Blachy trudnościeralne wykonane z taśmy goracowalcowanej.
Dzięki wysokiej twardości 250 - 500 HB martenzytyczne stale durostat® z voestalpine mogą być stosowane wszędzie tam, gdzie wymagana jest wysoka odporność na ścieranie. Wyraża się to albo jako zużycie ścierne ślizgowe, albo zużycie ścierne udarowe - lub jako kombinacja obu.
W celu porównania zachowania się materiałów stalowych pod względem zużycia stosuje się różne testy laboratoryjne, które dobrze pokazują różne mechanizmy zużycia. Przy skalowaniu do rzeczywistego systemu tribologicznego należy jednak zwrócić uwagę na to, jak dobrze badania laboratoryjne odzwierciedlają warunki panujące w praktyce.
Dzięki zastosowaniu stali durostat® można znacznie wydłużyć żywotność i związane z nią okresy między obsługowe takich elementów jak łopaty koparek, powierzchnie wywrotek, zsuwnie przenośników, powierzchnie ścieralne w wagonach towarowych i masowych, kontenerach czy betoniarkach.
Przekonujące zalety:
- Wysoka odporność na zużycie - mniejsze ścieranie
- Wydłużona żywotność i okresy międzyobsługowe
- Lekkie zastosowanie dzięki wysokiej wytrzymałości
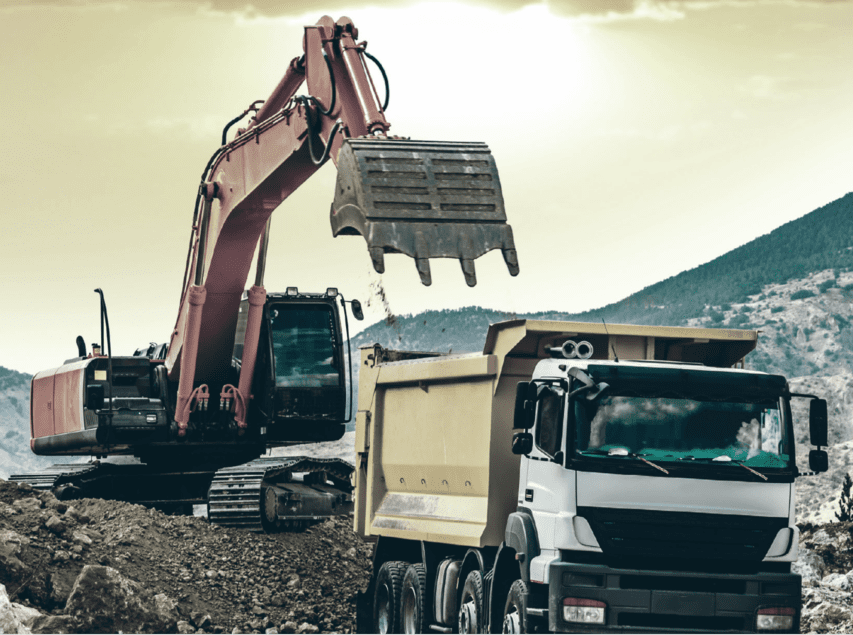
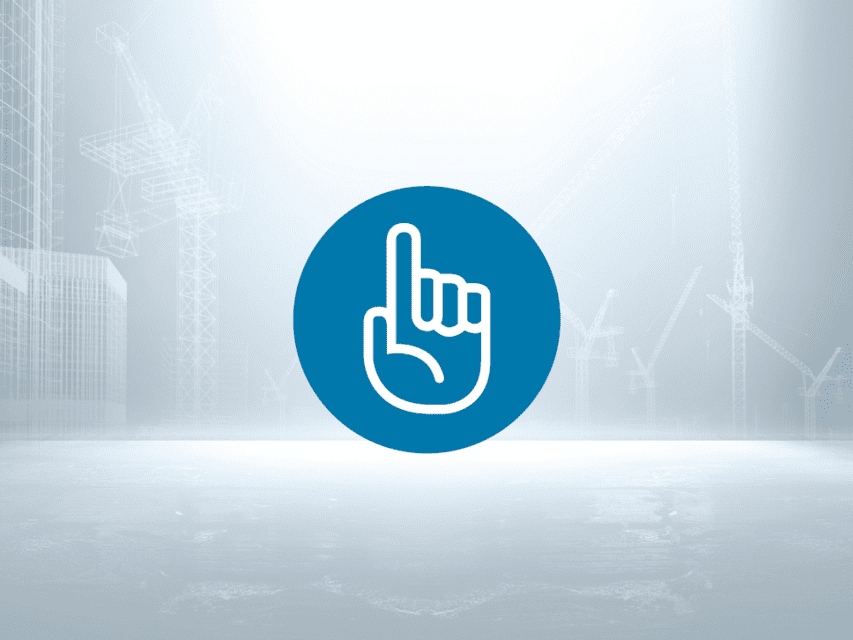
Przedstawione wyniki zostały przeprowadzone w niezależnych instytutach badawczych TU Clausthal (D) i Tampere Wear Center (FI).
