Best laser cutability. Narrowest tolerances. Excellent workability.
The steel grades of the alform laser series are thermomechanically rolled or normalized hot-rolled steels with excellent cold formability and are especially well suited to laser cutting. We supply minimum yield strengths of 180 to 420 MPa.
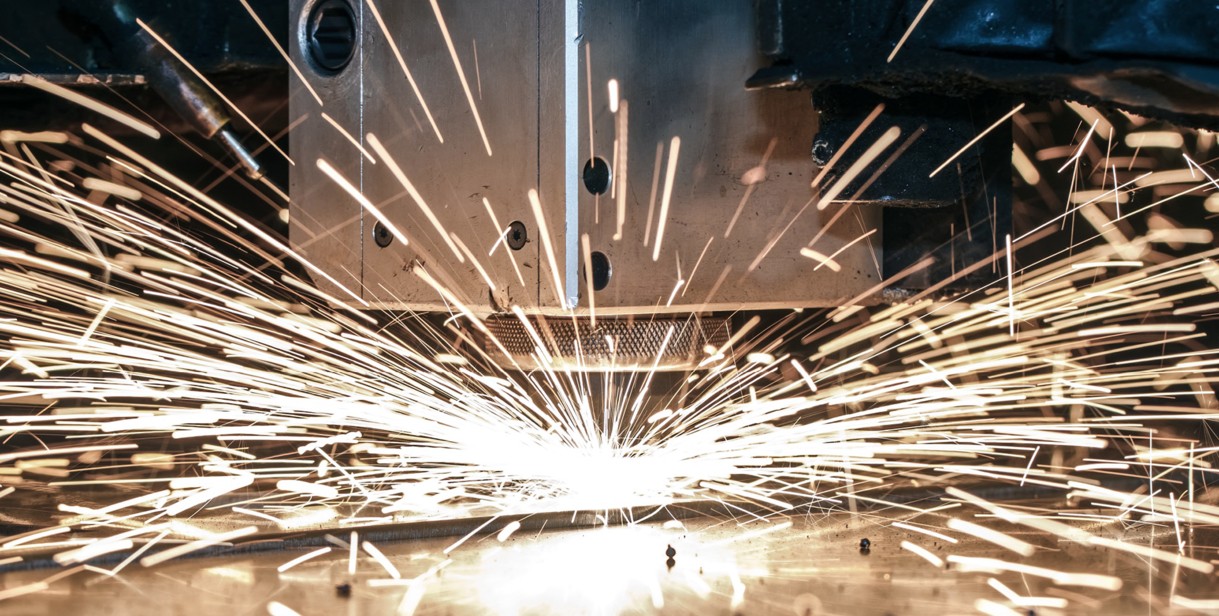
The alform laser series is characterized by the following:
- Extremely homogeneous surface and internal properties achieved through high degrees of purity with respect to non-metallic inclusions
Minimum inherent sheet stresses to avoid warping during cutting
Optimized laser cutting with regard to cutting speed and grade through limited phosphorus and sulfur content and a maximum silicon content of 0.03%,
Limited flatness tolerances for high-quality cutting
Optimized surface quality achieved by a thin, uniform layer of scale resulting from thermomechanical or normalized rolling
The use of alform® steels has proven successful in applications where extremely precise cuts, burr-free cut edges and parts free of distortion are required.
The advantages of the alform® laser series
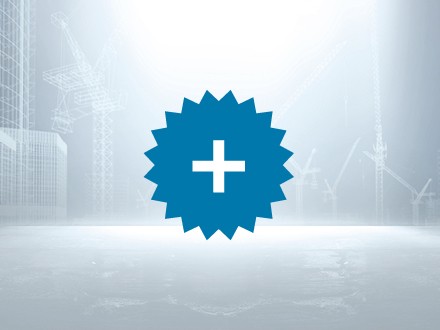
Best laser cutting quality ensured through implementation of the following:
- Special additional inspections of surface, dimensional tolerances and flatness
Highest cutting speeds with optimum shape of the cut edges as a result of the optimized chemical composition
High degrees of purity with respect to non-metallic inclusions (resulting in vertical cut edges without undercutting)
Homogeneous, uniform secondary scale layer ensuring trouble-free operation in laser cutting units as well as fine and shallow draglines.
