Environmental Product Declarations offer evidence
The voestalpine Metal Forming Division has created the basis for many subsequent major steps on the path to climate neutral production. After one and a half years of hard work, the data for an Environmental Product Declaration (EPD) for the indirect phs process (phs-ultraform®) are now available.
Carbon footprint identified.
High-strength, press-hardened phs components are lightweight, supporting efforts to reduce vehicle weights and consequently emissions. The new EPDs provide the voestalpine Automotive Components sites with a certified sustainability label for their phs components. The EPDs primarily indicate the size of a product’s carbon footprint. This establishes another positive feature for voestalpine products.
First site determination.
The carbon footprint is calculated according to the energy consumed during the indirect phs processes at four voestalpine sites on three continents. Each step of the manufacturing process within the division is considered, from the coil to the oiled phs part. The EPD provides customers with a weighted mean value from the years 2018 to 2020 which—after confirmation from the program operator—is valid for five years.
Important basis created.
The process inventory for the phs components offer an additional advantage: documenting the data allows efforts to continuously improve the energy efficiency of ongoing process developments to be demonstrated. These enhancements have now been implemented, enabling around 20% of the energy used in the phs process chain to be saved. This not only brings the voestalpine companies closer to their target of climate neutrality, but also shows their customers that they are continuously working to improve the carbon footprint. Learn more about green projects and initiatives in the Metal Forming Division and its contribution to our CO2UNTDOWN TO ZERO.
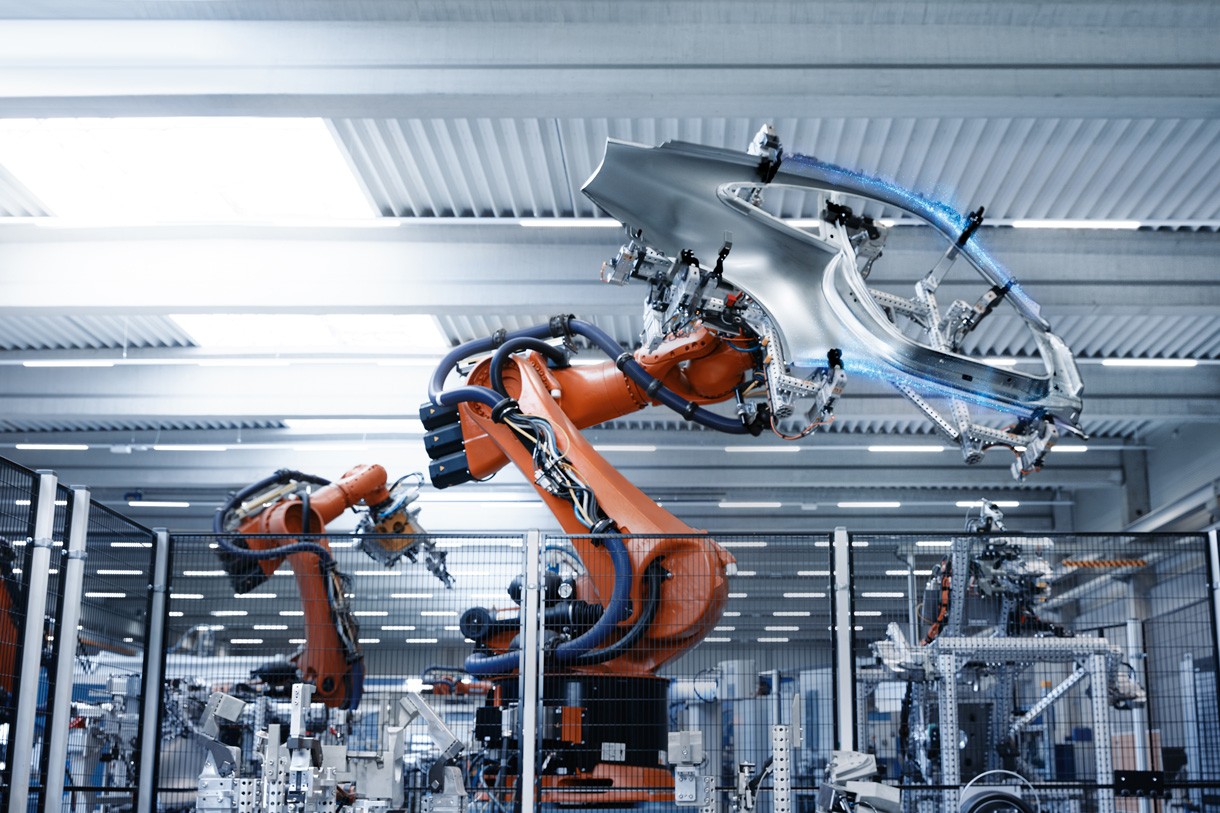
How are CO2 emissions calculated?