Zużycie ślizgowe
W celu zbadania zużycia ślizgowego stali durostat® przeprowadzono próby tarcia na kole ciernym zgodnie z normą ASTM G65, w których suchy lub wilgotny piasek kwarcowy jest wprowadzany jako materiał ścierny pomiędzy gumowe koło a próbkę. Test opisuje więc klasyczne zużycie 2 ciał, które występuje przy zsuwaniu się skał z powierzchni wywrotek, zsuwni przenośników lub łopat koparek.
Instytut doświadczalny ISAF, TU Clausthal (Niemcy)
Badanie koła ciernego ASTM 65 z suchym piaskiem
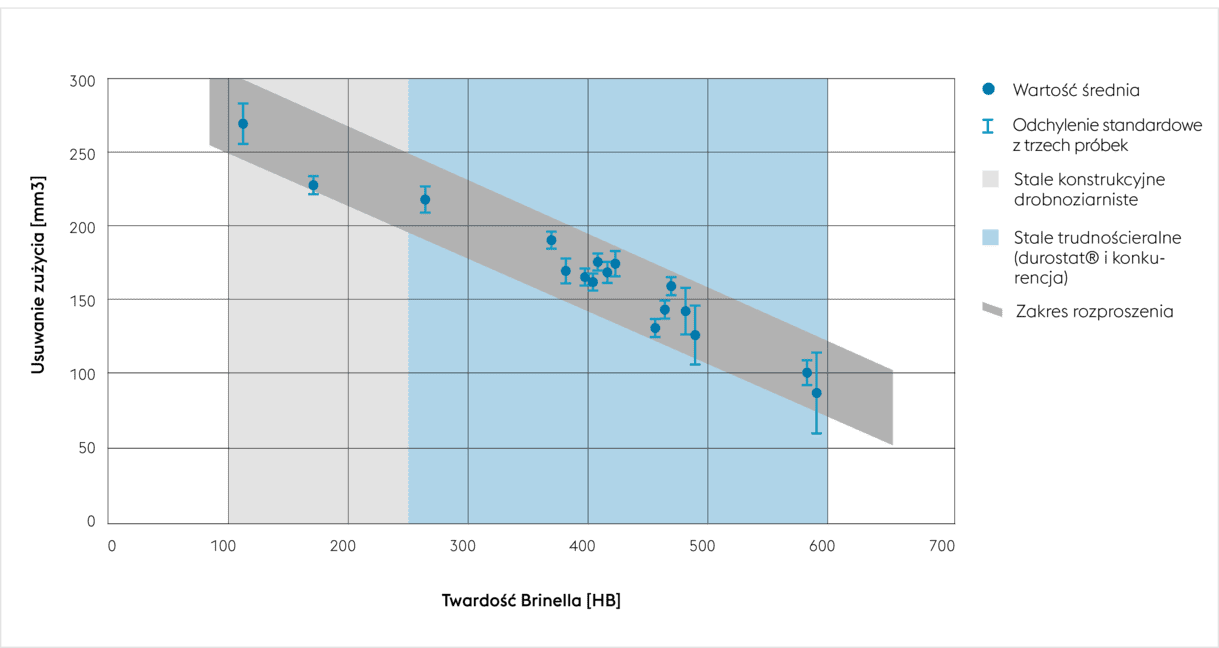
Badanie koła ciernego ASTM 65 z mokrym piaskiem
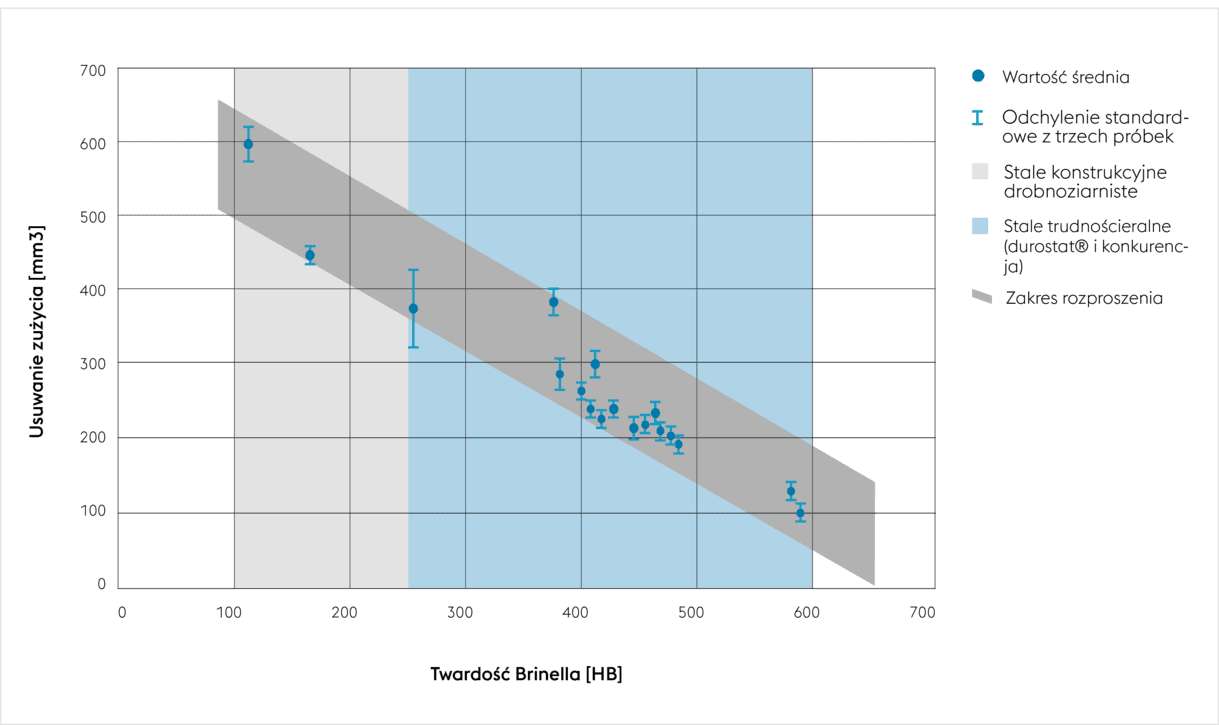
Znacznie zmniejszone zużycie ślizgowe
Wyniki pokazują, że głównym czynnikiem wpływającym na zachowanie się zużycia ślizgowego jest twardość. W związku z tym stale martenzytyczne, takie jak durostat® firmy voestalpine, wykazują znacznie większą odporność na zużycie ślizgowe niż klasyczne stale konstrukcyjne lub stale mikrostopowe.
Zużycie udarowe
W celu scharakteryzowania zużycia udarowego przeprowadzono testy wirnika (Instytut: Uniwersytet w Tampere, Tampere Wear Center). Zewnętrzne koło łopatkowe (tumbler) transportuje materiał (tu: granit Kuru o wielkości ziaren od 10 do 12,5 mm) do góry z wolną prędkością (30 obr/min); badany materiał znajduje się na szybko obracającym się wirniku (wirnik o prędkości 700 obr/min), który poprzez energię uderzenia kruszy granit.
