
The world is in the midst of a comprehensive energy transition: electromobility in transport, heat generation in households without fossil fuels or the transformation in industry to achieve carbon neutrality require one thing above everything else: electrical energy.

The technical specialists at voestalpine have succeeded in developing a manufacturing process for 100% media-tight, full-face-bonded stator stacks with integrated cooling. Does it work in the real world?

Successful participation in the exhibition in Berlin with innovative products, sustainable solutions and Austrian hospitality. From 14 to 16 May 2024, voestalpine presented itself at the CWIEME in Berlin and welcomed numerous visitors and business partners at the exhibition stand.
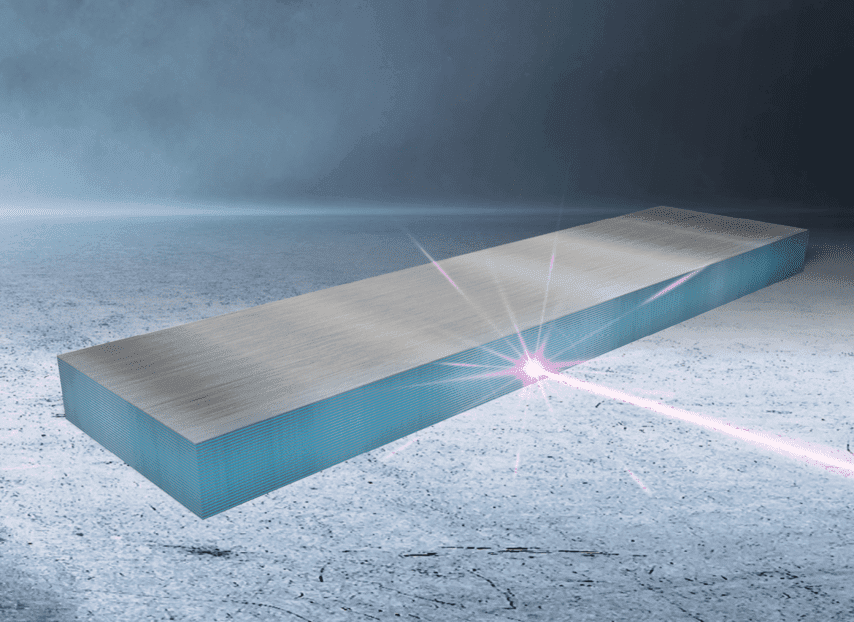
Coiltech Pordenone is the leading trade fair in Italy in the coil winding industry and focuses onmaterials and machines used in the production of electric motors, generators, transformers and coilwindings.
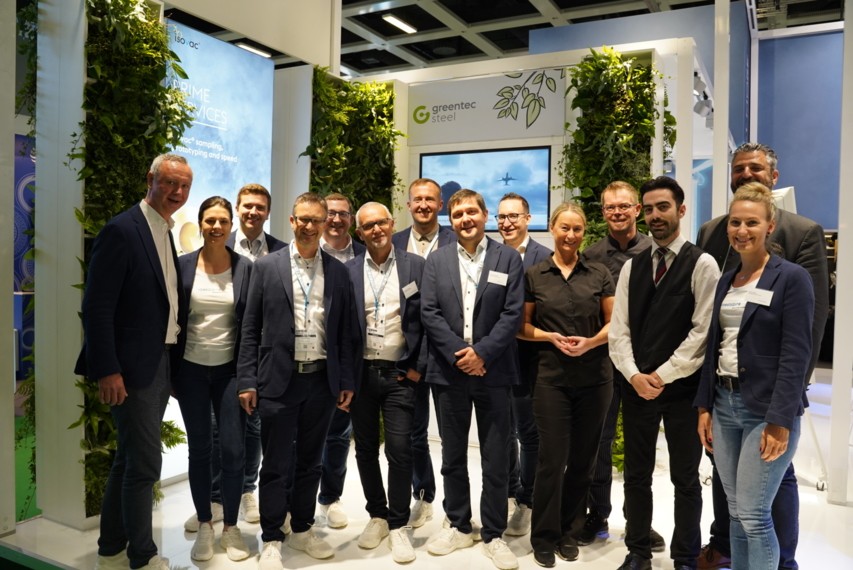
Berlin, May 24, 2023—As a leading manufacturer of electrical steel, we could not afford to miss the CWIEME in Berlin, the world-renowned trade fair for professionals in the electrical industry.