How much greenhouse gas is emitted per ton of product? A product or prematerial's EPD provides the answer to this and other questions. For example, it enables the end producer to calculate the complete footprint of their product, such as a car, or to identify the supplier with the lowest level of emissions. All the energy consumed in a product's manufacture—expressed as CO2 emissions—must be calculated in order to issue the EPD. The lower the amount of energy used in the production processes, and the more green electricity either generated by the manufacturer or as a share of the total purchased power, the smaller the ecological footprint. Scope 1 covers direct emissions from manufacture at the production site (e.g., combustion of natural gas when heating or subjecting the material to heat treatments), while Scope 2 covers the provision of the purchased, indirect, and already converted power source (primarily electricity). Scope 3 examines the emissions generated during the upstream and downstream processes, i.e., for companies in the Metal Forming Division, the production of steel. The EPDs provide an overview of the key emissions in Scope 1, 2, and 3, that is from mining the ore through to delivery of the finished component.
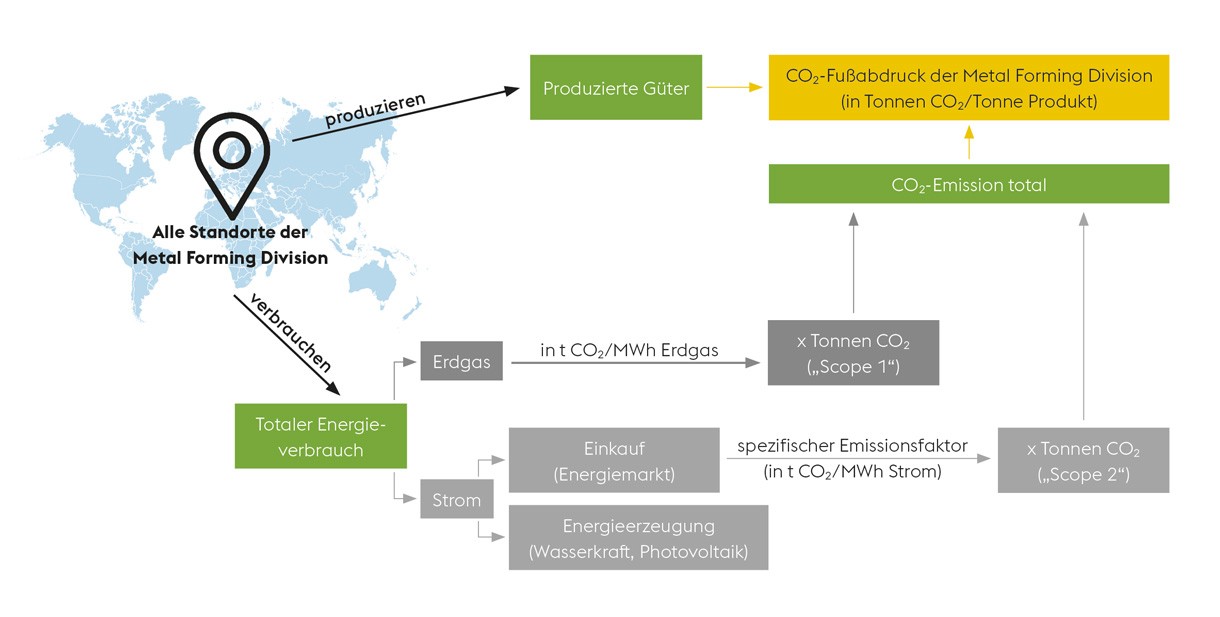