Introduced in France in 1930 by Mr. Paul BAP, founder of Profilafroid, the steel profiles made from steel coils, also called strips in rolls, were already developed in other countries.Especially in the United States, England and Germany.nitially realized on a cold drawing bench, the process has been completely transformed by the use of machines with roller trains, called profileuse, allowing a continuous production and much faster than that of the drawing bench.
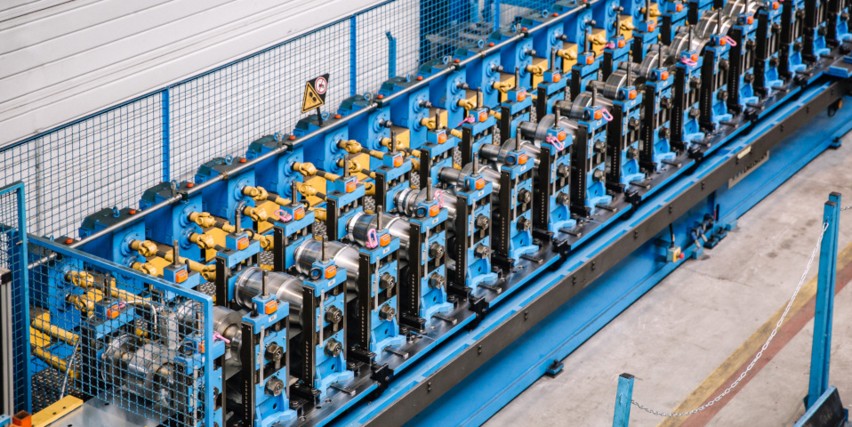
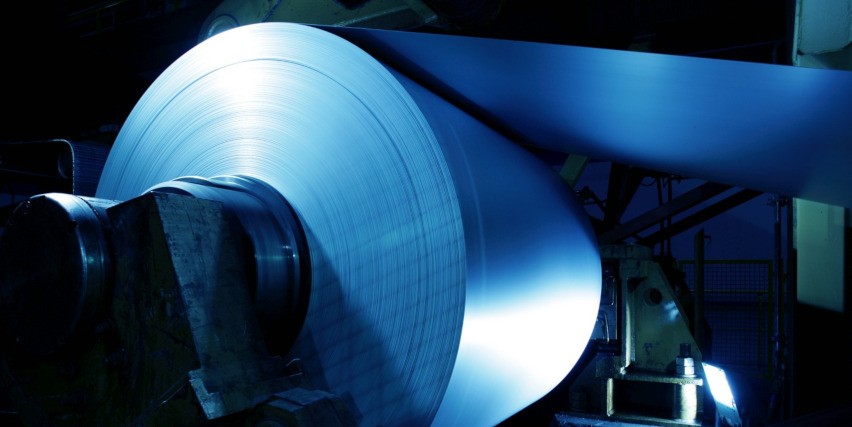
Cold roll forming consists of gradually and continuously forming a steel profile.The method consists initially unrolling the strip of a steel coil, whose width corresponds to the developed of the finished profile.This band, also called strip, is then engaged flat in a succession of several rolls called rollers whose shapes and numbers are variable depending on the complexity of the desired steel profile.
This succession of rollers is decomposed into a number of operations.Each operation corresponds to a profiling head.
Each head is similar to a small rolling mill cage with two shafts, one upper and the other lower, supporting the rollers with conjugate profiles, machined to match the forming they must perform and between which passes the metal strip.These rollers are made of high strength steel and manufactured by us.

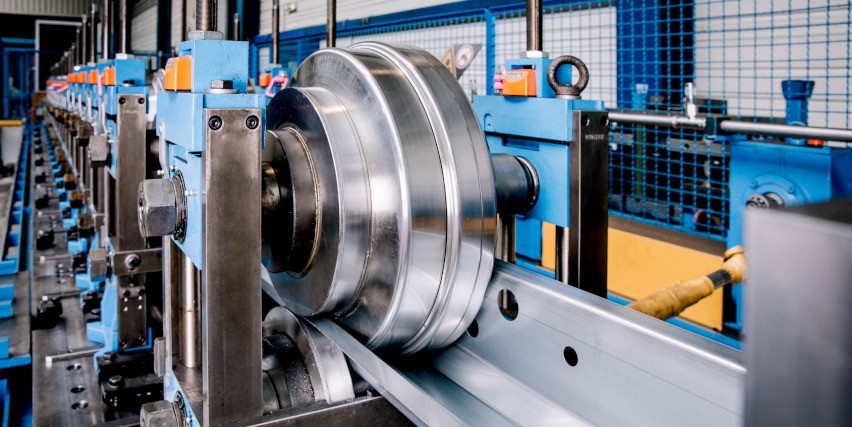
All of these rollers, called roller train, are defined by our design office which determines the "flower pattern".This is the number of operations required to manufacture a steel profile.A head represents a partial deformation operation of the flat steel strip.The band goes in one head, then in another and so on successively to the desired end result.
This successive passage of the band in the profiling heads progressively transforms the metal strip towards its final shape.This process respects the mechanical and characteristic stresses of the metal and allows the use of multiple grades of steels from S235 to multiphase steels.Indeed, the two shafts of each head are controlled by the motor of the machine, which ensures a regular drive of the band.