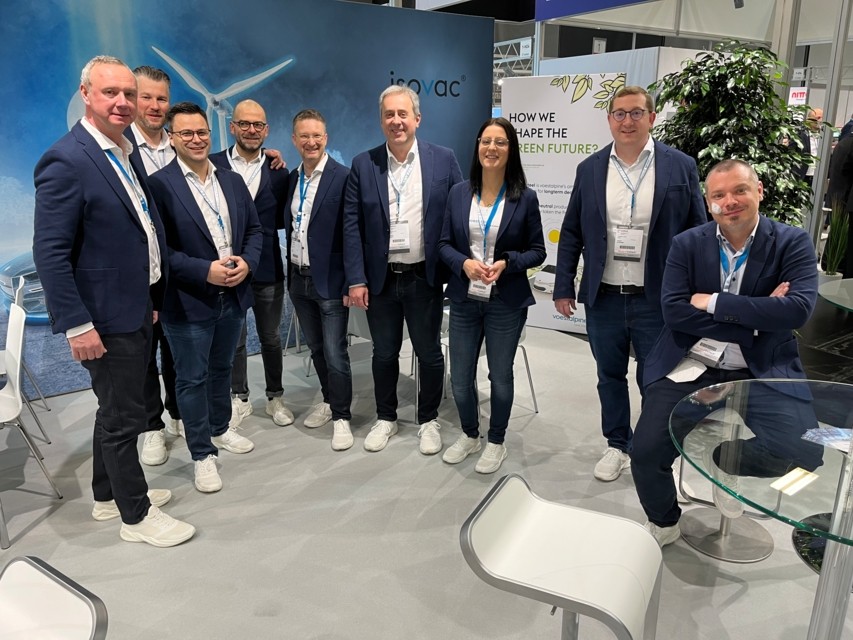
A new location, new topics, many new and familiar faces. The first of the three electrical steel trade fairs took place on 29 and 30 March 2023 in Augsburg. More than 400 exhibitors from 49 nations were there.
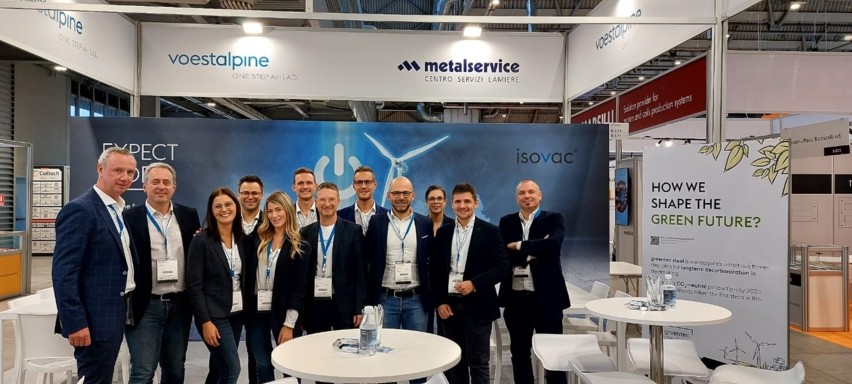
Coiltech in Pordenone was more than worth the trip. Along with our partner Metalservice, we were able to welcome countless customers and interested parties at the joint trade fair stand and to pamper them all with typical Austrian hospitality.
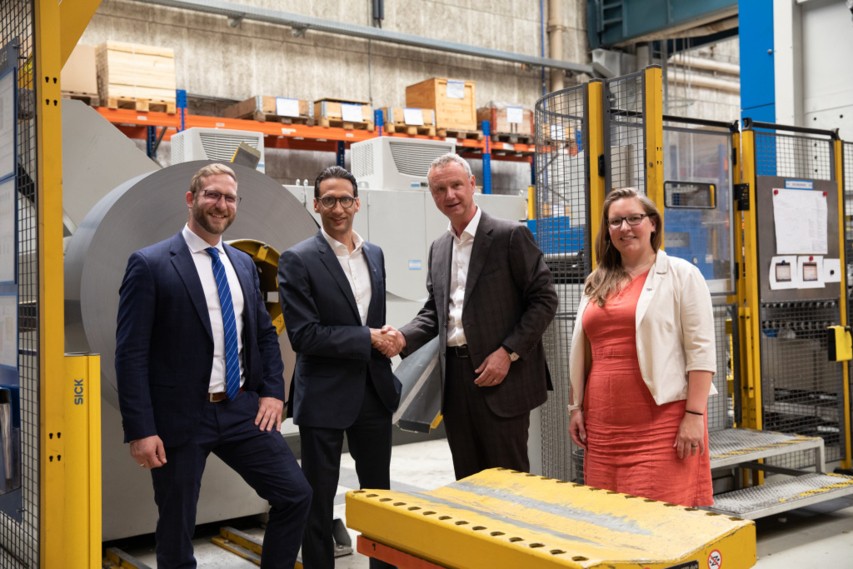
Electrical steel for regional railways: Steel made by voestalpine is found not only in the rails themselves, but also on railways throughout the world. Electrical steel made by voestalpine is used in the drive motors of subways, streetcars and electric buses.