Skutkuje to z jednej strony powstawaniem na próbkach bruzd i zagłębień, a z drugiej strony usuwaniem tych silnie zdeformowanych obszarów przez uderzające w nie następnie cząstki ścierne. Przykład praktyczny: Prace ziemne (kultywator rolniczy, brona talerzowa, procesy załadunkowe w wywrotkach lub wagonach towarowych i masowych).
Wyniki bębnów wirnikowych w stosunku do odniesienia [%]
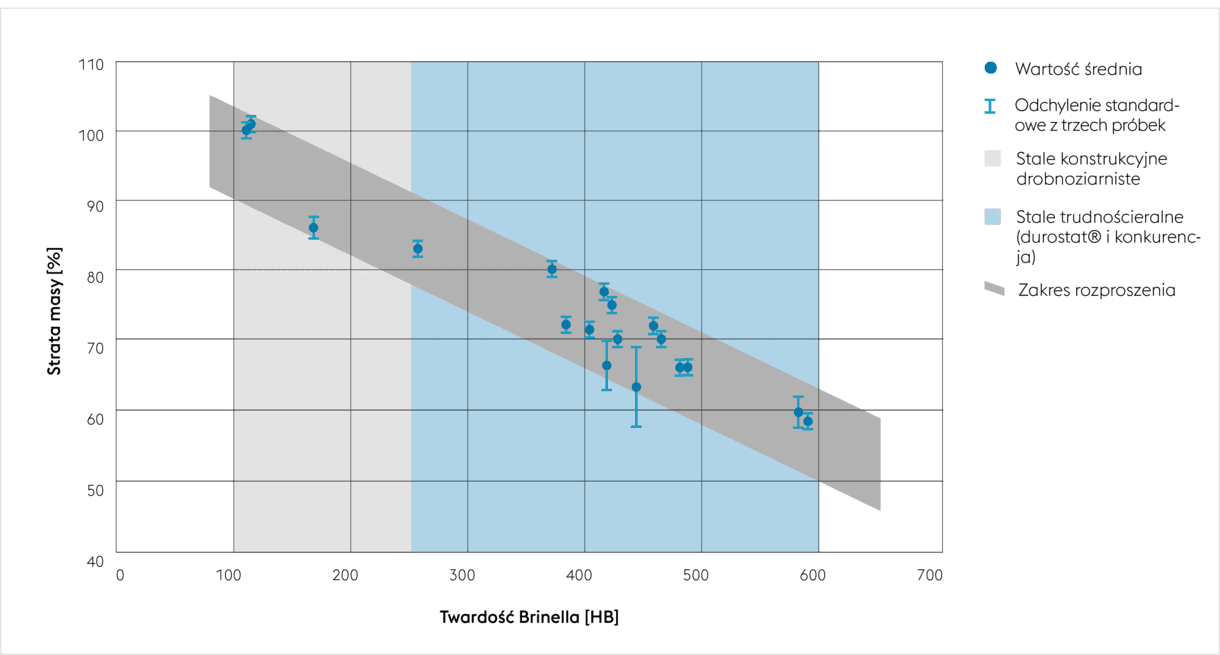
Znacznie zmniejszone zużycie udarowe Podobnie jak w przypadku zużycia ślizgowego, bardzo dobre właściwości martenzytycznej stali durostat® są również widoczne w przypadku zużycia udarowego.
Próba udarności
W celu sprawdzenia ekstremalnych obciążeń materiału przy załadunku nadwozi wywrotek dużymi bryłami skalnymi, złomem lub podobnymi, przeprowadzono testy w symulatorze zderzeń. W tym teście sanki z końcówką uderzającą w kształcie stożka są wystrzeliwane w próbkę z określoną energią. Pozostała głębokość wgniecenia jest mierzona na płytce testowej.
