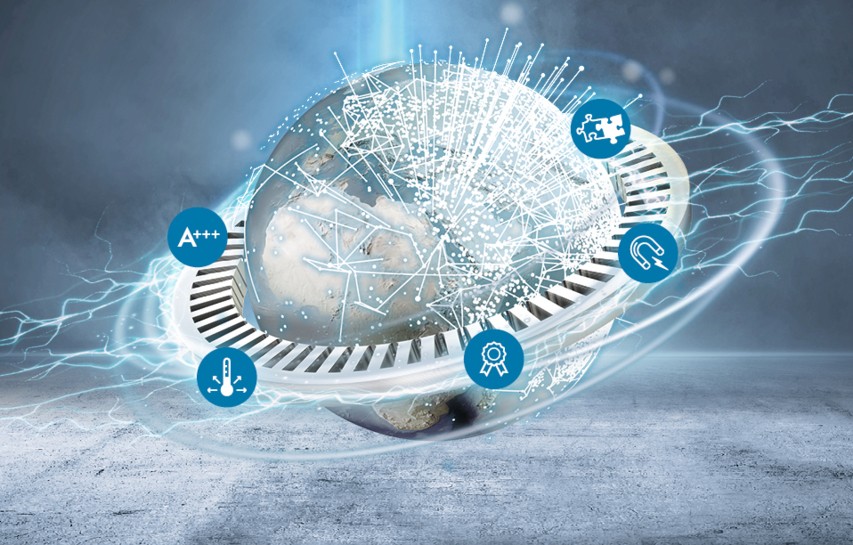
Best product properties for maximum performance
isovac® electrical steel for highest energy efficiency. We combine isovac® with our unique services, innovative materials, logistics, commercial advise and technical consultation in order to provide you with a comprehensive package of benefits.
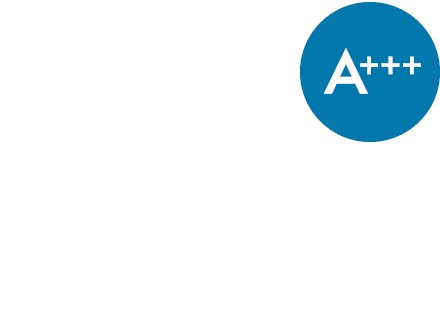
Maximum performance
Low eddy-current and hysteresis losses in electrical steel is of decisive importance in order to be able to efficiently utilize the energy used in the operation of electrical machinery. The most modern production facilities guarantee the production of electrical steel for the highest performance of electrical machinery.
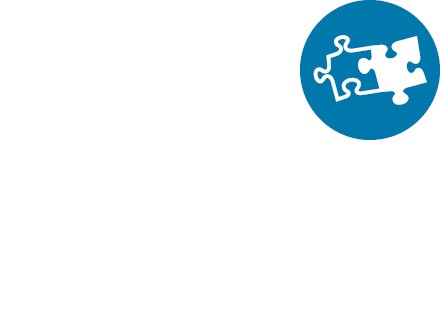
Customized product properties
The exclusive manufacturing of prematerial in our integrated metallurgical facilities makes it possible for us to unceasingly monitor and ensure the high quality of all processing parameters. This results in a tailor-made product that meets the highest quality standards.
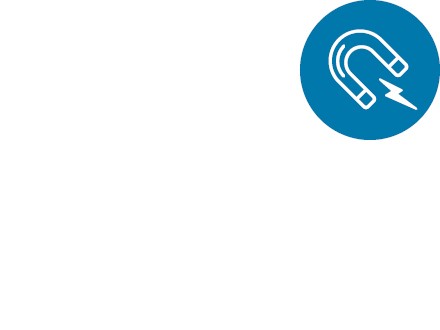
High magnetic polarization and permeability
Magnetic polarization and permeability are essential values in the engineering of electrical machinery. Only high induction allows efficient utilization of available energies.
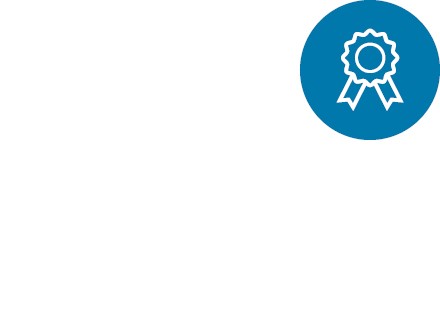
Material homogeneity
High process reliability and low tolerances through continuous rolling and annealing processes make it possible for us to guarantee homogeneous material for improved mechanical, magnetic and geometric properties. This leads to stable material processing, low tool wear, less scrap, fewer rejects and high dimensional accuracy of the stamped part.
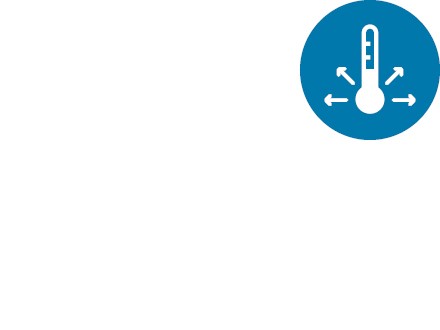
High thermal conductivity
High thermal conductivity permits further optimization of performance. The innovative alloy design and the high chemical degree of purity of isovac® grades significantly increases thermal conductivity.
Precision in processing
For more efficiency in processing We are fully committed to the state-of-the-art technical product properties demanded by the market. Our claim to narrow shape tolerances and processability goes much further.