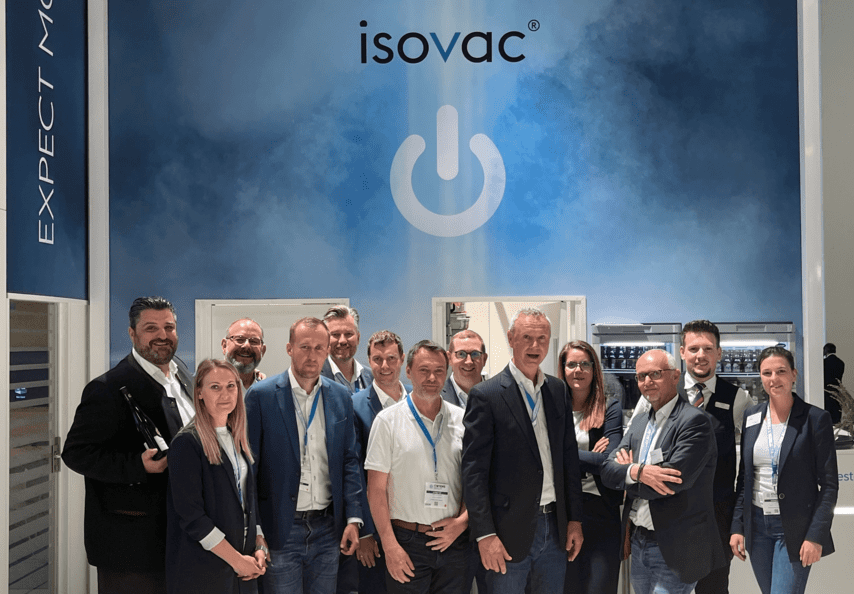
With more than 600 exhibitors and 6.700 visitors in just three days, CWIEME in Berlin showed its true colors after a two-year break. A comprehensive program with more than 80 seminars covering the latest trends and technical developments in electrical engineering and electromobility as well as drive technologies rounded off a perfect trade show.
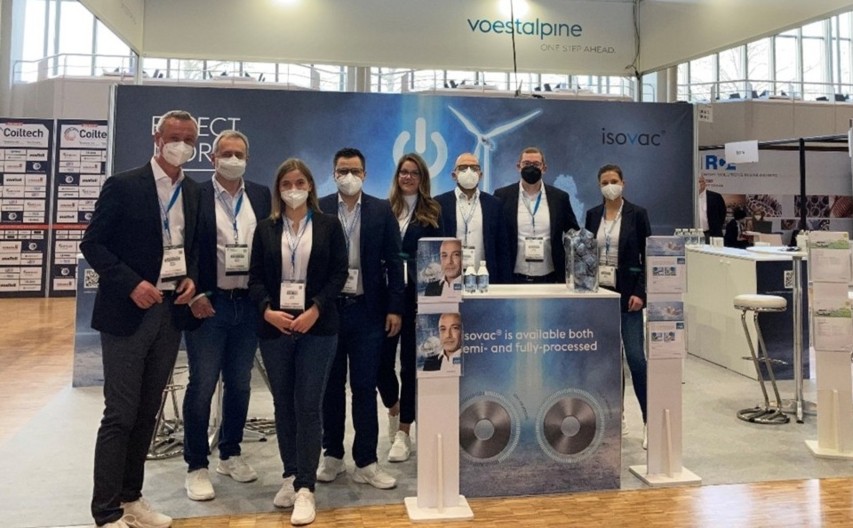
The Coiltech Deutschland, a coil winding expo and conference, took place in Ulm, Germany, for the first time in 2022. Manufacturers and developers of electric motors, generators, transformers and e-mobility solutions presented a variety of different levels of specialization.
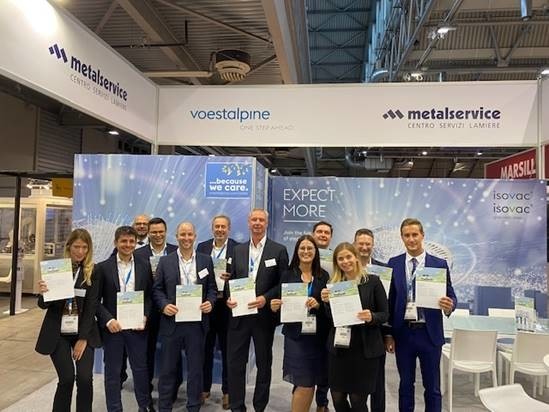
Expect more. Join the future of electrical steel. This was the motto under which voestalpine presented itself in collaboration with Metalservice.
