The research projects cover the entire possible spectrum and include both Carbon Direct Avoidance (CDA) projects, i.e., projects that research new technical possibilities to avoid producing CO2, and Carbon Capture Utilization (CCU) projects aimed at converting CO2 into new storable products. Currently, our research is primarily focused on CDA projects, namely steel production processes with no carbon emissions. These include projects such as the testing facilities for carbon-neutral steel production which uses hydrogen to directly reduce iron ore (sustainable steelmaking) at the Donawitz site, and the H2FUTURE hydrogen pilot facility at the Linz site.
H2FUTURE
voestalpine.jpg)
The H2FUTURE hydrogen pilot facility has been operating at the site in Linz since 2019. With the commissioning of what is currently the world’s largest pilot plant for the carbon-neutral production of hydrogen, we are setting an international milestone in the advancement of new energy supply options. Since its launch, the test facility has successfully completed a number of test programs. Now, our focus lies on building on the knowledge obtained from research conducted to date, first and foremost in terms of hydrogen quality.
- Hydrogen pilot facility for the production and use of “green” hydrogen on an industrial scale
- Further research into the compression and purification of hydrogen
- Participation in the balancing energy market to compensate for fluctuations in the electricity grid
H2FUTURE project partners
SuSteel
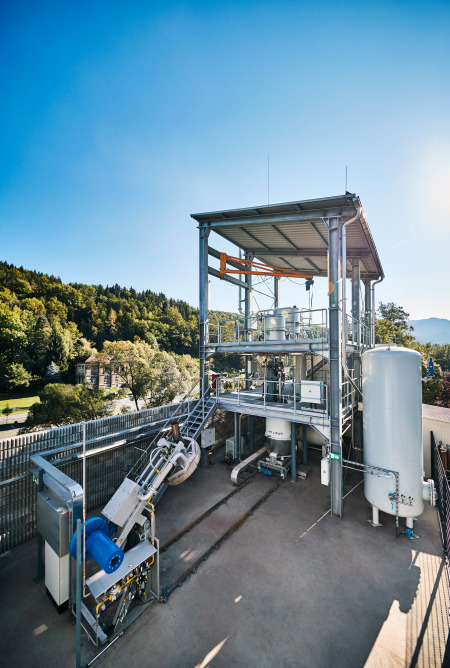
A testing facility is currently being established at the Donawitz site in Styria as part of the SuSteel (Sustainable Steelmaking) project. Here research will be undertaken into the carbon-neutral production of crude steel in a single process step using novel hydrogen plasma technology. In a form of electric arc furnace, steel is produced using hydrogen plasma to reduce ores, omitting the pig iron stage. The advantage is that climate-neutral water vapor is the only end product, allowing CO2 emissions to be avoided completely. This basic research project being run by the K1-MET metallurgy competence center has a very long-term implementation timeframe. The project involves voestalpine Stahl GmbH, voestalpine Stahl Donawitz GmbH, and the Montanuniversität Leoben.
- Reducing ores using innovative hydrogen plasma technology
- CO2 emissions could be completely avoided
- International showcase project
SuSteel project partners
HYFOR
The Hyfor research project, involving Primetals Technologies, voestalpine Stahl Donawitz GmbH, the Montanuniversität Leoben, and K1-MET, is also based at the site in Donawitz. The aim of the project is to build a pilot facility to test the reduction of iron ore fines in a fluid state using hydrogen. In an industrial-scale plant, the resulting hot sponge iron would then be melted down in an electric arc furnace or used to produce hot briquetted iron (HBI). The pilot facilities have already started testing, with the initial findings verifying the feasibility of this process.
- Using hydrogen to reduce iron ore fines
- Initial research findings confirm potential feasibility
- Objective: Base data for later conversion to an industrial plant
HYFOR project partners
ZEUS
The aim of the ZEUS project (Zero Emissions throUgh Sectorcoupling) is to establish and provide a cross-sectoral demonstration of a climate-neutral process chain, encompassing all elements from the production and treatment of green hydrogen to capturing carbon from industrial emissions and its subsequent conversion into valuable, storable products (CCU research project). To achieve this, various pilot plants are being looked into in an industrial environment (H2FUTURE plant, carbon capturing, catalytic methanation, CO2 electrolysis) and interconnected to create holistic process chains.
Projektpartner ZEUS
Underground Sun Storage 2030
Together with partners from industry and science, voestalpine is researching into the seasonal, underground storage of large volumes of green hydrogen as part of the Underground Sun Storage 2030 project led by RAG Austria. During the summer months, electrolysis is used to convert solar energy into pure hydrogen in a climate neutral process, with the hydrogen subsequently stored in former natural gas reservoirs for the winter months. A research facility will be built at a former natural gas reservoir in Gampern (Upper Austria) where the relevant testing will be conducted to 2025. voestalpine is also extensively investigating the possible uses for the stored hydrogen in energy-intensive industrial processes. This unique project, the only one of its kind in the world, is receiving funding as part of the Austrian Climate and Energy Fund’s energy research program.
- Electrolysis is used to convert solar energy into pure hydrogen
- Storage in former natural gas reservoirs for the winter months
- Planned construction of a research facility at a former natural gas reservoir in Gampern (Upper Austria)
- Investigation of the possible uses in energy-intensive industrial processes
- WIVA P&G funded research project
USS2030 Industrial project partners
Carbon Cycle Economy Demonstration (C-CED)
The „Carbon Cycle Economy Demonstration“ (C-CED) project is looking into creating a carbon cycle. CO2 generated in voestalpine industrial plants (which is present in the waste gas streams in varying concentrations) will be captured. Concentrated, compressed CO2 is pumped together with sustainably produced hydrogen into natural underground storage sites whose original natural gas content has been depleted. At a depth of about 800 meters, microorganisms indigenous to the site, known as archaea, combine the two gases to produce green methane, the main component of natural gas. This methanation process can take about four weeks. Additional source materials can be pumped in during this process. Like natural gas, the sustainably produced methane is extracted when needed and can be used in industrial processes or to produce electricity. CO2 is again generated and the cycle begins anew.
- CO2 from industrial processes is captured
- CO2 is stored together with sustainably produced hydrogen in natural underground storage sites
- Microbiological processes produce green methane gas
- The methane is used for industrial processes or to produce electric power