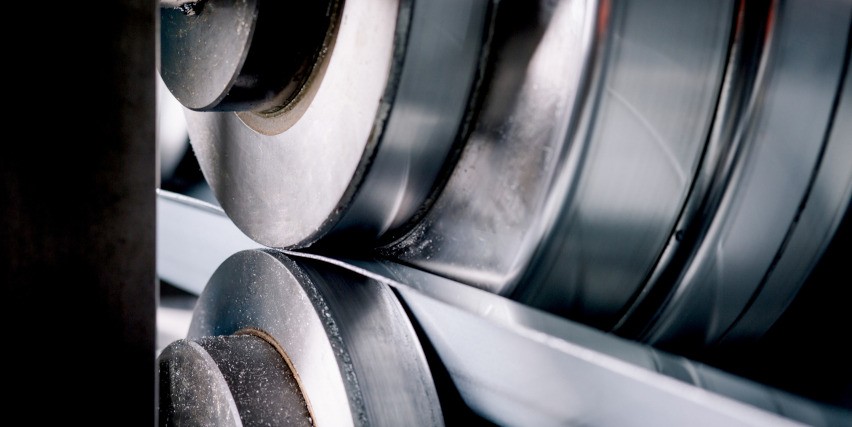
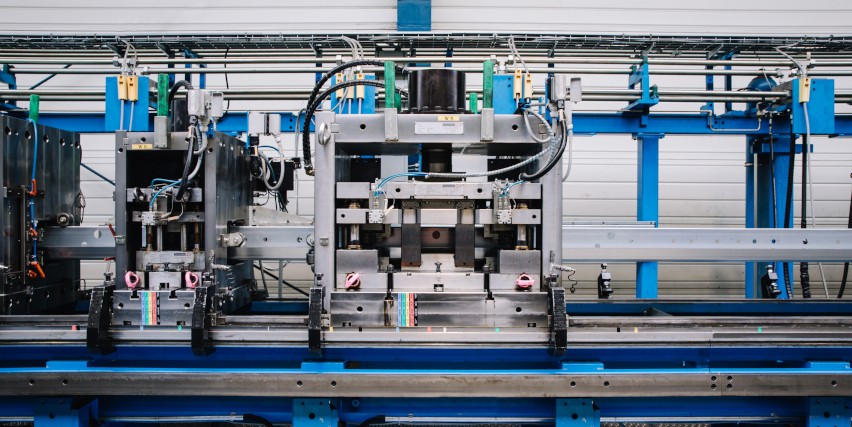
The forming of the profile being performed very gradually, we do not have to fear the cracks or even the breaks that occur in the cold bending to the press or stamping.Finally, although it is not a rolling, the operation produces a certain surface hardening known as the "skin effect".The manufacturing, initially limited to hot and cold rolled steel strip sections, has gradually expanded to include stainless steel and aluminum and copper alloy profiles.
During the cold roll forming, operations such as punching, stamping, can be done online.Then, the metal section is cut at the end of the line to the desired length.The profiling operations are performed cold, because carried out at room temperature, they do not require the heating or melting of the metal for the manufacture of a profile.
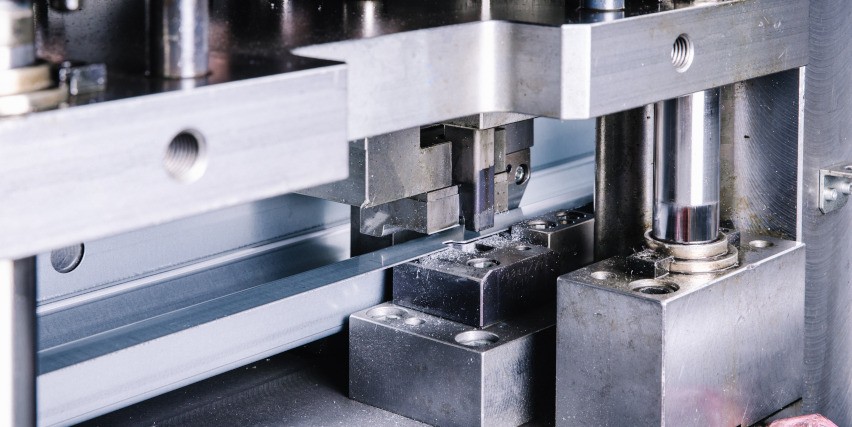

The cold roll forming operation does not bring about any substantial modification to the flat product used concerning its thickness and its mechanical characteristics.
The cold forming industry is part of the primary metal processing industry between the steel industry and users.
The cold roll forming advantages are numerous
- Development, diversity and complexity of forms that meet all the needs of users.
- Curvature radius corresponding to the thickness of the metal strip.
- Lightening the weight of structures by roll forming steels with high elastic limits.
- Ease of implementation in assemblies with welding, riveting, bolting, gluing.
- Variety of possible delivery lengths of steel profiles, up to 30 meters.
- Diversity of surface conditions such as hot roll, pickled, cold rolled, prepainted, and galvanized.