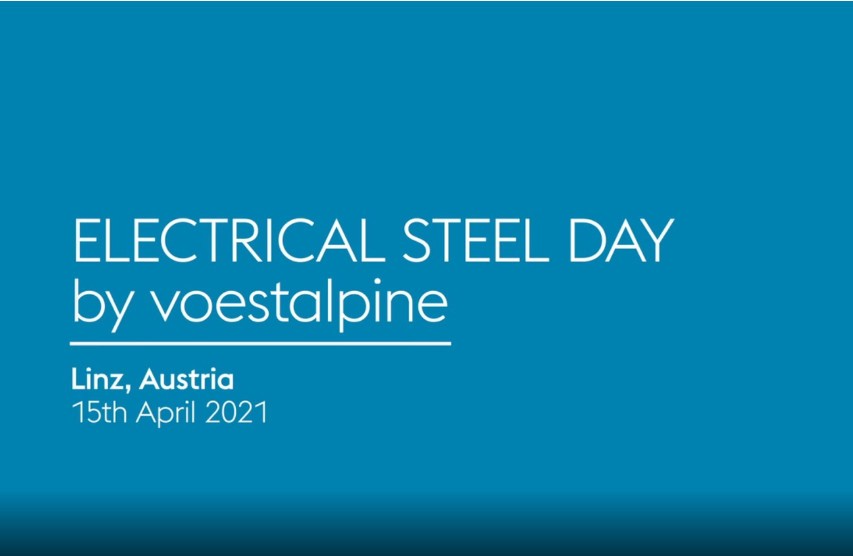
The time after our Electrical Steel Day was actually the time before. The great deal of interest and the large number of participants made it necessary to provide a second chance to those who did not have time for the initial broadcast, which a large crowd also watched.
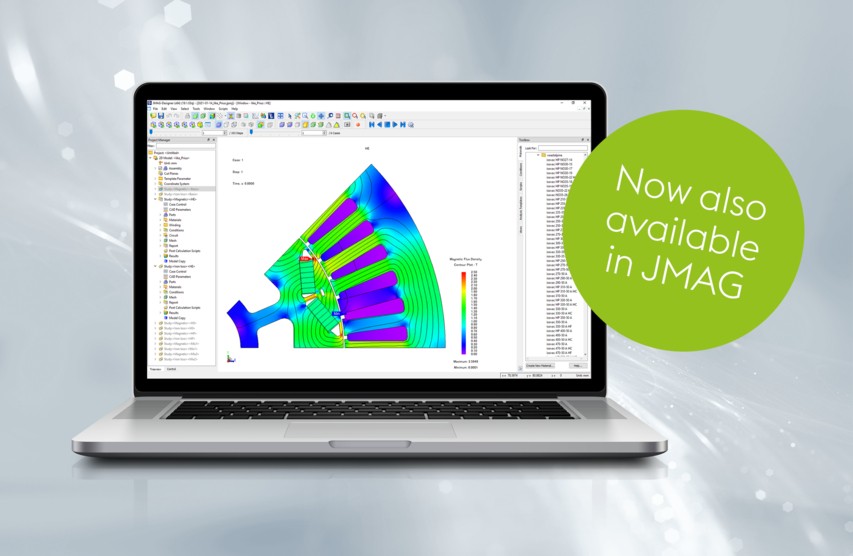
High-precise engine development based on simulations. Let your mind go wild! From now on you can use JMAG to calculate your engine with simulation data from voestalpine.
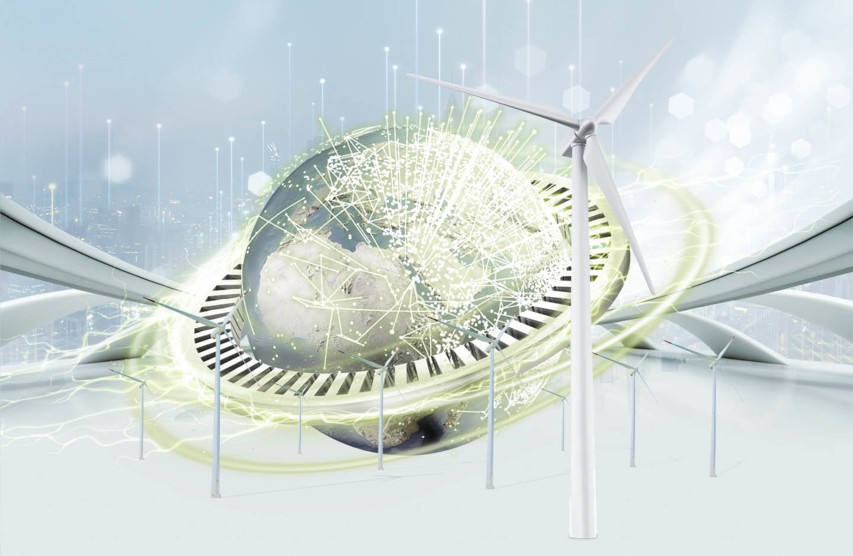
The Steel Division supplies high-quality electrical steel to ENERCON for wind farms in Burgenland.