Badano różne materiały o następujących grubościach materiału:
- S355MC: 10 mm
- durostat 250: 7 mm
- durostat 400: 5 mm
- durostat 450: 4 mm
Wyniki
Wraz ze wzrostem twardości materiałów maleje niezbędna grubość materiału dla tej samej głębokości wgniecenia (czerwona linia na wykresie). Stwarza to możliwości dla lekkich aplikacji. Wraz ze wzrostem twardości materiałów zmniejsza się głębokość wgniecenia przy tej samej grubości materiału (krzywe na wykresie). Oznacza to, że można zrealizować jeszcze bardziej odporne komponenty i grupy komponentów.
durostat® jako najlepszy materiał w teście udarnościowym
Przykład
Przy głębokości wgłębienia 10 mm, dla S355MC potrzeba by było 10 mm grubości materiału, podczas gdy dla durostatu 450 jest to tylko 4 mm. Oznacza to, że można produkować lżejsze komponenty/grupy komponentów przy zachowaniu tej samej odporności na odkształcenia, co umożliwia wytwarzanie zrównoważonych (zmniejszenie zużycia materiałów i paliwa, redukcja CO2) i ekonomicznych (zwiększenie ładowności) produktów końcowych.
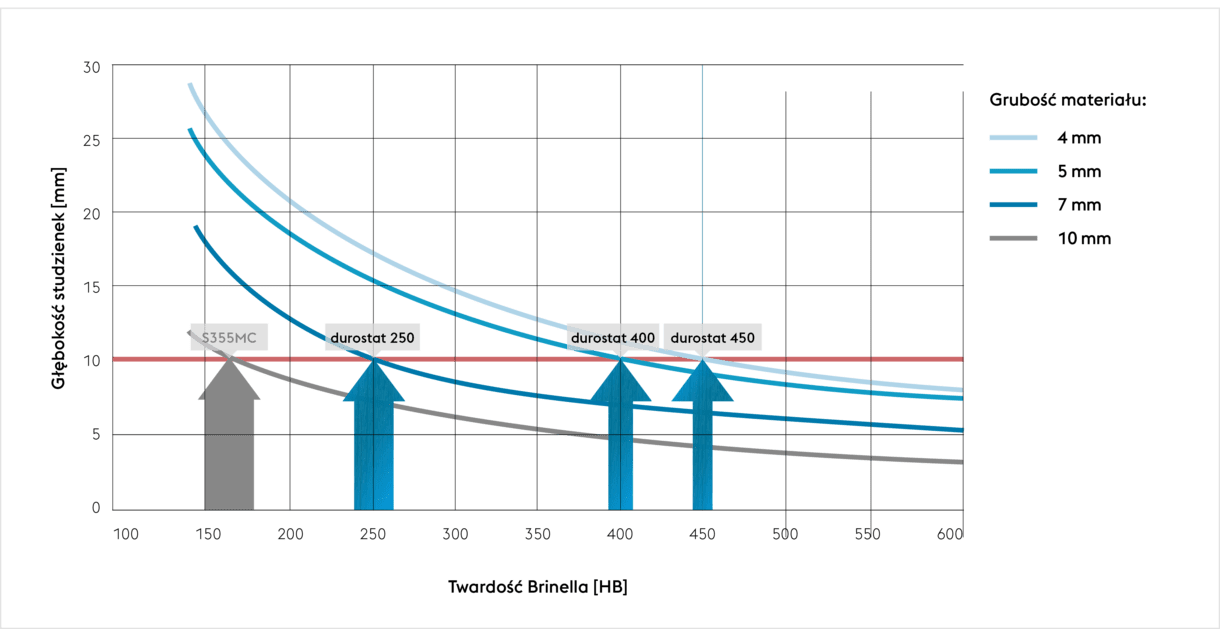
Dobra spawalność dzięki niskiej zawartości węgla
Ze względu na swój skład chemiczny, blachy z durostatu® mogą być dobrze spawane wszystkimi powszechnie stosowanymi procesami spawania termicznego. Strefa wpływu ciepła w spoinach charakteryzuje się z jednej strony występowaniem zmiękczenia początkowego, a z drugiej strony brakiem utwardzenia w stosunku do materiału podstawowego utwardzonego podczas produkcji.
