The Key to the Green Factory
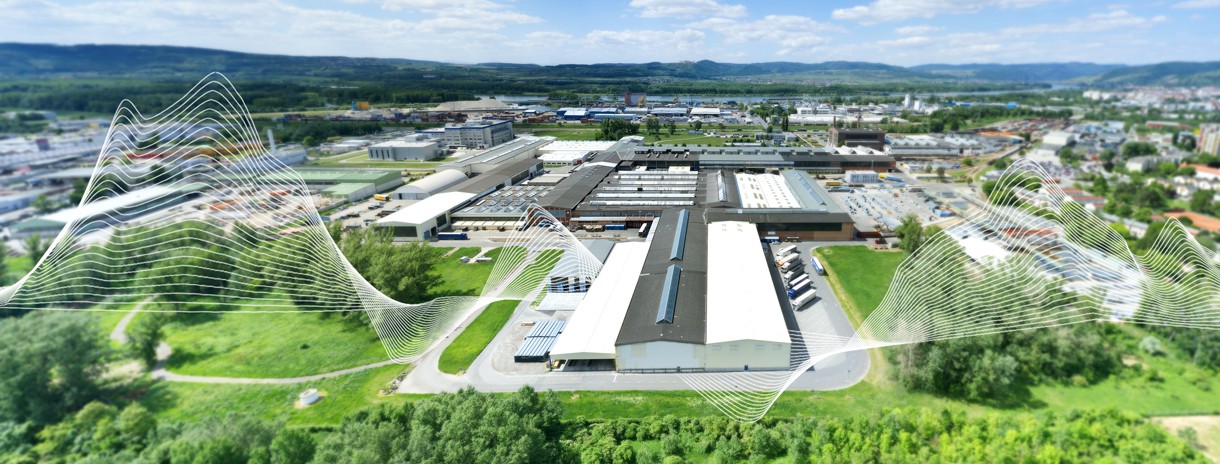
The companies of the Metal Forming Division set new standards with their high quality solutions for automotive components, profiles, tubes, sections, rack systems and precision strip steel products. In the future, it will not only be important what you produce, but how CO₂-intensively you produce. The Metal Forming Division is making the Green Factory a reality.
Green Factory in each business unit
The Metal Forming Division has a mission: The entire division will be CO₂-neutral by the year 2035. The Green Factory is the vision for each of the four business units:
- Automotive Components
- Tubes & Sections
- Precision Strip
- Warehouse & Rack Solutions
Discover sustainable information
The four business units differ not only in their product portfolios, but also in the various production processes. Different procedures and processing steps mean different approaches to avoiding CO₂ emissions.
Please find the interactive graphics for each of the business units here.
CO₂UNTDOWN TO ZERO in clearly defined key areas
The foundation for the Green Factory is the ambitious CO₂UNTDOWN TO ZERO project in the division. We have defined a roadmap that guides our way to CO₂-neutral production in the entire division by 2035. The key areas are as follows:
Current examples
Holistic consideration and interaction of all measures across each of the key areas will lead to the best sustainable result and make our Green Factory a reality. Some things have already been achieved, but there is still much to be done. More than 270 projects are currently being implemented. Here are some examples:
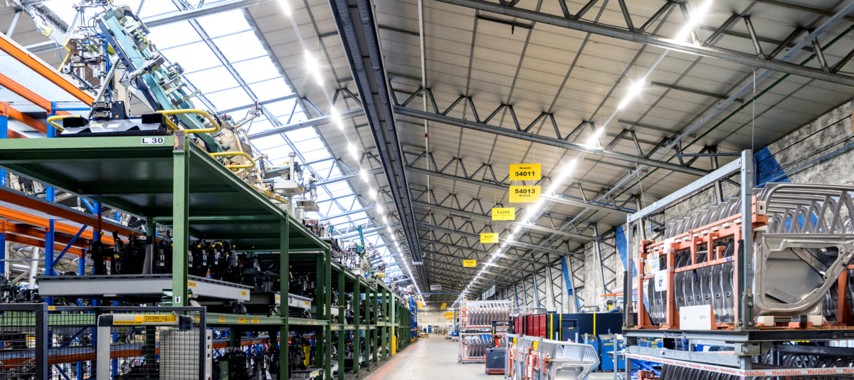
Saving energy
Process improvements and technology changes often have a double positive impact because CO₂ emissions are reduced and energy is saved. Here are some current examples: Metal Forming locations are switching to LED lighting. This reduces CO₂ emissions and saves up to 60 % of energy. Synchro motors replace hydraulic solutions, and solid-state lasers replace CO₂ lasers. Office areas are heated using waste heat from production, and much more.
Using renewable energy
When purchasing energy, we pay careful attention to how it is obtained. Long-term contracts are agreed with suppliers of green electricity. One example is a recent contract for nine wind turbines in the mountains of Upper Styria for the future supply of electricity exclusively to Metal Forming production sites in Styria and Lower Austria. Power supply is all about sustainability. The aim is to meet 80 to 100 % of the electrical demand from renewable sources by 2026.
