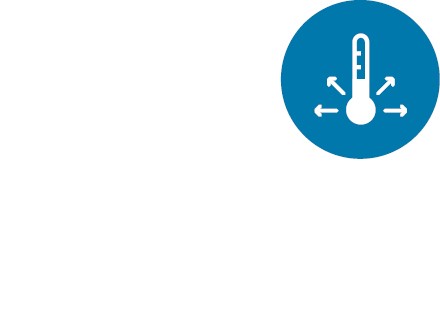
Improved thermal conductivity
There is no air gap between laminations when they are face-bonded. This means that heat conductivity in the axial direction is improved when compared with stacks that feature an air gap (see schematic diagram).
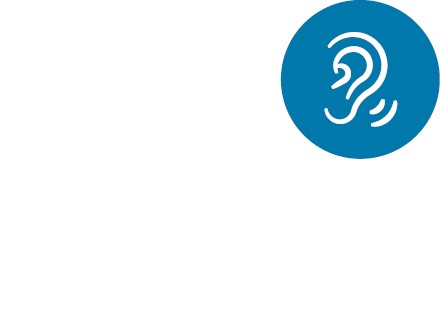
Acoustic advantages
Face bonding minimizes the vibration between individual laminations, and this has a direct effect on the acoustic behavior of the component because noise is reduced in the respective electric machine.
Such an advantage can only be achieved through optimized material coatings. Our long-standing experience in varnish coating provides a foundation for high adhesive strengths and good processability at the customer.
Optimum thermal conductivity in axial package direction
Filling the areas between the lamellae with Backlack not only increases the thermal conductivity of the package. The stacking factor is also reduced to a much lesser extent than would be expected from the higher layer thickness of the bonding varnish.
Schematic diagram of the thermal conductivity:
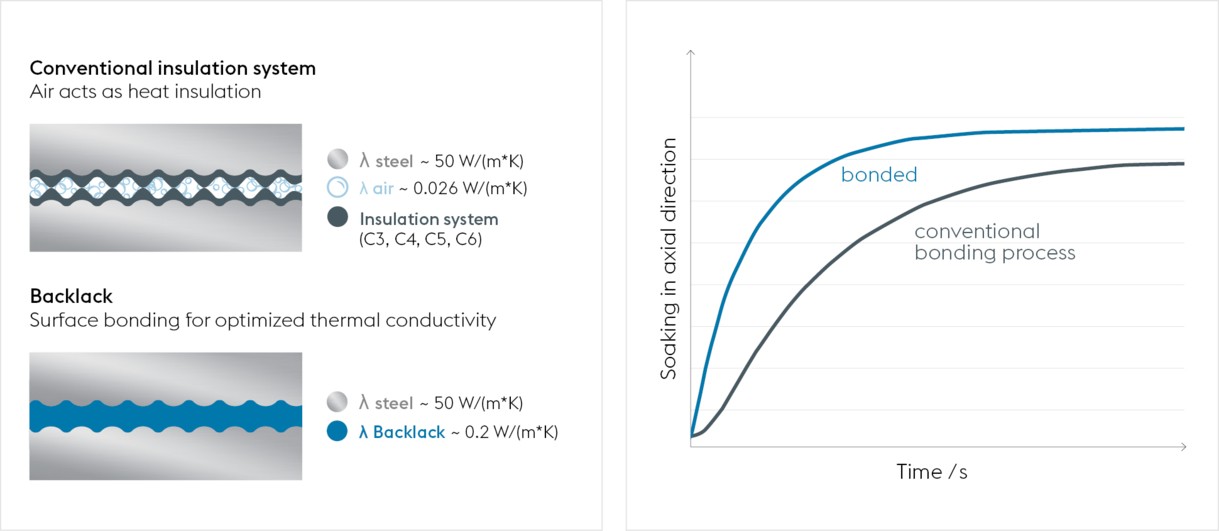