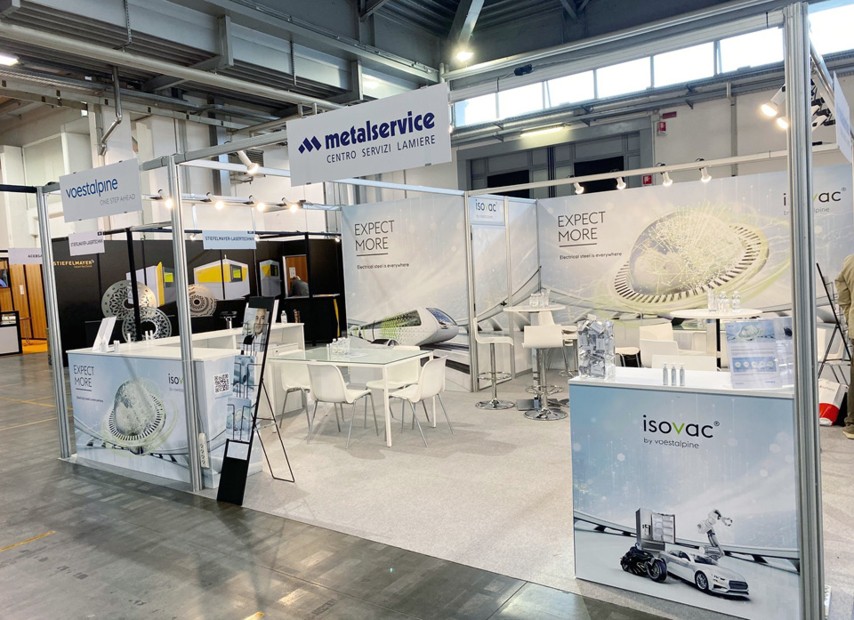
“Expect More” was this year’s motto at the Coiltech in Pordenone. The latest electrical steel innovations were presented in compliance with the safety rules at the first trade fair this year for voestalpine.
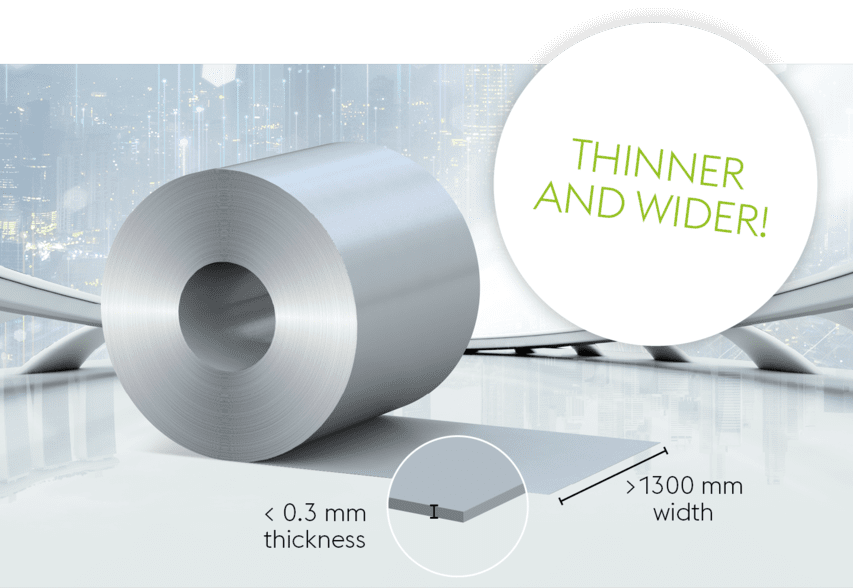
Thin and yet wide? Is this combination feasible for high-alloyed electrical steel? In the following article you will learn which dimensions have become possible—thanks to new investments—with isovac®, the electrical steel strip made by voestalpine.
