3D sand printing in the fast lane: voestalpine Foundry Group helps Deutsche Bahn stay on track
Thanks to innovative 3D sand printing technology, it is possible to produce complex and customized castings with high precision in the shortest possible time. The pioneering FASTLANE service reduces the production time of castings to a minimum and, especially in the case of spare parts, helps to avoid unplanned downtimes and the resulting additional costs. Despite its speed, FASTLANE does not compromise on quality.
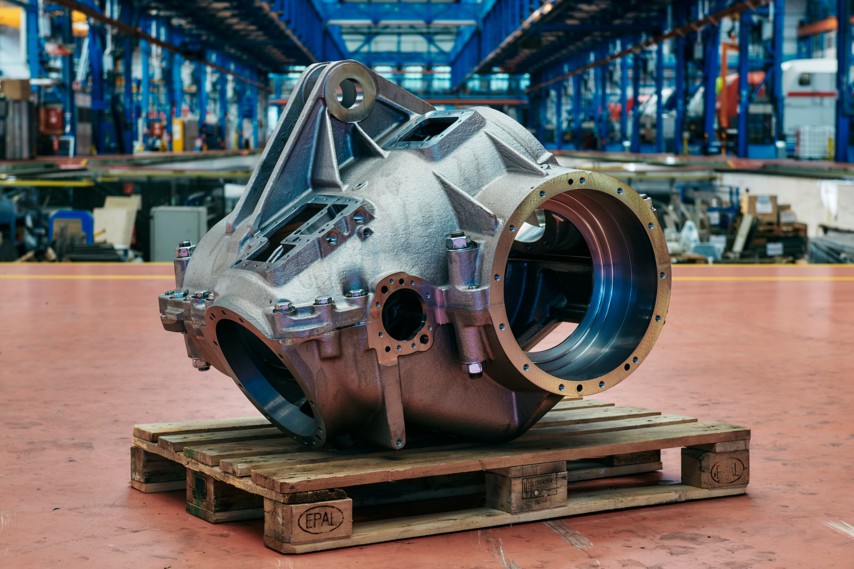
In a world where efficiency and speed are becoming increasingly important, the accelerated production and delivery of high-precision steel mold castings has also become a crucial factor in order placements. Conventional methods require complex and time-consuming preparations to build a mold before the actual casting can take place. However, thanks to the revolutionary FASTLANE service combined with 3D sand printing technology, this is now a thing of the past.
Recently, the benefits of this groundbreaking technology became clear once again, in collaboration with our new cooperation partner for 3D sand printing, Deutsche Bahn. A gearbox housing, an indispensable spare part with a volume of almost one cubic meter and weighing over half a ton, was urgently needed for repair work on idle shunting locomotives.
While the traditional production route for this spare part would have required an average delivery time of ten months, voestalpine Foundry Group was able to reduce the delivery time to just two months thanks to the use of 3D sand printing technology. The gearbox housing is produced using the indirect 3D printing process, in which powdered quartz sand is combined with a liquid binder to create the mold for subsequent casting.
Once the geometry and material are fixed, the casting is immediately added to a digital warehouse. CAD data of molds and cast parts are stored here, allowing for quick and uncomplicated preparation of the component for casting through 3D sand printing with just a few mouse clicks when needed. Digitalization saves storage space and costs, shortens delivery times and supply chains, providing significant advantages for our customers. The entire process is automated and enables rapid implementation of design changes or adaptations.
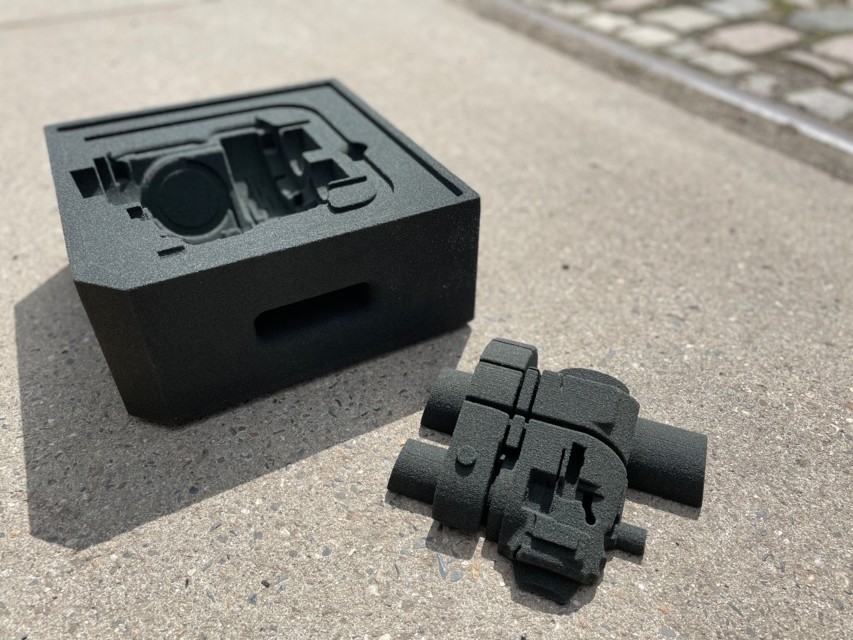
3D sand printing at FASTLANE also delivers added value when it comes to sustainability. CO2 emissions are avoided through shorter distances and reduced physical inventories. In addition, 3D sand printing already saves resources in itself, as only the raw material actually required is used due to contour-accurate casting.
