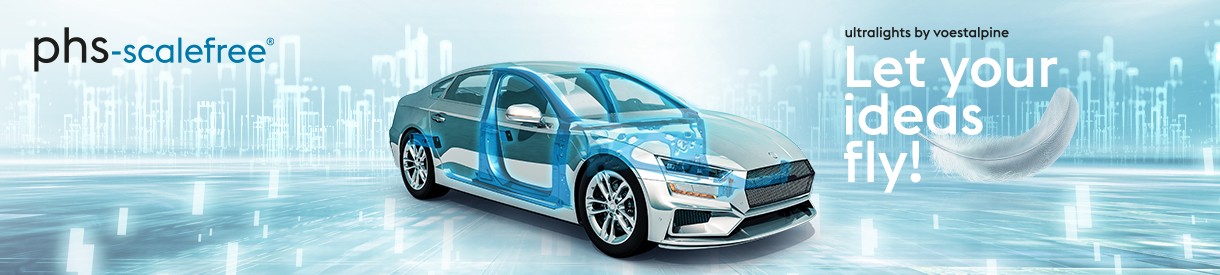
The first hot forming steel up to 2000 MPa with a thin zinc coating
phs-scalefree 2000 is a special development in the field of lightweight automotive design that opens up new perspectives for the manufacture of high-strength components.
The single-phase zinc-ferrite coating is our secret for success. It ensures excellent scale protection with outstanding hot forming properties and provides additional corrosion protection.
phs-scalefree® is the quality solution for B pillars or internal structural components. Galvanized manganese-boron steels for hot forming are also recommended for large components and are easier to form than uncoated or hot-dip aluminized PHS steels.
Mission accomplished. Zinc-coated steel up to 2000 MPa.
The new steel solution strengthens the position of voestalpine as the PHS specialist. phs-scalefree® was specifically developed to optimally complement the extensive portfolio of press-hardening steels for hot forming.
Unbeatable in manufacturing and component quality
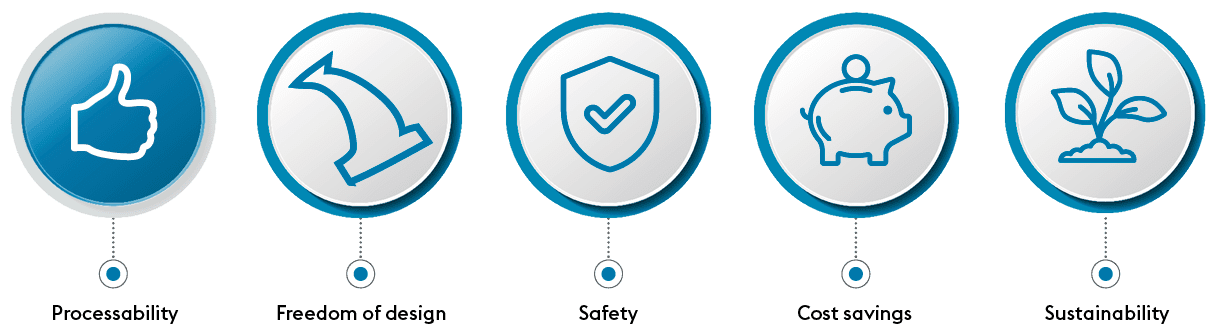
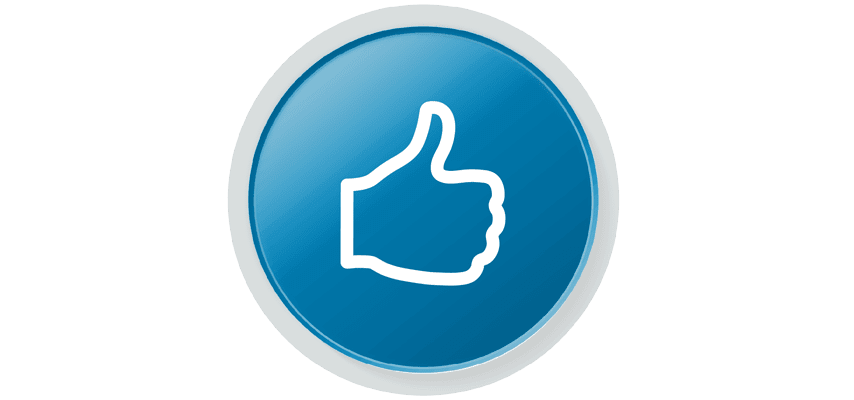
Thin zinc coating for high level of processability
- No special PHS furnace atmosphere required. The zinc layer protects the PHS surface from scaling, and the high emissivity of the zinc-iron surface ensures rapid heating.
- During coating and throughout corrosion process, the single-phase zinc-iron coating leads to reduced hydrogen absorption when compared to multi-phase zinc-iron coatings and thus protects components from cracking.
- phs-scalefree® can be hot-formed using either the direct and indirect process.
phs-scalefree® steels have very good adhesive bonding properties because of their special surface.