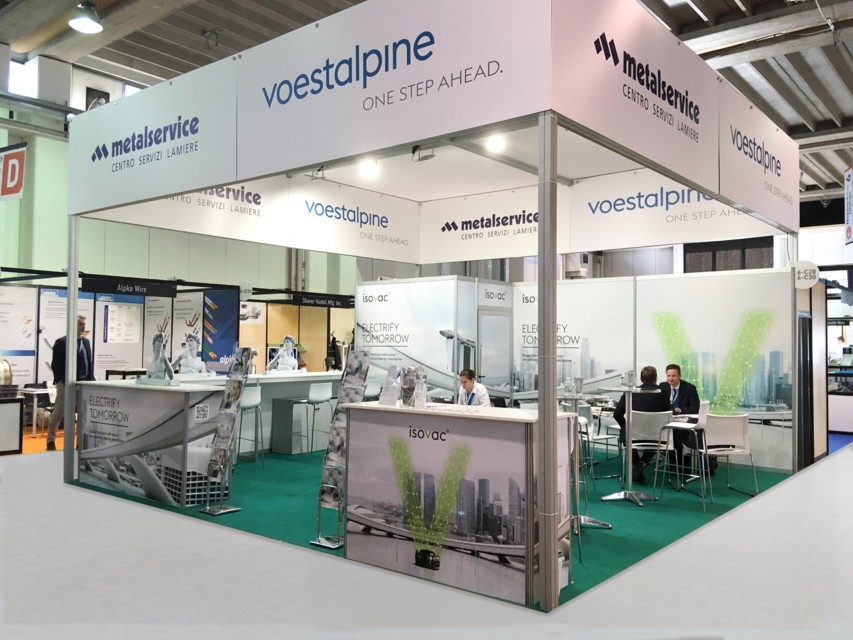
From 25 to 26 September, Pordenone was once again the meeting place for experts in the electrical industry to learn more about the most recent innovations. voestalpine focused on the two main areas of e-mobility and Backlack.
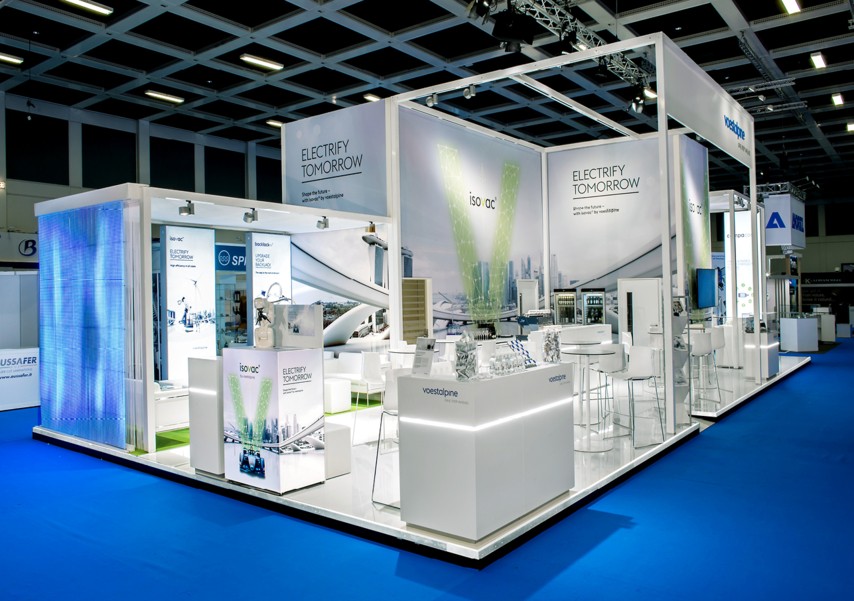
Electrify Tomorrow was the motto of the voestalpine presentation at this year's CWIEME in Berlin. As an official sponsor of Formula E, an electric racing car was of course a must as a trade fair highlight. Technical presentations given by experts and new product developments were met with a great deal of interest. Like last year, the crowning finale was the "Austrian Night." This year’s trade fair was again a great success.
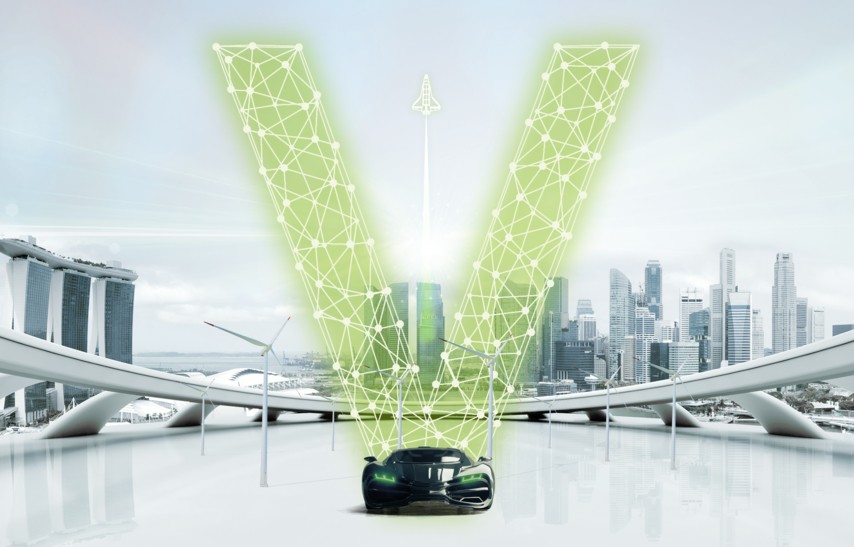
This year's CWIEME once again provides each visitor with an overview of the most interesting technologies and mobility solutions of the future.
