The data speaks for voestalpine: Best service for forming and crash simulation
The old adage that you’re always smarter in hindsight is now history! This is true at least in the development of new components for lightweight automotive design. Simulation software makes you smarter beforehand, and it can save you time and money.
The basis for this is the relationship between important variables in the steel and forming and crash behavior. The voestalpine material data for forming simulations are provided for common simulation programs, and characteristic data for crash simulations are available upon request.
Simple availability is our forte.
The voestalpine material cards for Autoform can be downloaded directly from the home page.
They are available for PAM-Stamp and Stampack in the material database included in the software. The material cards for LS-Dyna can be ordered directly from voestalpine.
The entire voestalpine spectrum of cold-rolled materials is available for material selection, and material cards are available for selected hot-rolled steels. Work is currently underway on the creation of material cards for hot-formed materials. These can be validated based on test results with your own tools.
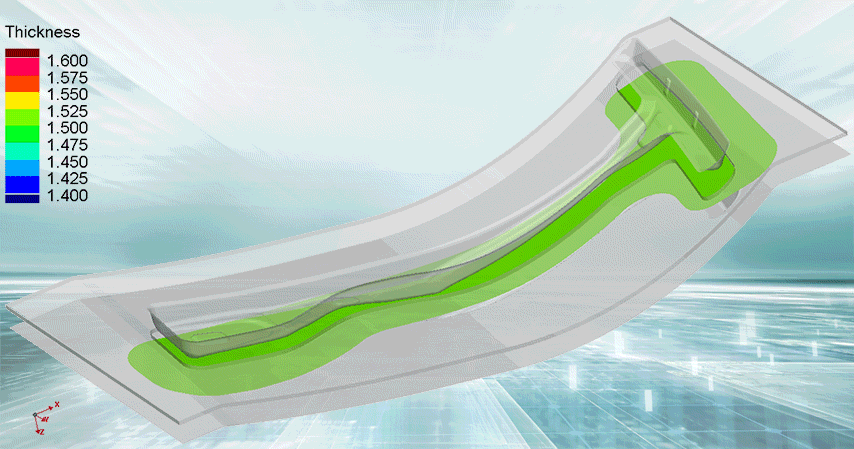
Personal program support
The material cards for forming steels as well as for high-strength steels for crash simulations (LS-Dyna, PAM-Crash, Radioss and Abaqus) can be obtained free of charge. Dr. Gernot Trattnig, voestalpine R&D, Simulation of Forming Technologies, explains it in simple terms:
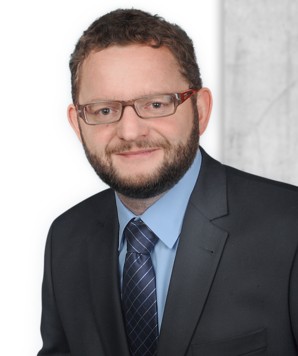
voestalpine is your most reliable partner when it comes to challenging tasks and complex components. Because of our close cooperation with customers, we know their requirements first-hand. We work together to find the right solutions, which are based on material data alone. In turn, personal contact helps us to optimize our material data and models in order to provide them in the right form at the right time. This leads to maximum benefit for the customer and helps us further improve our services.
Dr. Gernot Trattnig, Research and Development, Simulation of Forming Technologies
The proof of the pudding is in the eating
Precise simulation of the entire forming process enables rapid verification of several alternatives. It helps us identify critical points in component design (see animation). In order for this to be calculated using the finite element method, basic data is required. These data are determined empirically in series of extensive testing. The innovative strength of voestalpine in the development of new materials helps you to find the optimum solution to your design and to meet your special requirements.