See for yourself what durostat® can do!
durostat® can be used in a wide variety of applications. We offer our customers the highest quality standards, yet we continually define the limits of feasibility and never lose sight of our partners' best performance. durostat® is a wear-resisting steel with excellent properties that have set new standards Set wear resistance and hardness.

Longer service life
We developed the durostat® product range in order to prolong the service life of your components in abrasive environments. Our steel grades have a significantly longer service life than conventional steels and withstand the most stringent environments.

Weight savings
When compared to conventional construction steels, sheet thicknesses can be significantly reduced while maintaining the same length of service life. This leads to lower dead weights and higher payloads, especially in automotive engineering.
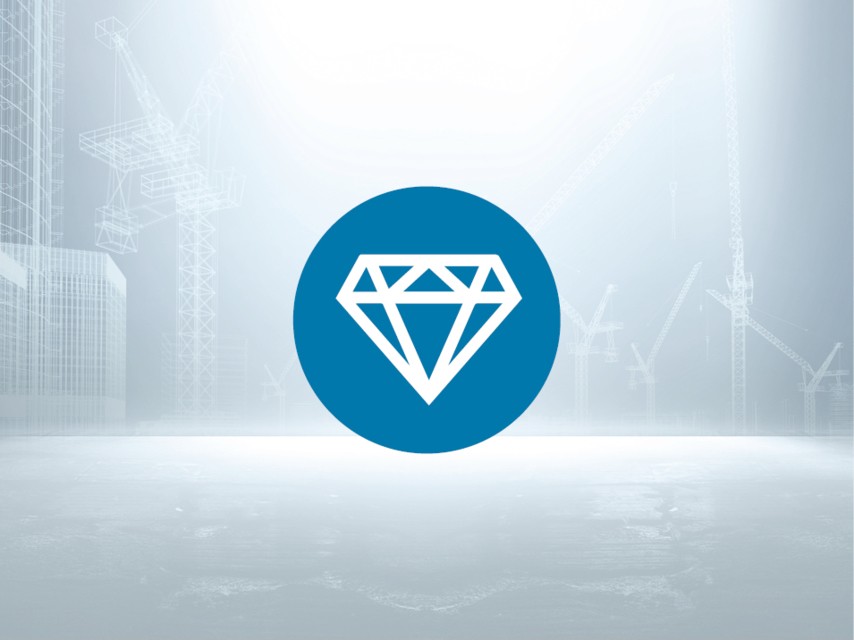
High degree of hardness
Their high level of hardness is adjusted by means of accelerated cooling after hot rolling (direct hardening) or through conventional quenching. We prefer direct hardening because this method improves toughness and reduces scale formation.
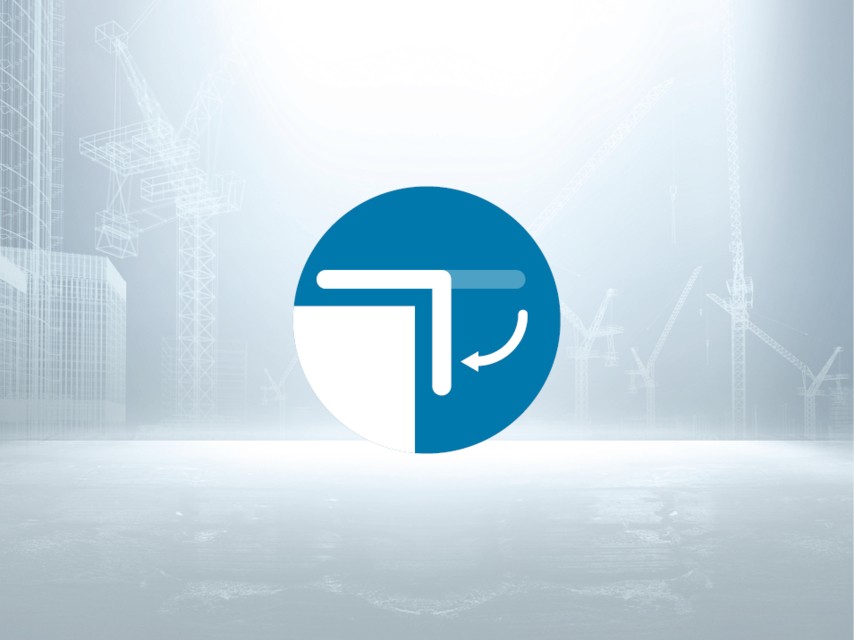
Very good cold formability
Our durostat® steel grades are very well suited to cold forming, independently of whether the steel is direct-hardened or non-hardened. This is achieved through a homogeneous, fine-grained structure as well as a high degree of purity.