Learn surprising new things at the artistic highlight of the exhibition.
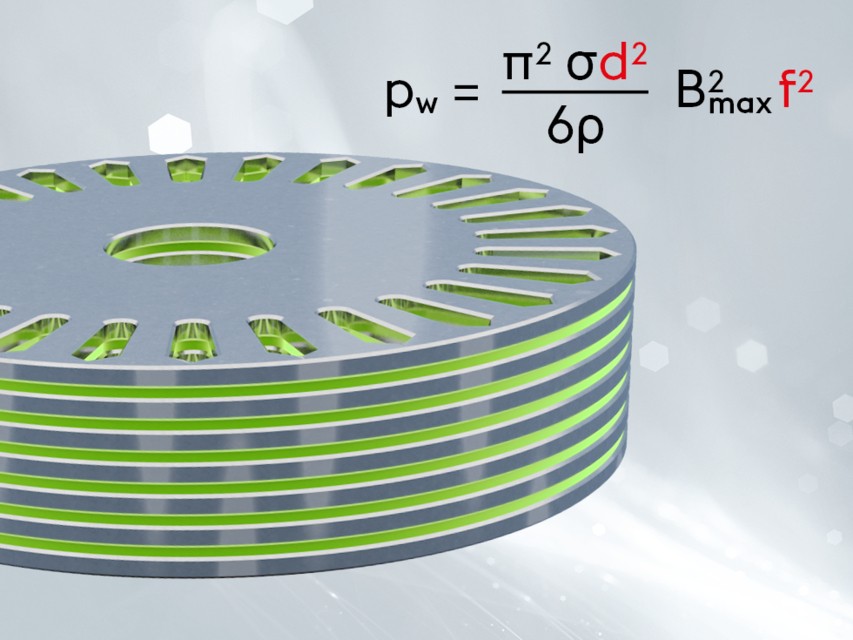
Yes, but not always, not at any price and not in every application. Learn how sheet thickness has an effect on motor efficiency as well as on processing efficiency. Also learn about the connection between sheet thickness, the year 2025 and global stamping capacities. Feel the excitement!
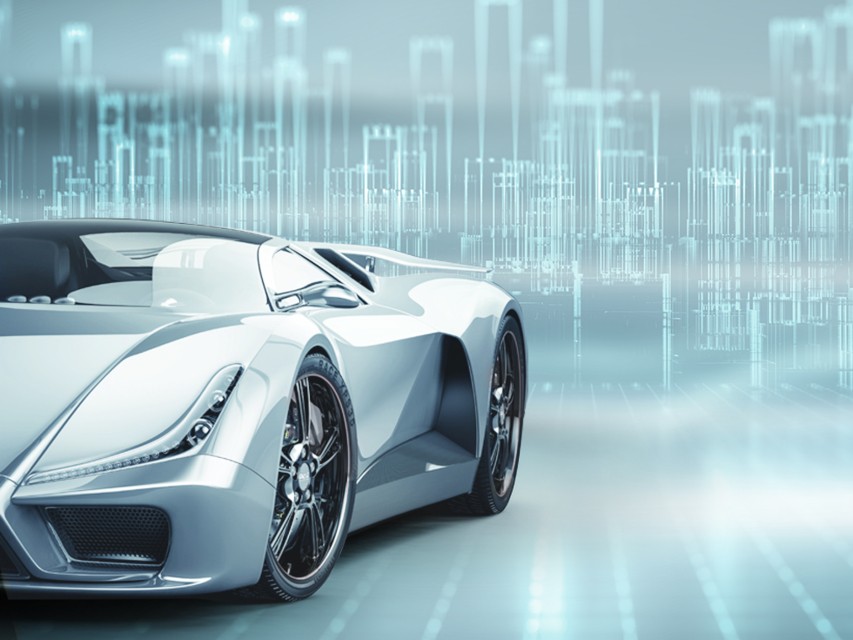
Where does the current of opinions flow with respect to electromobility? An interactive presentation at this year's "Connected by Excellence" provided an overview of further developments in electromobility and insights into the opinions of representatives and experts in the industry.
