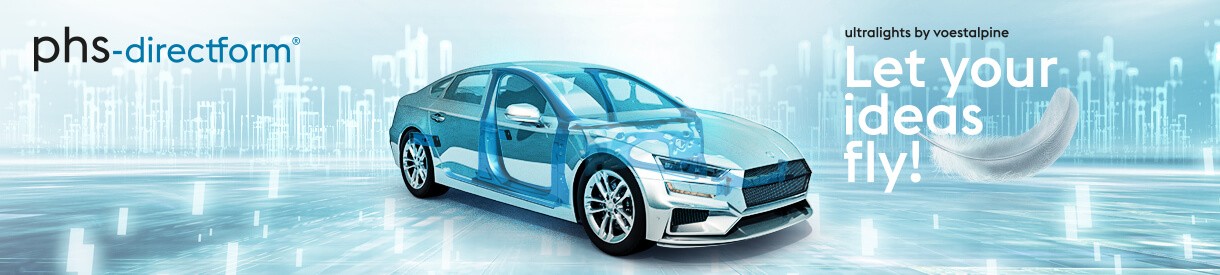
Galvanized hot forming steels for the production of press-hardened components using the direct process
The world novelty developed by voestalpine is directly hot-formed, hot-dip galvanized steel strip to be used in corrosion-resistant light-weight components for the automotive industry.
phs-directform® is the technically simple, safe solution for complex components and high efficiency, even in small quantities. The material is suitable for forming in existing and adapted direct-hot-forming lines. phs-directform® boasts of excellent strength, is suitable for joining, and its excellent corrosion protection make it recommendable for structure and body crash components.
EN 10338 and/or EN 10346 | VDA 239-500 | voestalpine special grades |
- | - | phs-directform 1500 |
- | - | phs-directform 490 |
Carbon footprint greentec steel product
greentec steel product | Maximum carbon footprint [kg CO2e/kg steel] 1) |
Hot-dip galvanized steel strip | 2.30 |
1) The carbon footprint is calculated pursuant to worldsteel CML 2001-2016 (system expansion) on a cradle-to-gate basis.
All products, dimensions and steel grades listed in each voestalpine supply range are available as greentec steel.
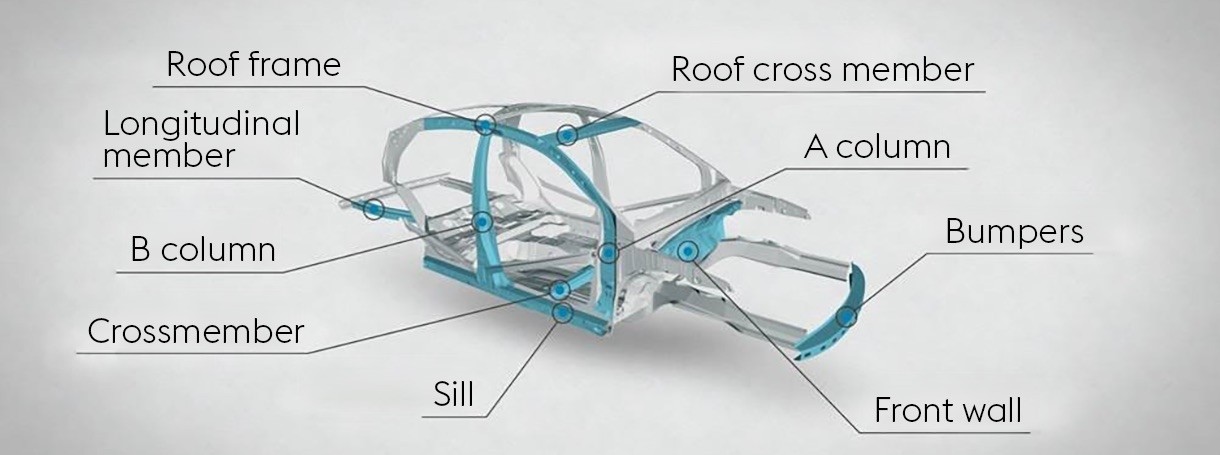
Advantages of phs-directform® in detail:
- Exceptional cathodic corrosion protection
- Press-hardening steel, perfect for lightweight automotive design
- Economical manufacturing
- Simple process steps
- Less material usage
- Good crash performance (ductility)
- Strengths to 1,500 MPa
- Excellent processability
- Brilliant paintability
- Suitable for tailored-property parts
- Standard transport corrosion protection
The innovation for complex components made of press hardened steel
The blanks are heated to roughly 900 °C. This is followed by an innovative non-contact pre-cooling process that uses air to cool below 550 °C in an effort to prevent microcracks. During the subsequent forming process, the blanks are brought to their final geometry and hardened. Tailored-property parts can also be manufactured from laser-welded blanks.
Overview video at the click of your mouse:
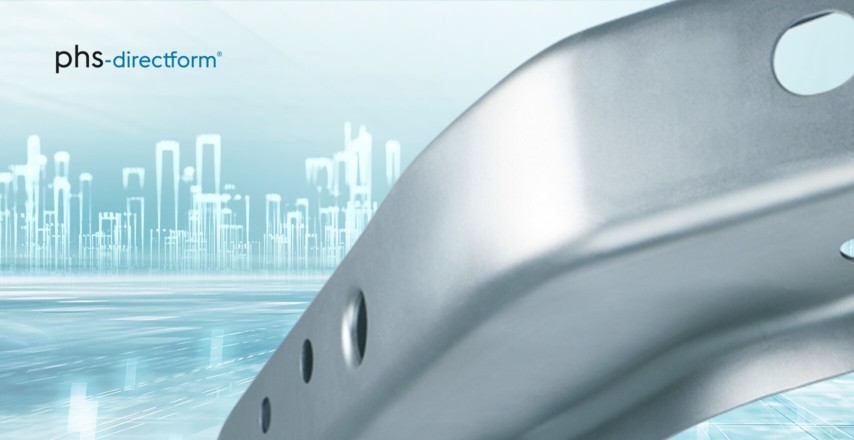