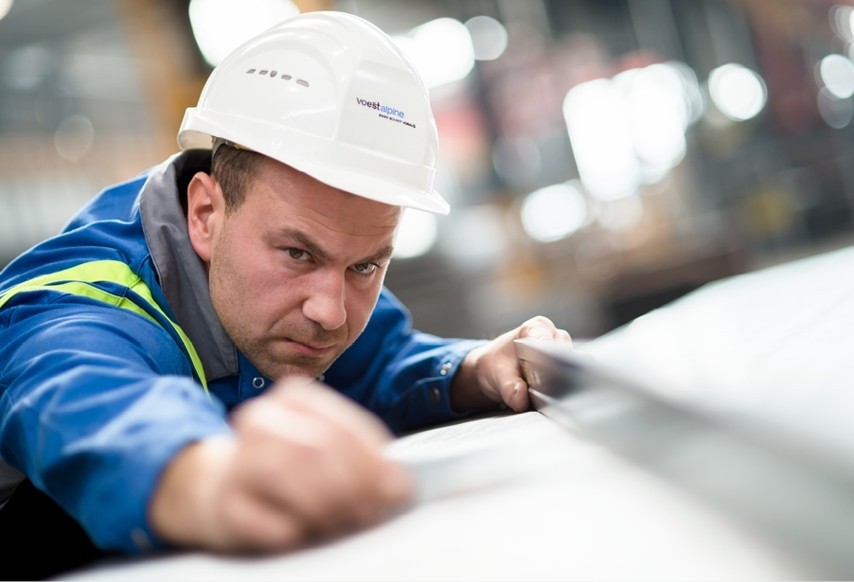
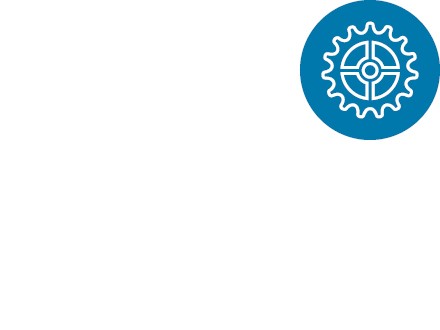
Mechanical properties and insulation
Mechanical properties guarantee both the functionality of rotating electrical machinery and, more importantly, the processability of the steel strip. Consistent mechanical properties as well as clean surfaces that cause minimal abrasion on the punching tool are prerequisites to optimized punching processes. One possibility of reducing tool wear and improving the punching process is the application of an insulating layer on the steel surface. The layer acts as an insulator and is especially effective in providing lubricating action for the punching tool.
- Uniform mechanical properties
High chemical material purity
Very good adhesion between the material and insulation
Continuous insulation thickness
No defects in insulation
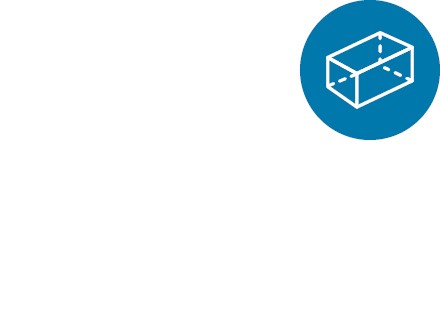
Geometric properties
The result of our stable and continuous rolling process is a reduction in the steel strip thickness tolerance value. The subsequent continuous annealing makes it possible for us to reduce material stress to a minimum and manufacture components with the highest precision.
- Narrowest tolerances in the strip in both longitudinal and cross direction for consistent package parallelism
No damage to slit edges and strip surfaces
Low stress in hot-rolled and slit strip (no strip waviness, high shape consistency)
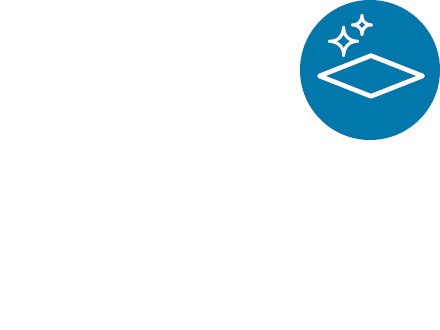
Cleanliness
Consistent mechanical properties, narrowest tolerances and clean strip surfaces must be continuously guaranteed in order to allow efficient and problem-free processing. We minimize production residues as far as possible. Additionally, extremely abrasion-proof insulation coatings with good adhesion properties can be applied to the steel surface.
Good insulation adhesion
Minimum abrasion during splitting and punching
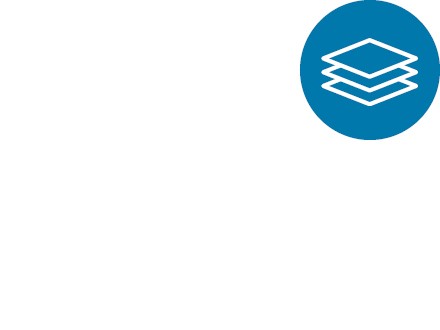
Adhesive bondability
A successful adhesive bonding process is dependent on the bondability of the insulation on the steel surface. For example, Backlack is a special insulating varnish for electrical steel. The main purpose of this varnish is to bond the individual lamellas with each other and create a compact laminated core without any short circuits. The use of Backlack allows us to achieve very complex geometries.
- Surface free from dust, oil, grease and silicon residues
High level of insulation adhesion,
optimized for full-surface bonding
Homogeneous adhesive bonding
Innovative coatings with Backlack and backlack-v®