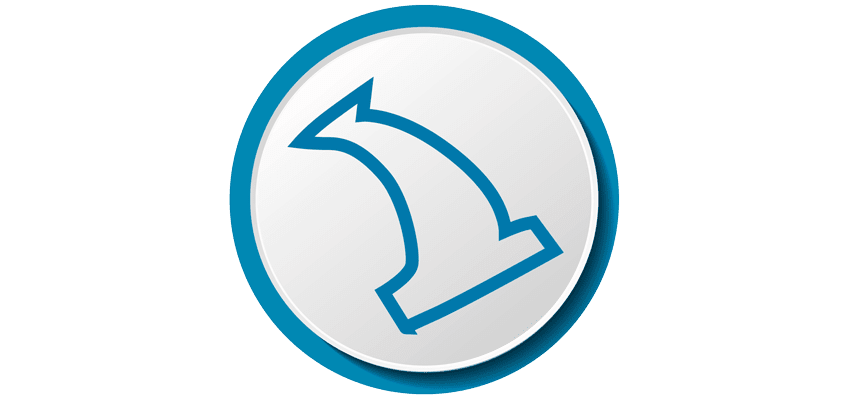
PHS process for freedom of design
- In the direct process, geometries can be varied as a result of lower friction in the hot forming-tool (when compared to uncoated or hot-dip aluminized PHS steels).
- Complex geometries, including undercuts, are possible in the indirect process as a result of cold forming in the initial process step.
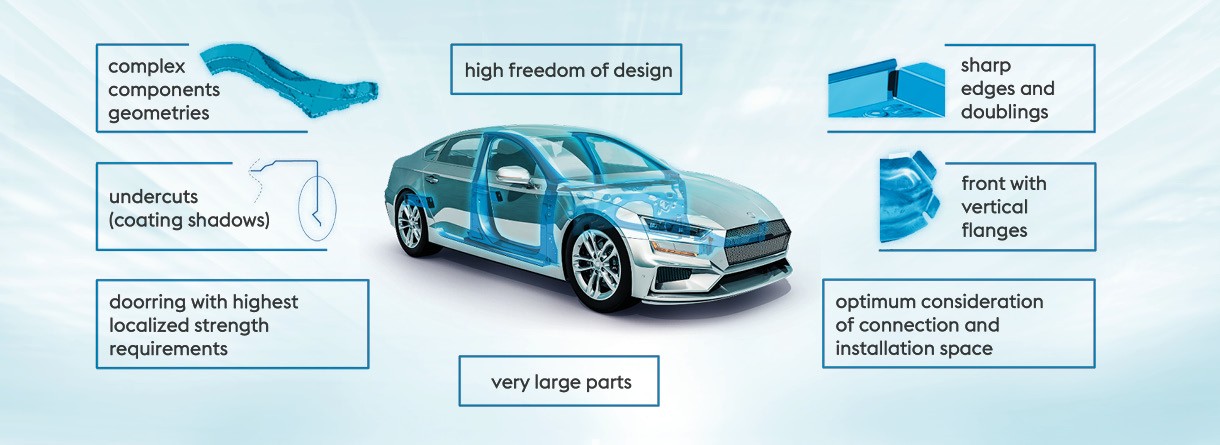
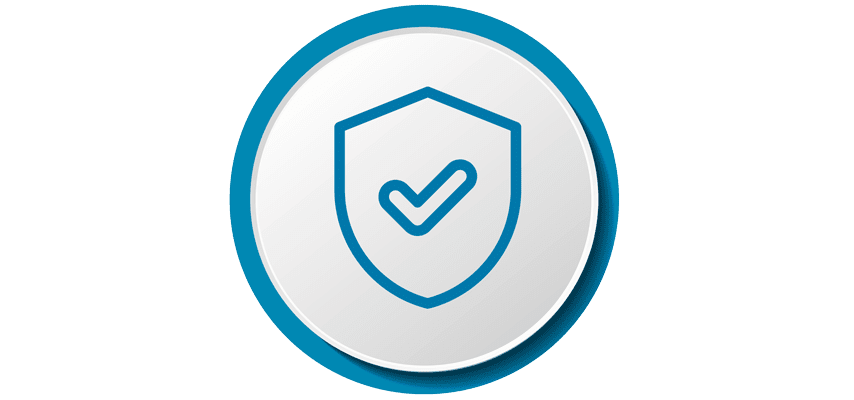
High-strength components for greater safety
- The high-strength components guarantee the best crash performance with the lowest weight.
- The single-phase zinc-ferrite coating protects the components from corrosion.
- The experts at voestalpine will provide advice and support from component design to production.