The voestalpine Foundry Group is proud to contribute to the success of our customers in the best possible way and to support Deutsche Bahn in accelerating maintenance work. Through the use of 3D sand printing technology, we are setting new standards in the manufacturing industry and helping to make the industry more efficient and reliable. With our commitment to quality and innovation, we stand by our customers as a reliable partner to meet their casting and supply requirements and drive progress in the industry.
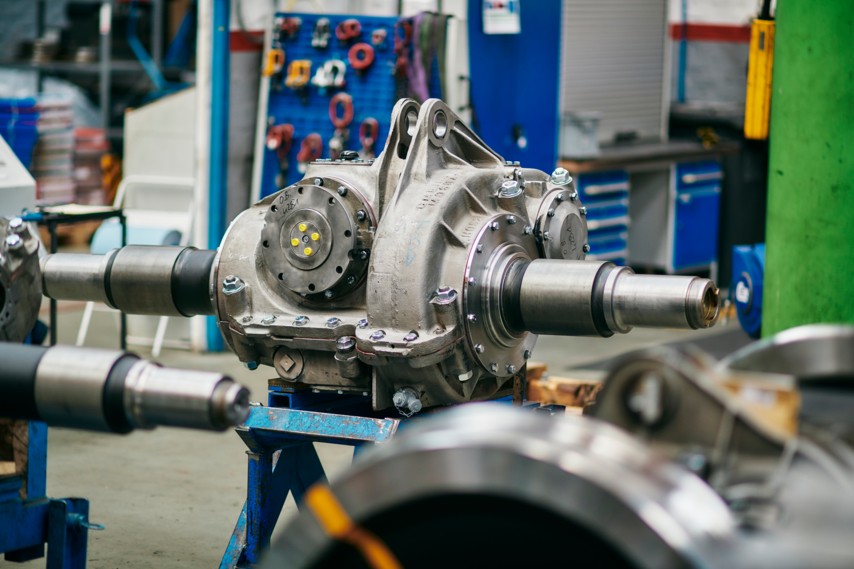
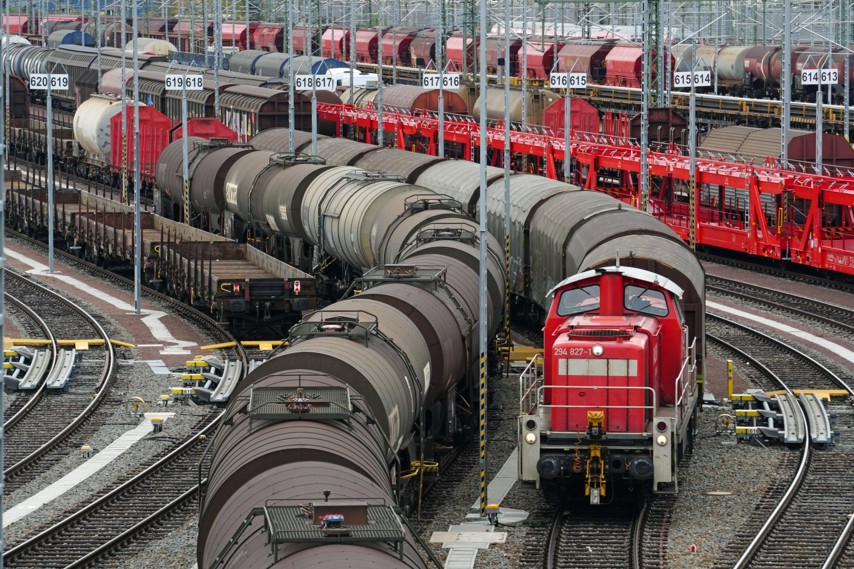
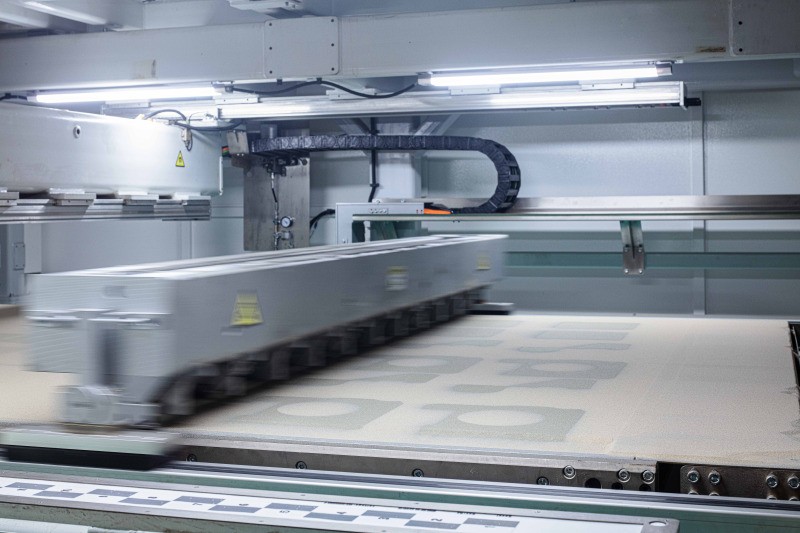
For more information about 3D sand printing, please click here.