Technological Innovation
To maintain our high product quality, the EAF uses a mix of scrap, liquid pig iron, and HBI (hot briquetted iron). HBI is manufactured in a so-called direct reduction process, in which natural gas rather than coal and coke is used to reduce iron ore to iron, resulting in fewer CO2 emissions.
We source most of the required HBI from a direct reduction plant in Texas, USA; this plant has been majority-owned by a global steel manufacturer since 2022, with voestalpine holding a 20 percent stake. As a result of this Texas stakeholding, we have signed a long-term supply contract for 420,000 tons of HBI annually. Having a secure supply of HBI and scrap as raw materials is a major competitive advantage for us.
Showcase project in the circular economy
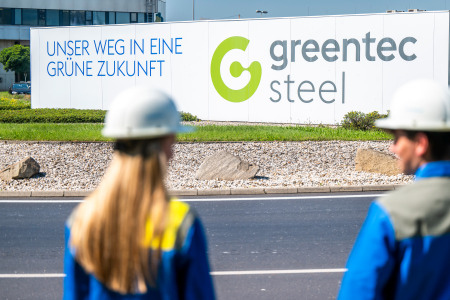
Due to the increasing demand for recycled materials, old scrap will increasingly have to be used in the future. Compared to new scrap, the reprocessing and sorting of old scrap is usually costly. Together with Mercedes-Benz and TSR Recycling, we have therefore launched a unique project in the field of recycling management.
Our continually evolving raw material concept will also allow us to manufacture green high-tech steels, such as those already used in the automotive and rail industries, both now and in the future.
Future route to high-quality steel
What is direct reduction?
Direct reduction is an important bridging technology for decarbonizing steel production. It uses natural gas instead of coal and coke to reduce iron ore to iron, thereby emitting less CO2. The direct reduction process is used to produce HBI, a sophisticated and environmentally friendly pre-material used in steel production.