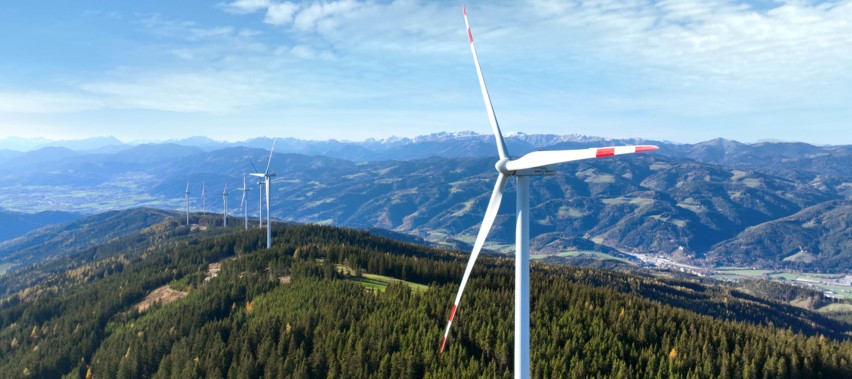
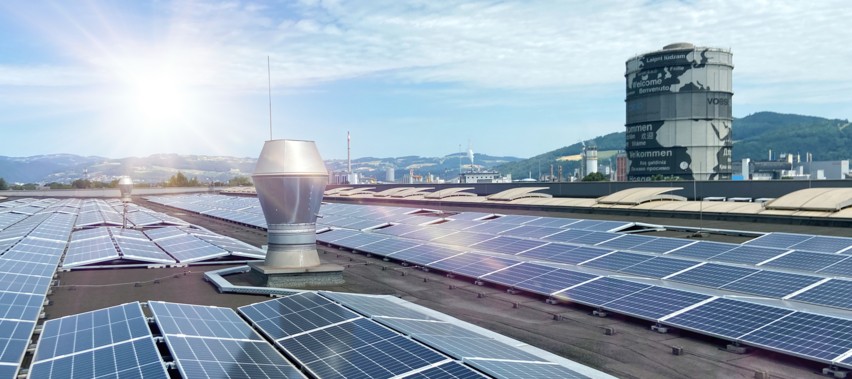
Producing green energy
We produce a lot of our own energy. Our large-scale projects focus on the installation of PV systems on production building rooftops and open spaces . For example, the second largest photovoltaic system in the Netherlands is installed on the plant in Bunschoten. We also use solar power in the southern hemisphere. At our site in East London, South Africa, the electricity generated by the PV system is stored in batteries. The plant is self-sufficient and will continue to produce even during governmental power shutdowns. In Austria, on the other hand, with three hydropower plants, Ybbs supplies more than a third of the electricity needed by Böhlerwerk and Kematen sites. These are only three examples of our many other projects. Our goal is to cover 20 % of the total electric requirement in the division with self-generated green energy.
Minimizing CO₂ footprint
The CO₂ footprint is minimized throughout the entire value chain, from raw materials to logistics. The production of green steel is a milestone in the pre-material sector. The ground-breaking ceremony for the first electric arc furnace has taken place this fall, and the new furnace will reduce CO₂ emissions by 30 % beginning in 2027. This conversion of steel production to a greener production route is the largest climate protection program in Austria. In the area of logistics, the shift from trucks to more environmentally friendly solutions is one of our highest priorities, and voestalpine products are primarily transported by ship or rail. Electrical equipment such as electric forklifts are also used on a large scale at the company.
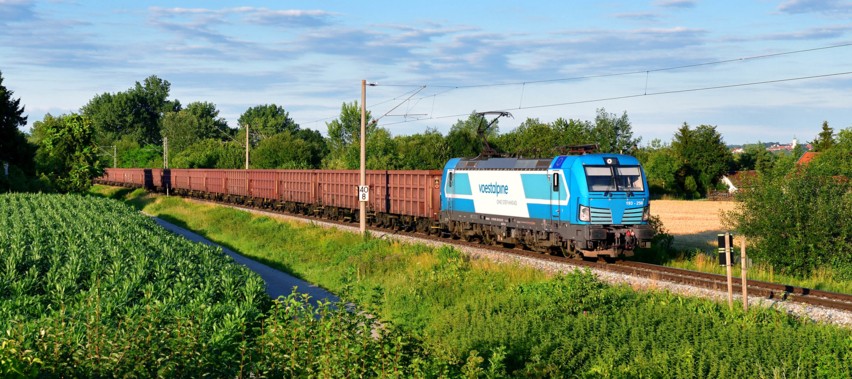
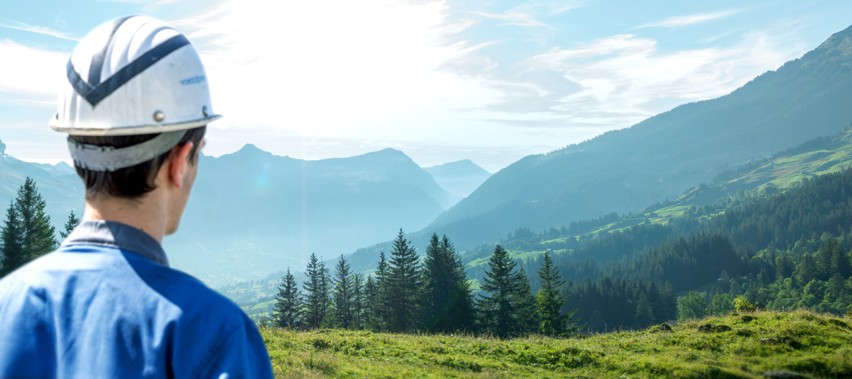
Increasing awareness
Only people can make a real difference. At each of our locations, managers are trained and employees motivated to be more conscious of our environment, at work as well as at home. Our focus is on raising awareness and strengthening ecological connections. We see a lot of enthusiasm, and we all want to make a difference, which is why we have provided a specially developed CO₂ emissions calculator to every employee and customer so that they can see their own CO₂ footprint.
Charging stations are available to employees as an incentive to drive electric cars to work. The share of electric cars in the company fleet is also being gradually increased. Employees can use their own muscle power on bikes provided for use on company premises. Special programs have been put into place. For example, employees are offered favorable conditions for the purchase of photovoltaic modules.
Please learn more about the mission of the voestalpine Metal Forming Division here.