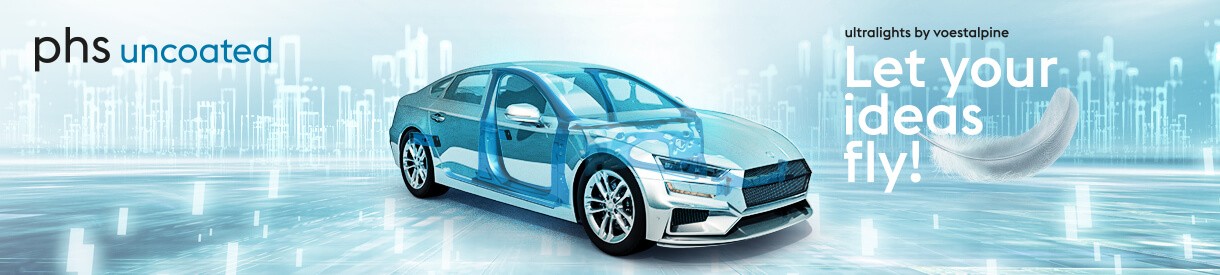
Uncoated hot-forming steels for the production of press-hardened components
The excellent material and processing properties of phs-uncoated steels made by voestalpine make them an efficient and flexibly applicable solution for safety-relevant press-hardened components in lightweight automotive designs in which there are only small amounts of corrosion.
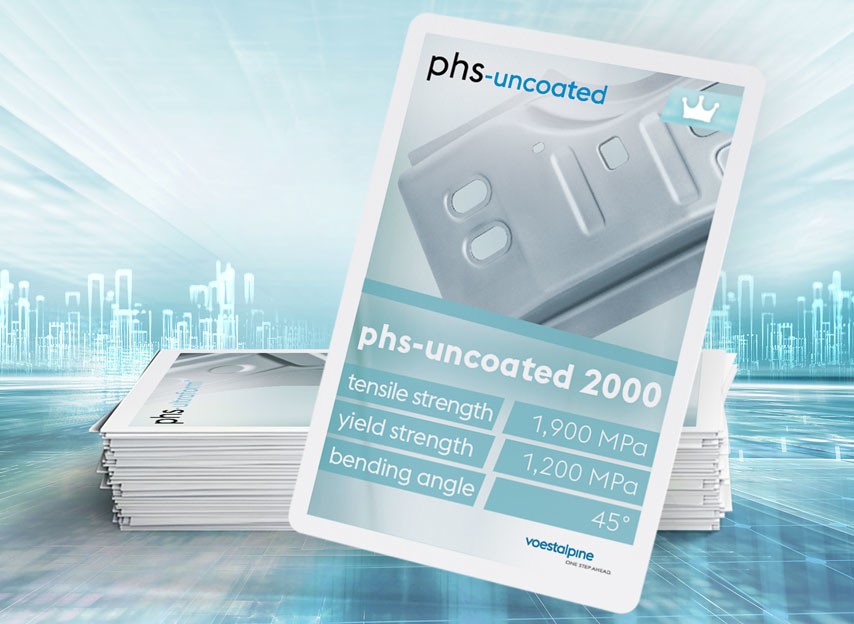
The new ace: phs-uncoated 2000
Press-hardened and hot-formed phs-uncoated 2000 sets an entirely new standard, particularly in vehicle components exposed to very high energy absorption and where minimum deformation is required in the event of a crash. Examples are the protection of the passenger compartment or lightweight battery boxes that can be used safely in electric vehicles.
The phs-uncoated 2000 steel grade boasts tensile strengths above 1800 MPa in hardened condition and can be processed in both the indirect and direct hot forming processes. Both process routes ensure high dimensional accuracy in the components. In unhardened condition, phs-uncoated 2000 also exhibits good cold formability in the indirect process. A further advantage is the excellent joinability, which is why resistance spot welding is possible without any problem.
Tensile strengths above 1300 MPa:
phs-uncoated 1500
The phs-uncoated 1500 steel grade made by voestalpine provides tensile strengths of 1350–1600 MPa in the hardened state. The tensile strength of the unhardened steel strip is approximately 550 MPa and achieves a high degree of freedom during cold forming in the indirect process.