Typowe wartości | |||||
Materiał | Zawartość C [%] | CET 1) [%] | CEV 2) [%] | PCM 3) [%] | Klasyfikacja grupowa zgodnie z ISO/TR 15608 |
durostat 400 | 0,11 | 0,35 | 0,54 | 0,26 | 3,2 4) |
durostat 450 | 0,15 | 0,39 | 0,58 | 0,30 | 3,2 4) |
durostat 500 | 0,19 | 0,43 | 0,61 | 0,34 | 3,2 4) |
1) CEV=C+Mn/6+(Cr+Mo+V)/5+(Ni+Cu)/15
2) CET=C+(Mn+Mo)/10+(Cr+Cu)/20+Ni/40
3) PCM=C+Si/30+(Mn+Cu+Cr)/20+Ni/60+Mo/15+V/10+B∙5
4) Stan dostawy utwardzony
Instrukcja obróbki spawalniczej
Zmiękczanie rozrusznika Szerokość zmiękczenia startowego jest bezpośrednio zależna od czasu chłodzenia (czas t8/5). Wpływ zmiękczenia przystawki na właściwości wytrzymałościowe poprzeczne do złącza spawanego zależy od względnej szerokości strefy miękkiej (stosunek szerokości strefy miękkiej do grubości blachy), a także od właściwości wytrzymałościowych spoiny.
Hartowanie - nie istnieje
Ze względu na koncepcję materiału czysto martenzytycznego, maksymalna twardość w strefie wpływu ciepła nie może przekroczyć twardości materiału podstawowego. Jest ona zależna wyłącznie od zawartości węgla. Ekwiwalent węgla ma więc wpływ jedynie na zachowanie się przemiany i spadek maksymalnej twardości ze wzrostem czasu t8/5. Wartości twardości w złączu spawanym określa się za pomocą metody Vickersa (HV). Za pomocą tabeli przeliczeniowej wg EN ISO 18265, tabela A.1, można oszacować wartości twardości w skali Brinella (HB) lub wytrzymałości na rozciąganie (Rm).
Podgrzewanie wstępne - nie jest konieczne W zasadzie do grubości blachy 6 mm nie jest konieczne podgrzewanie wstępne.
Dotyczy to następujących warunków:
- Stosowanie spoiw i materiałów spawalniczych, które powodują bardzo niską zawartość wodoru w spoinie (HD < 5 ml/100 g spoiny). Należy przestrzegać wskazówek producenta dotyczących przechowywania i ponownego suszenia.
- Blachy powinny być czyste, suche i wolne od powłok, rdzy i kamienia w obszarze spoin.
W przypadkach odbiegających od normy zaleca się oszacowanie temperatury podgrzewania według EN 1011-2, C.3 - metoda B lub SEW 088. W zależności od warunków klimatycznych (spadek poniżej punktu rosy lub wilgotności kondensacyjnej), bezpośrednio przed spawaniem zaleca się osuszenie krawędzi spawalniczych w temperaturze min. 80 °C.
Punkt rosy i temperaturę podgrzewania można również oszacować za pomocą kalkulatora spawalniczego voestalpine.
Ręczne spawanie łukowe (111) i spawanie łukowe w osłonie gazów (MAG, 135) Na właściwości wytrzymałościowe poprzeczne do złącza spawanego wpływa między innymi poziom wytrzymałości wybranego spoiwa.