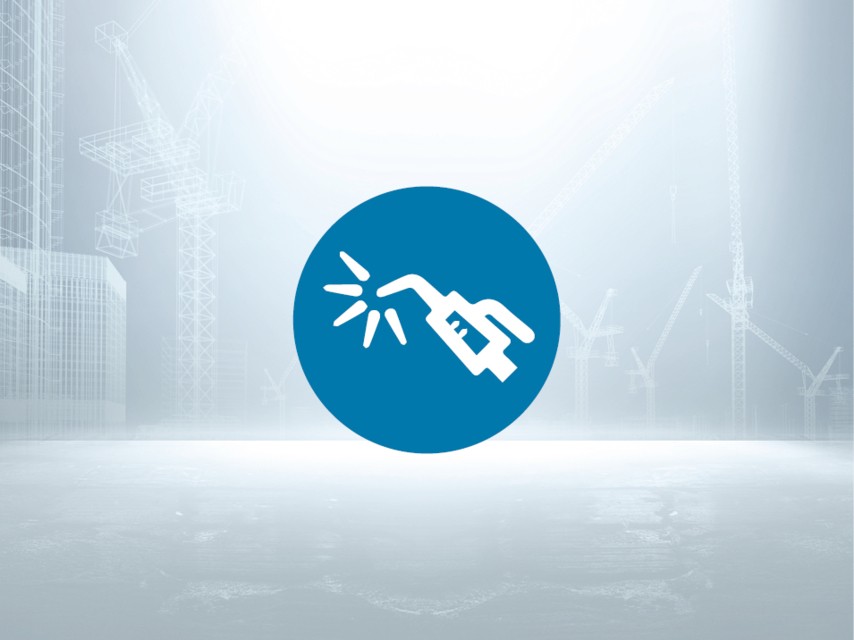
Good weldability
Our modern alloying strategies with optimized carbon equivalents guarantee good weldability, a factor that especially applies to direct-hardened durostat® steels. Preheating can be completely eliminated for lower sheet thicknesses.
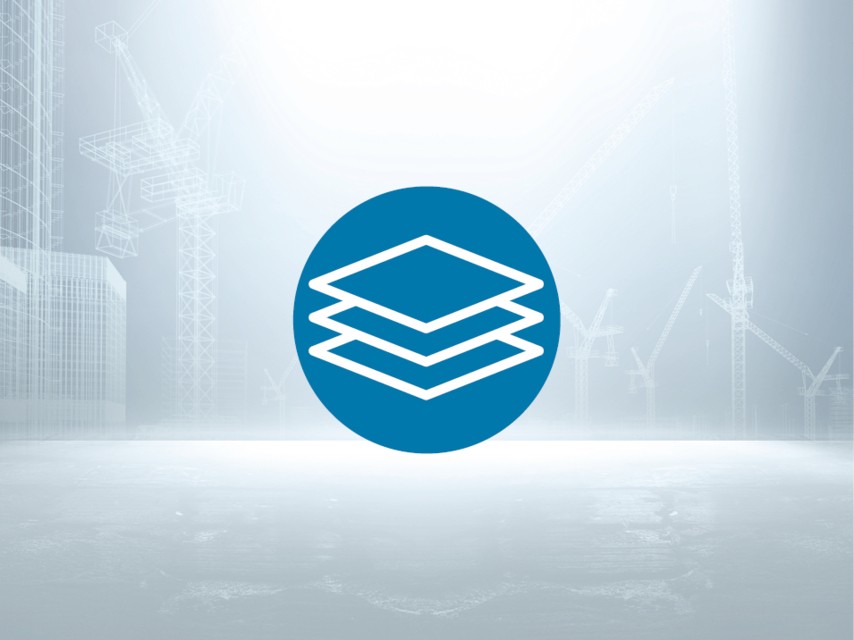
Excellent flatness
The outstanding flatness is achieved through precisely controlled rolling processes in combination with modern leveling units. This is highly advantageous during cutting and further processing and achieves optimized dimensional accuracy of the manufactured components.
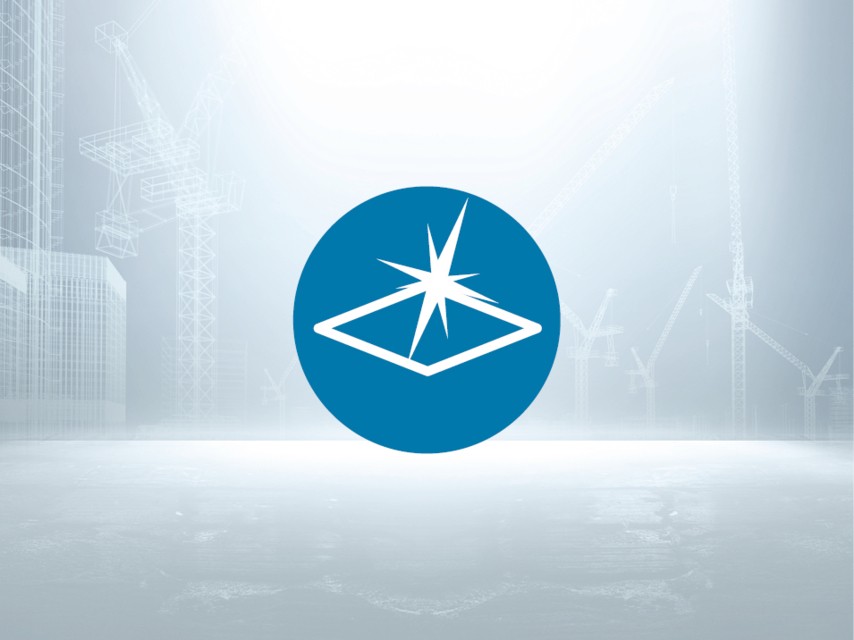
Clean surface
A uniform layer of scale forms on the sheet surface following hot rolling in our process route. The natural protective layer acts against corrosion during transport and can easily be removed through sand blasting. Selected dimensions can be supplied with a pickled surface, which makes it possible to forego descaling prior to coating.