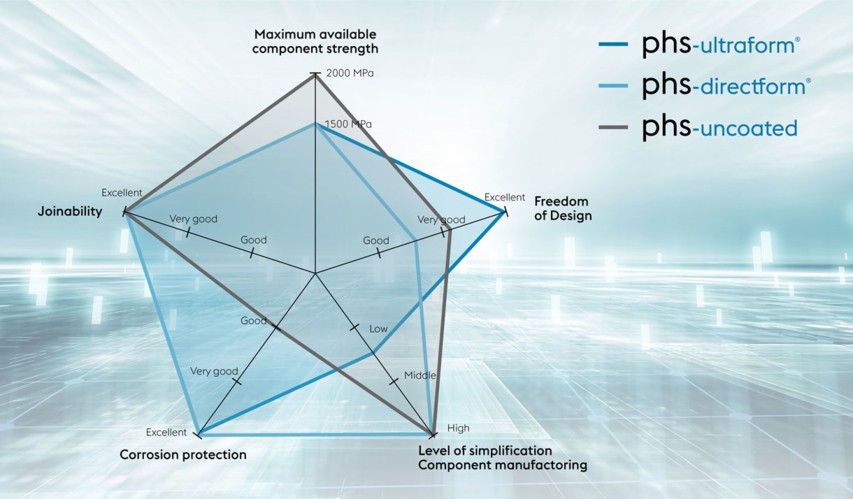
Characteristic values in as-delivered condition | |
Characteristic value | phs-uncoated 2000 CR |
Yield strength Rp0.2 [MPa] | 300-500 |
Tensile strength Rm [MPa] | 450-650 |
Elongation after fracture A80 [%] | ≥ 17 |
Characteristic values in as-delivered condition | |
Characteristic value | phs-uncoated 2000 HR |
Yield strength Rp0.2 [MPa] | 280 – 680 |
Tensile strength Rm [MPa] | 440 – 850 |
Elongation after fracture A80 [%] | ≥ 10 |
Typical characteristic values in hardened condition | ||
phs-uncoated 2000 CR/HR | ||
Characteristic value | Hardened | Hardened + BH* |
Yield strength Rp0.2 [MPa] | 1200 | 1400 |
Tensile strength Rm [MPa] | 1900 | 1850 |
Elongation after fracture A80 [%] | 5 | 5 |
Bending angle at 1.0 mm | 45 | 50 |
* Increased yield strength as a result of the bake-hardening effect |
Carbon footprint greentec steel product
greentec steel product | Maximum carbon footprint [kg CO2e/kg steel] 1) |
Hot-rolled steel strip | 2.10 |
Cold-rolled steel strip | 2.20 |
1) The carbon footprint is calculated pursuant to worldsteel CML 2001-2016 (system expansion) on a cradle-to-gate basis.
All products, dimensions and steel grades listed in each voestalpine supply range are available as greentec steel.
Multiple uses
phs-uncoated steels are also used in welded blanks, so-called tailor-welded blanks (TWB) or tailor-rolled blanks (TRB). The phs-uncoated 2000 steel grade is available in wide strips, slit strips, blanks or tailor-welded blanks in combination with other steel grades or different thicknesses. Tailored-heating and tailored-cooling technologies can also be applied during press hardening.
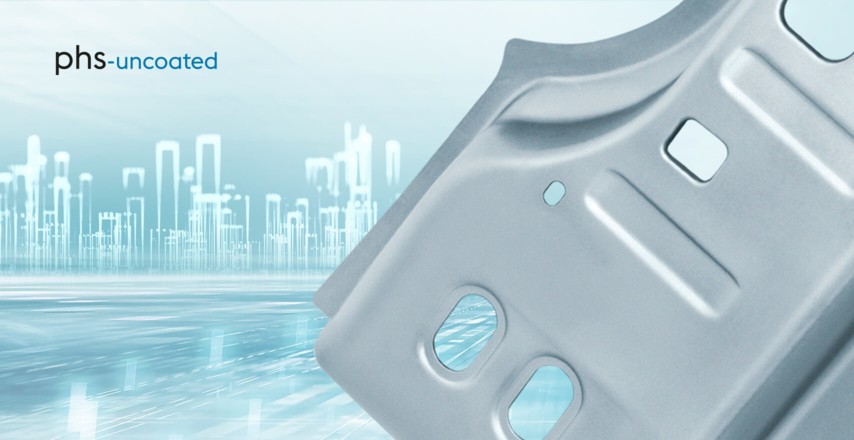
Overview of benefits
- Best crash behavior
- Very good joining behavior
- Components also available as tailored-property parts (TPP)
EN 10338 and EN 10346 | VDA 239-500 | Special voestalpine grade |
- | - | phs-uncoated 1500 |
- | - | phs-uncoated 2000 |