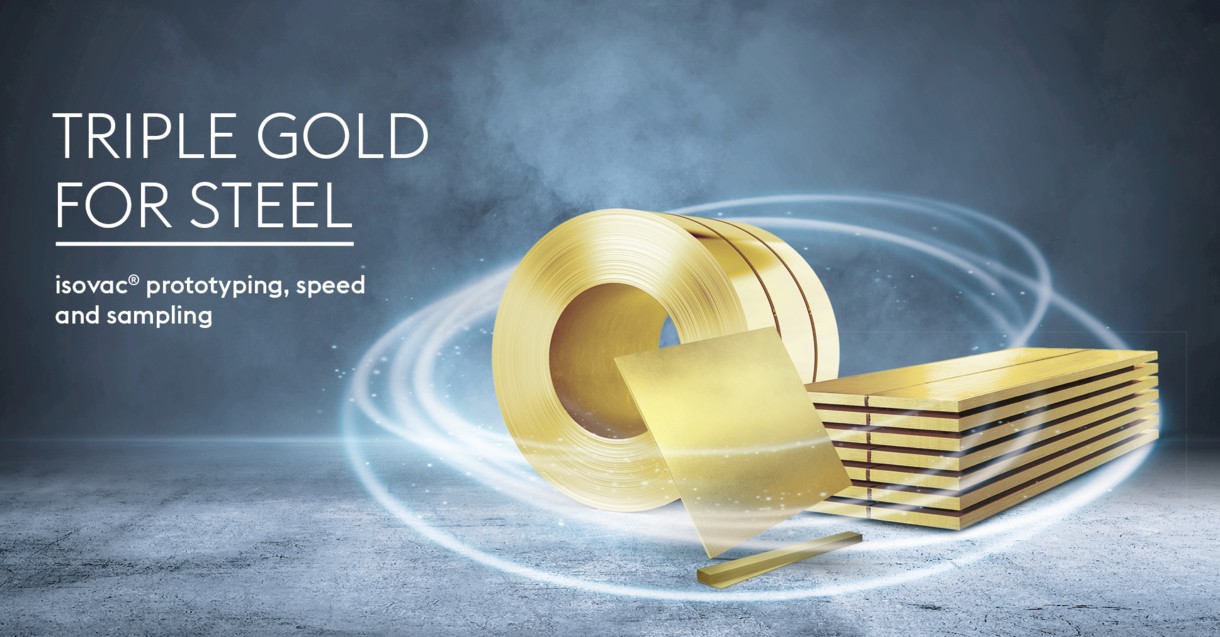
isovac® prime services - TRIPLE GOLD FOR STEEL
At voestalpine, we combine isovac® with our unique services to provide the best package of innovative materials, commercial recommendations, technical consultation and logistics. With isovac® prime services, voestalpine takes its performance one step further.
To be accurate, there are three main benefits: Rapid supply of selected steel grades to meet short-term requirements, small quantities of our highest-quality electrical steels supplied for the creation of prototypes and the possibility of receiving quickly supplied samples for testing in your own lab.
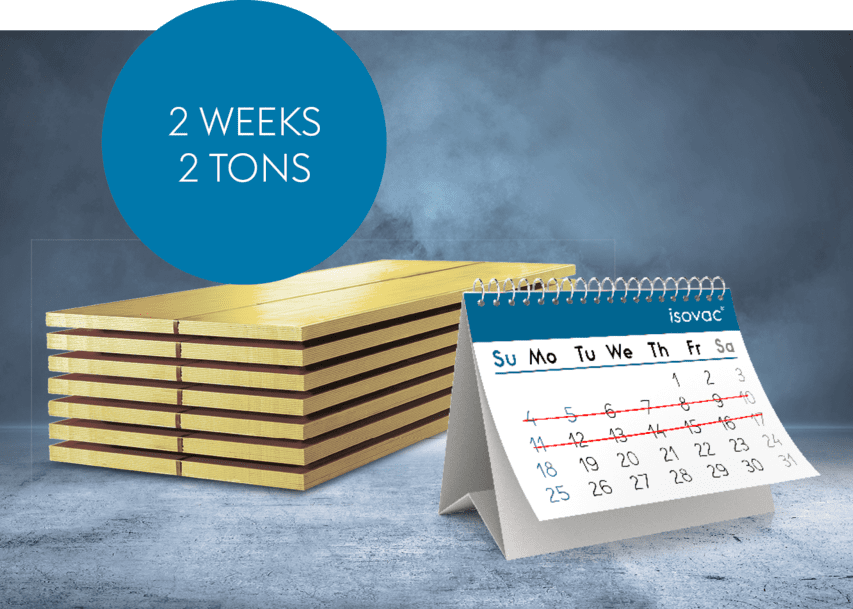
isovac® prototyping
Innovative motors require innovative and highly efficient electrical steel. Data sheets and simulation calculations make it possible to pre-select just the right steel grade. But how good is the performance of the material in the motor? In efficient prototyping, quantities smaller than the conventional coil and rapid supply play a major role. voestalpine supplies a number of high-quality steel grades in the form of sheet material in small quantities with a guaranteed manufacturing time of only two weeks for existing customers.