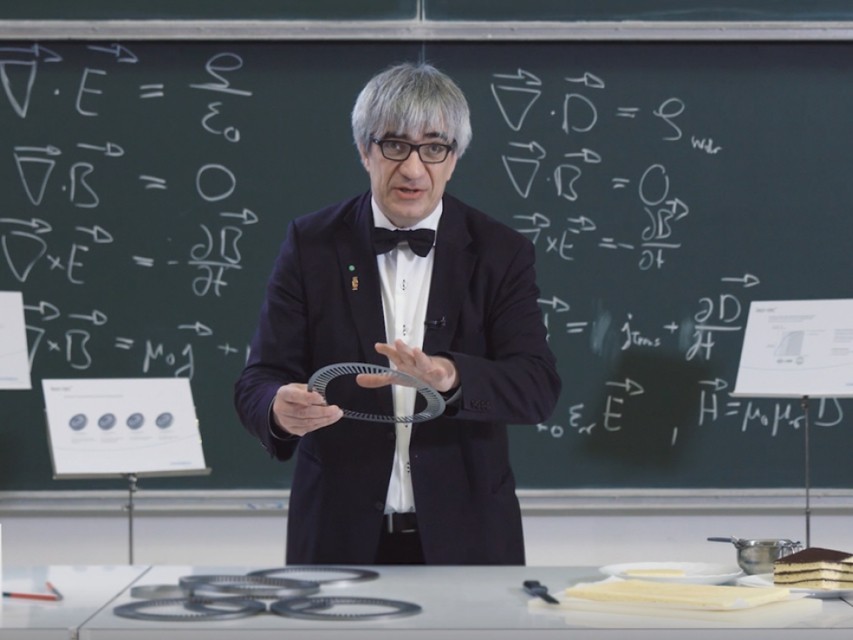
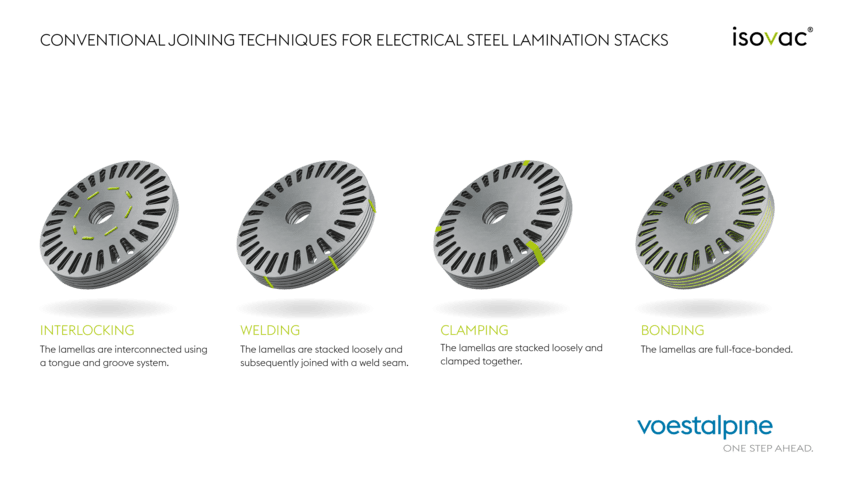
The stator and rotor cores of electrical machinery are manufactured using thin laminations stacked together by our customers in order to minimize eddy current losses. There are several ways to join these laminations, and the most efficient way is to use Backlack.
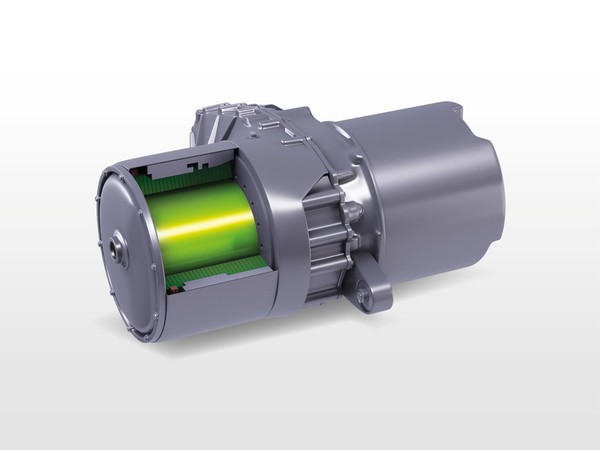
The familiar topics of light-weight design and safety in car bodies will continue to gain significance with increasing electromobility. The need for highly efficient electrical steels for rotors and stators in the drive train is new for many customers. While today more than 100 electric motors are found in every modern car, the manufacture of pre-materials for such motors was less challenging. The new drive motors have changed the picture dramatically.
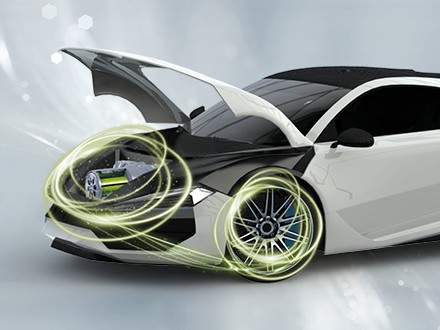
Special motor designs developed in the past few years require the use of particularly high-quality electrical steels. In compliance with these market requirements, we have developed a number of innovative electrical steels. We have given special consideration to pure technical requirements as well as to the workability and availability of the materials.