Optimized production conditions from the hot-rolling mill and cut-to-length lines to the straightening lines and shearing units (guaranteed flatness deviations of ≤ 3 mm across a length of 1 meter)
Limited tolerances (50% of EN 10051, Tables 3 and 4)
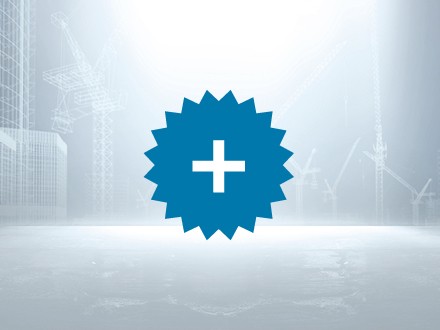
Excellent weldability is ensured by the following:
- Large field of welding parameters (processing range)
Cold cracking resistance without preheating
Best mechanical-technological properties in the welded joint equivalent to those in the base material
Excellent formability of the welded joint
Improved tempering resistance in case-hardening and heat-treatable steels
Low tendency toward age hardening
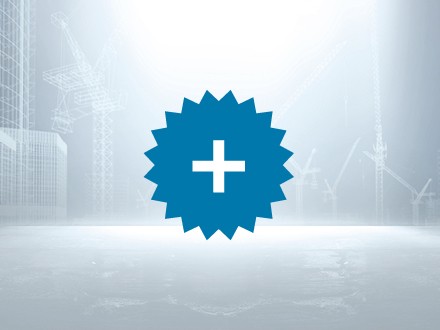
Uniform mechanical properties
- The high consistency of mechanical properties in alform® laster steels guarantees smooth automatic material processing.
Delivery specifications
alform® laser is available in both normalized and thermomechanically rolled condition. If it is necessary to heat-treat thermomechanically rolled steels (M series) above 580 °C (e.g., normalizing), this will result in a decrease of the minimum yield strength.
In such a case we would be able to supply normalized-rolled steels (N series), though only up to a minimum yield strength of 380 MPa. (Flame straightening is also possible in thermomechanically rolled steel grades up to 800 °C.)
Dimensions
Thickness [mm] | max. thickness [mm] for alform laser (min. width 900 mm) | ||||
180 N | 200 N 240 N | 380 N | 355 M 380 M | 420 M | |
1.80 - 1.89 | 1,185 | 1,360 | - | 1,050 | - |
1.90 - 1.99 | 1,260 | 1,440 | 1,100 | 1,115 | 1,000 |
2.00 - 2.24 | 1,320 | 1,500 | 1,120 | 1,165 | 1,040 |
2.25 - 2.49 | 1,505 | 1,600 | 1,175 | 1,340 | 1,150 |
2.50 - 2.74 | 1,600 | 1,600 | 1,235 | 1,600 | 1,315 |
2.75 - 2.99 | 1,600 | 1,600 | 1,290 | 1,600 | 1,540 |
3.00 - 3.24 | 1,600 | 1,600 | 1,350 | 1,600 | 1,600 |
3.25 - 3.49 | 1,600 | 1,600 | 1,410 | 1,600 | 1,600 |
3.50 - 3.74 | 1,600 | 1,600 | 1,475 | 1,600 | 1,600 |
3.75 - 4.50 | 1,600 | 1,600 | 1,535 | 1,600 | 1,600 |
4.51 - 12.00 | 1,600 | 1,600 | 1,600 | 1,600 | 1,600 |
(Cut-to-length sheets made of hot-rolled strip)
Tensile test
Tensile test | Yield strength Reh [%] min. | Yield strength Rp0,2 [%] min. | Tensile strength Rm [%] min. | Elongation [%] min. | |
[MPa] | [MPa] | [Mpa] | A80 | A5 | |
laser 180 N | 180 - 290 | - | 280 - 360 | 28 | 34 |
laser 200 N | 200 - 320 | - | 320 - 400 | 26 | 32 |
laser 240 N | 240 - 360 | - | 360 - 470 | 23 | 28 |
laser 380 N | 380 - 520 | - | 510 - 610 | 19 | 24 |
laser 355 M | 355 - 480 | - | 430 - 530 | 20 | 24 |
laser 380 M | 380 - 510 | - | 450 - 550 | 20 | 24 |
laser 420 M | 420 - 550 | - | 480 - 580 | 18 | 22 |
(Cut-to-length sheets made of hot-rolled strip)
Notch impact energy and edging radii
Notch impact energy Edging radii | Notch impact energy 1) ISO-V / 20 °C [J] min. | Edging radii 2) Ri min. at 90° edging Location of bending edge in direction of rolling (s = sheet thickness) | ||
s < 3 mm | s 3 - 6 mm | s > 6 mm | ||
alform laser 180 N | 3) | 0.25 s | 0.5 s | 1.0 s |
alform laser 200 N | 3) | 0.25 s | 0.5 s | 1.0 s |
alform laser 240 N | 27 | 0.25 s | 0.5 s | 1.0 s |
alform laser 380 N | 404) | 0.25 s | 0.5 s | 1.0 s |
alform laser 355 M | 40 | 0.25 s | 0.5 s | 0.8 s |
alfom laser 380 M | 40 | 0.25 s | 0.5 s | 0.8 s |
alform laser 420 M | 40 | 0.50 s | 1.0 s | 1.0 s |
(Cut-to-length sheets made of hot-rolled strip)
1) Av minimum mean value from three samples (ISO-V, longitudinal) as related to full-size specimen
(10 x 10 mm). Upon agreement, notch impact energy is determined for thickness of 6 mm and
higher. The value indicated is the mean value of three samples of 10 x 10 mm.
2) Smallest permissible inside radius at 90° edging, Ri min.
3) No guarantee.
4) A minimum value of 24 J is guaranteed for thickness higher than 8 mm.