isovac® speed
Planning horizons are becoming shorter and shorter, and it is often difficult to meet short-term end customer requests. In compliance with market demand, voestalpine provides the possibility of ordering a selection of high-quality electrical steel grades with up to 50% shorter delivery times. Materials upon request while supplies last.
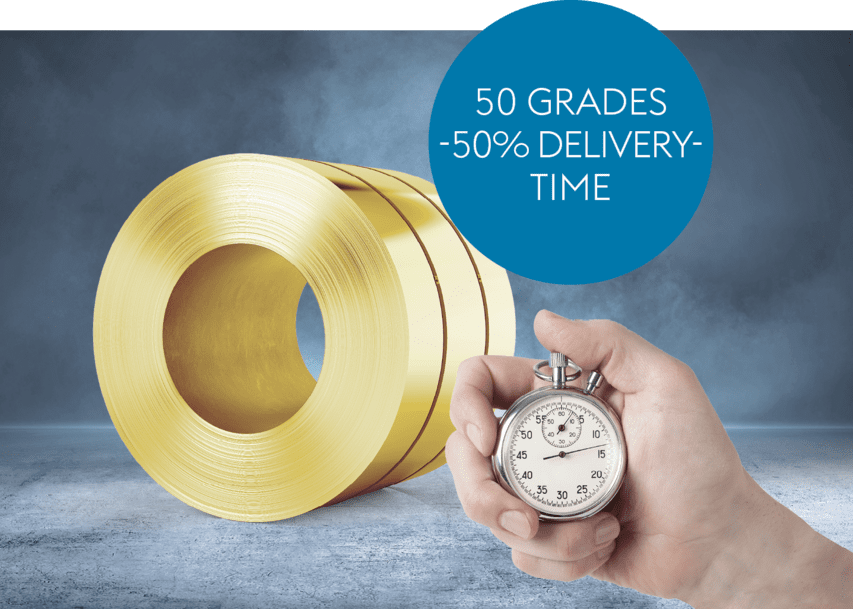
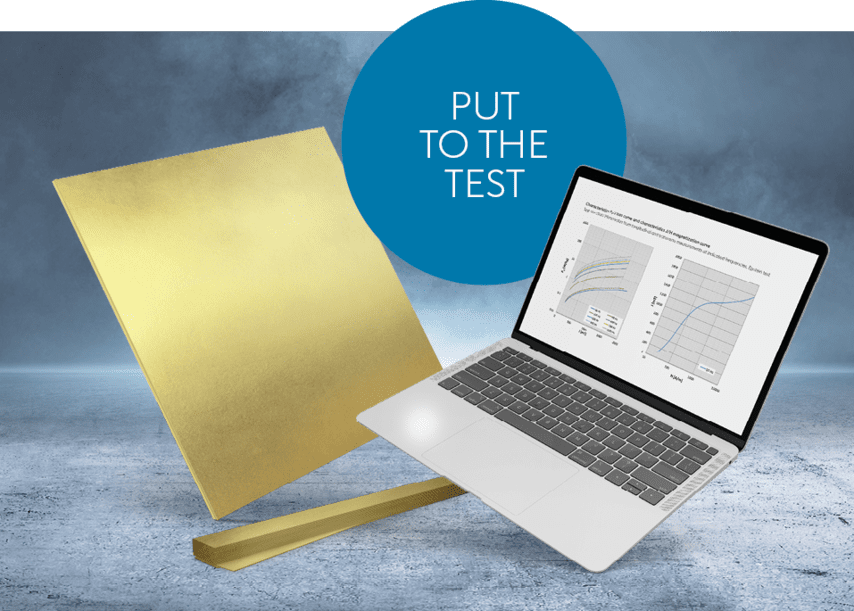
isovac®sampling
The range of property profile requirements of innovative electrical steels is steadily becoming broader. Selecting the optimum steel grade has been simplified by a wide range of magnetic, mechanical or physical data provided by voestalpine. Do you want to conduct additional measurements using your own company equipment? Not a problem. Convince yourself of the exceptional properties of isovac electrical steel.