Materiały wypełniające
Stopień wytrzymałości / twardość wypełniacza lub czystego metalu czysta spoina metalowa Przeliczenie zgodnie z DIN EN ISO 18265 Tabela A.1 | Materiał wypełniający | ||||||
Materiał | HB ~ 0,30 x Rm | HB ←→ HV, HRC | Ręczne spawanie łukowe elektrodą (111) | Drut pełny MAG (135) | Drut wypełniający MAG (136, 138) | ||
durostat 400 durostat 450 durostat 500 | Rm ≥ 500 MPa | HB ≥ 148 | HV ≥ 156 | - | np. B. BÖHLER FOX EV 50, ... AWS A5.1: E7018-1H4R EN ISO 2560-A: E 42 5 B 4 2 H5 | np. B. BÖHLER EMK 6, UNION K 52, ... AWS A5.18: ER70S-6 EN ISO 14341-A: G 42 4 M21 3Si1 | |
Rm ≥ 530 MPa | HB ≥ 156 | HV ≥ 164 | - | np. B. BÖHLER FOX EV 60, ... AWS A5.5: E8018-C3 H4R EN ISO 2560-A: E 46 6 1Ni B 4 2 H5 | np. B. BÖHLER EMK 8, UNION K 56, ... AWS A5.18: ER70S-6 EN ISO 14341-A: G 46 4 M21 4Si1 | np. B. diamondspark 52 MC, BC, RC, ... AWS A5.36: E71T15, E70T5, E71T1 EN ISO 17632-A: T 46 4 M, T 46 4 B, T 46 4 P | |
Rm ≥ 690 MPa | HB ≥ 204 | HV ≥ 215 | - | np. B. BÖHLER FOX EV 75, ... AWS A5.5: E10018-G H4R EN ISO 18275-A: E 62 6 Mn2NiCrMo B 4 2 H5 | np. B. UNION NiMoCr, ... AWS A5.28: ER100S-G EN ISO 16834-A: G 69 6 M21 Mn4Ni1,5CrMo | np. B. diamondspark 620 MC, RC, ... AWS A5.36: E101T15, E101T1 EN ISO 18276-A: T 62 4 Z M, T 62 4 Mn1,5Ni P | |
Rm ≥ 760 MPa | HB ≥ 224 | HV ≥ 236 | HRC ≥ 20 | np. B. BÖHLER FOX EV 85, ... AWS A5.5: E11018-G H4R EN ISO 18275-A: E 69 6 Mn2NiCrMo B 4 2 H5 | np. B. BÖHLER NiCrMo 2,5- IG, UNION X85, ... AWS A5.28: ER110S-G EN ISO 16834-A: G 69 6 M21 Mn3Ni2.5CrMo G 79 5 M21 Mn4Ni1,5CrMo | np. B. diamondspark 700 MC, BC, RC, … AWS A5.36: E111T15, E110T5, E111T1 EN ISO 18276-A: T 69 6 Mn2NiCrMo M, T 69 6 1Mn2NiCrMo B, T 69 6 Z P | |
Rm ≥ 940 MPa | HB ≥ 277 | HV ≥ 291 | HRC ≥ 29 | np. B. BÖHLER X90-IG, Union X90, … AWS A5.28: ER120S-G EN ISO 16834-A: G 89 6 M21 Mn4Ni2CrMo | np. B. diamondspark 900 MC, BC, … AWS A5.36: 131T15, E130T5 EN ISO 18276-A: T 89 5 ZMn2NiCrMo M, T 89 4 Mn2Ni1CrMo B | ||
Rm ≥ 980 MPa | HB ≥ 289 | HV ≥ 304 | HRC ≥ 30 | np. B. UNION X96, … AWS A5.28: ER120S-G EN ISO 16834-A: G 89 5 M Mn4Ni2,5CrMo | np. B. diamondspark 960 MC, … EN ISO 18276-A: T 89 4 ZMn2NiCrMo M | ||
Odporne na zużycie materiały wypełniające
Jeżeli ze względów konstrukcyjnych konieczne jest, aby spoiny miały taką samą odporność na ścieranie jak materiał podstawowy, warstwa wierzchnia może być wykonana z odpornych na ścieranie materiałów wypełniających.