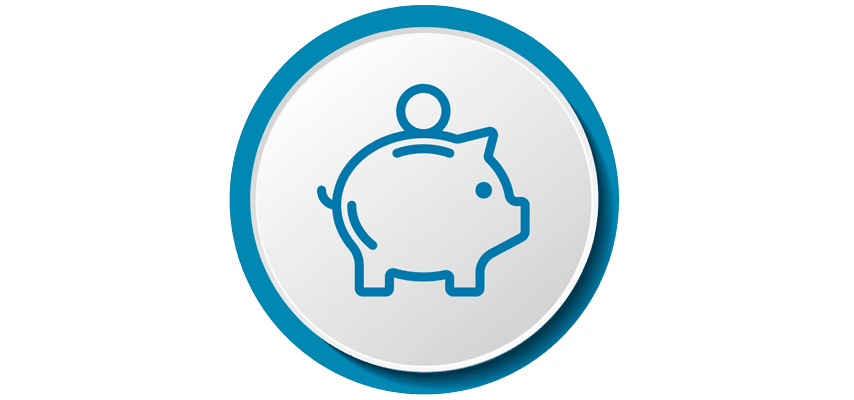
Scale protection for higher cost-savings
- The clean and scale-free processes ensure longer tool service life, reduced part cleaning requirements and longer tool cleaning intervals, which leads to savings in the forming process.
- The reduction of tool deposits and low tool wear also ensure consistently high component quality.
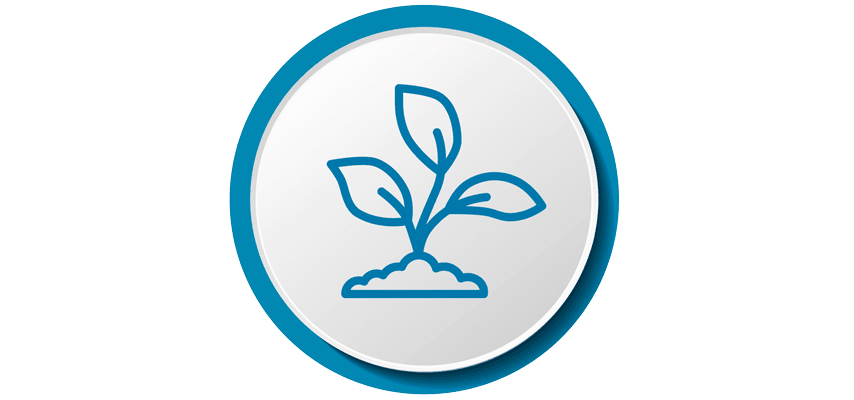
Lightweight design for sustainability
- High strengths up to 2000 MPa ensure lower wall thicknesses, lighter vehicle weights for lower fuel consumption and reduced carbon emissions.
- The press hardening technology also enables larger components. Material usage as well as the number of parts and joints can be reduced.
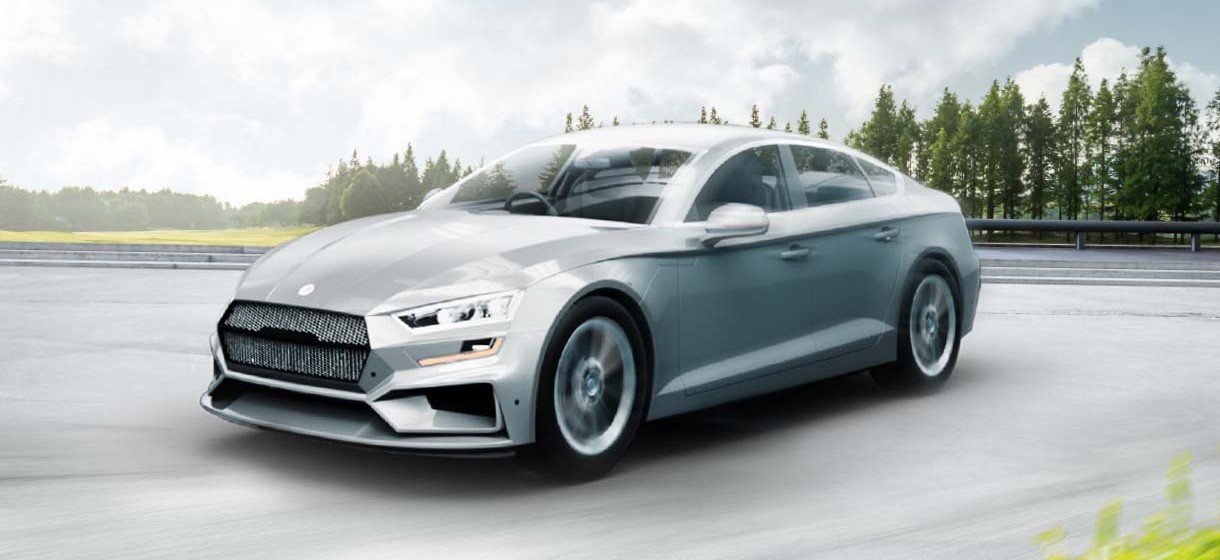
EN 10346 | VDA 239-500 | Special voestalpine grade |
- | - | phs-scalefree 2000 |
- | - | phs-scalefree 1500 |
- | - | phs-scalefree 490 |
Carbon footprint greentec steel product
greentec steel product | Maximum carbon footprint [kg CO2e/kg steel] 1) |
Hot-dip galvanized steel strip | 2.30 |
1) The carbon footprint is calculated pursuant to worldsteel CML 2001-2016 (system expansion) on a cradle-to-gate basis.
All products, dimensions and steel grades listed in each voestalpine supply range are available as greentec steel.