Poziom wytrzymałości / twardość spoiwa lub czystego metalu spoiny Konwersja wg DIN EN ISO 18265 Tabela A.1 | Materiał wypełniający | |||||||
Materiał | HB ~ 0,30 x Rm | HB ←→ HV, HRC | Ręczne spawanie łukowe elektrodą (111) | Drut rdzeniowy bez gazu obojętnego (114) | Drut pełny MAG (135) | Proszek metalowy Drut wypełniający MAG (138) | ||
durostat 400 HB 360 - 440 | HB ≥ 250 | Rm ≥ 847 MPa | HV ≥ 263 | HRC ≥ 24 | np. B. UTP DUR 250, ... EN 14700: E Fe 1 DIN 8555: E 1-UM-250 | np. B. SK BU-O, ... EN 14700: T Fe 13 mod. DIN 8555: MF 1-GF-300 P | np. B. UTP A DUR 250, ... EN 14700: SZ Fe 1 DIN 8555: MSG 1-GZ-250 | np. B. UTP AF ROBOTIC 250, ... EN 14700: T Fe 1 DIN 8555: MSG 1-GF-250-P |
durostat 450 HB 410 - 490 | HB ≥ 350 | Rm ≥ 1186 MPa | HV ≥ 368 | HRC ≥ 37 | np. B. UTP DUR 350, ... EN 14700: E Fe 1 DIN 8555: E 1-UM-350 | np. B. SK 242-O, ... EN 14700: T Fe 1 DIN 8555: MF 1-GF-40-P | np. B. UTP A DUR 350, ... EN 14700: SZ Fe 2 DIN 8555: MSG 2-GZ-400 | np. B. UTP AF ROBOTIC 352, ... EN 14700: T Fe 1 DIN 8555: MSG 1-GF-350-P |
durostat 500 HB 460 - 540 | HB ≥ 532 | Rm ≥ 1845 MPa | HV ≥ 580 | HRC ≥ 53 | np. B. UTP DUR 600, ... EN 14700: E Fe 8 DIN 8555: E 6-UM-60 | np. B. SK 258-O, ... EN 14700: T Fe 1 DIN 8555: MF 6-GF-55-GT | np. B. UTP A DUR 600, ... EN 14700: S Fe 8 DIN 8555: MSG 6-GZ-60-S | np. B. UTP AF ROBOTIC 600, ... EN 14700: T Fe 1 DIN 8555: MSG 6-GF-60-GP |
Spawanie wiązką laserową (521, 522, 523) i spawanie hybrydowe wiązką laserową-łukiem
Dzięki bardziej skoncentrowanemu dopływowi energii i związanemu z tym szybszemu chłodzeniu, w porównaniu do ręcznego spawania łukowego i spawania łukowego w osłonie gazów, występuje mniejsze zmiękczenie startowe w strefie wpływu ciepła i wyższy poziom wytrzymałości metalu spoiny.
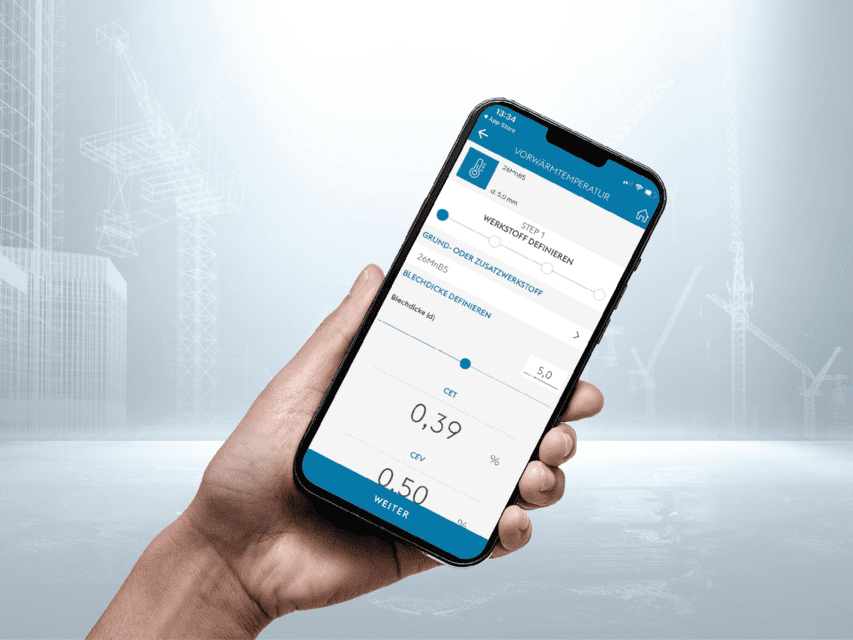
Welding Calculator voestalpine
Welding Calculator voestalpine wspiera Państwa w planowaniu i optymalizacji zadań spawalniczych, takich jak obliczanie czasu chłodzenia i temperatury podgrzewania wstępnego oraz obliczanie wymaganych ilości materiałów spawalniczych. Pobierz teraz kalkulator spawalniczy voestalpine jako aplikację na swoim smartfonie lub skorzystaj z wersji online na swoim komputerze stacjonarnym!