„DHO Heat4Future”
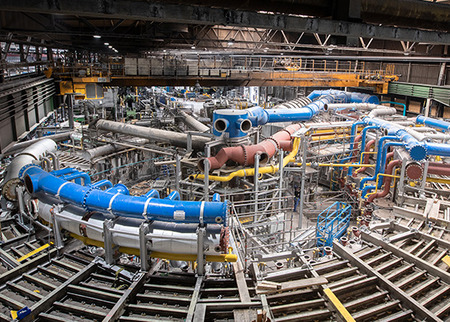
Nach einem dreiviertel Jahr Vorbereitungszeit und akribischer Planung arbeiteten zwischen 10. August und 11. September bis zu 200 interne und externe Personen an dem Umbau.
Nach einem dreiviertel Jahr Vorbereitungszeit und akribischer Planung arbeiteten zwischen 10. August und 11. September bis zu 200 interne und externe Personen an dem Umbau.
In Rekordzeit von nur vier Wochen haben wir es geschafft die Revision unseres Drehherdofens erfolgreich durchzuführen. Nach einem dreiviertel Jahr Vorbereitungszeit und akribischer Planung arbeiteten zwischen 10. August und 11. September bis zu 200 interne und externe Personen an dem Umbau. Das Raumvolumen des Ofens mit 24,5 Metern Durchmesser wurde verdoppelt und eine neue Generation der Regenerativbrenner mit niedrigeren Emissionswerten bei gleicher Leistung verbaut. Das Projektteam hat sich viel einfallen lassen, um die Umsetzungszeit so kurz wie möglich zu halten: vorkonfektionierte Fertigbauteile für die Montage, eine ausgeklügelte Lagerlogistik, eigens errichtete Infrastruktur vor Ort.
Ohne den großartigen Teamgeist, unsere Partnerunternehmen und das Vertrauen und die Unterstützung der Geschäftsführung wäre das Projekt nicht möglich gewesen.
Ein dreiviertel Jahr langt plante das Team vorab sämtliche Handgriffe bis hin zur letzten Schraube. 43 je fünf Tonnen schwere Wandelemente wurden vorkonfektioniert, damit möglichst komplette Teile in die Montage gehen konnten. Sie wurden dem Ablauf entsprechend und logistisch optimiert zwischengelagert. Für die vielen unterschiedlichen Teile und Materialien wurde außerdem ein Hochregallager mit 900 Paletten- Liegeplätze auf die grüne Wiese gebaut.
Mit einer Innenraumtemperatur von 1.400 Grad benötigt der Ofen zunächst vier Tage zum Abkühlen. Selbst nach dieser Abkühlphase konnten die Arbeiten bei rund 60 Grad Resttemperatur nur mit spezieller Schutzausrüstung durchgeführt werden. Abriss und Aufbau fanden bei der Revision fast gleichzeitig statt: Abkühlphase, Abbrechen der Rohrleitungen, Eröffnen der Decke für eine noch schnelleres Abkühlen, Abriss und Neubau des Stahlbaus, Wiederaufbau der Wände, Legen der Rohrleitungen und Elektroinstallation, Inbetriebnahme. Um behutsam wieder auf die benötigte Betriebstemperatur zu kommen, benötigte der Ofen fünf Tage.
Das Aufheizen musste langsam passieren, um Schäden an dem komplexen fünfschichtigen Ofenwandaufbau zu vermeiden. Rund 1.000 Tonnen Feuerfestmaterial wurden bei der Revision eingebaut und das Raumvolumen des Ofens verdoppelt. Die verbaute neue Generation der Regenerativbrenner überzeugt nicht nur mit niedrigeren Emissionswerten bei gleicher Leistung, sie ist außerdem bereits für sämtliche zukünftige Brennmedien wie Wasserstoff oder Ammoniak geeignet.
Es waren so viele Profis und absolute Fachleute im Einsatz, dass nie ein Problem entstand, da immer sofort eine Lösung bereit war.
Bis zu 200 Leute waren mit dem Projekt „DHO Heat4Future” beschäftigt:
Bei so vielen zusätzlichen Personen am Werksgelände wurde das Projektteam auch bei der Infrastruktur für die tägliche Versorgung kreativ: Um keine Zeit beim Anstehen in der Kantine zu verlieren, wurden die Beteiligten direkt auf der Baustelle mit Verpflegung versorgt, überdachte zweistöckige Containerdörfer beheimateten Sozialräume, Duschen und WCs vor Ort.
In zwei 12-Stundenschichten arbeiteten die Gewerke rund um die Uhr an der Umsetzung des Projekts. „Das tolle Teamwork und dass wir Firmen unseres Vertrauens beauftragen konnten, war der Schlüssel zum Gelingen“, so Heinz Teuschl. „Wir waren ein wirklich gutes Team und alle Beteiligten waren immer lösungsorientiert“, ergänzt Christian Schnitzler.
In dem runden Ofen mit 24,5 Meter Durchmesser werden die vorgeschnittenen Blöcke auf die Walztemperatur von 1.280 Grad erwärmt. Dazu werden die Blöcke in den sich drehenden Ofen eingelegt, wo sie nach einer Umdrehung und einer Verweilzeit von 130 Minuten die optimale Temperatur für die Weiterverarbeitung erreichen. Die Flammentemperatur beträgt 2.000 Grad, aufgelegt werden die Blöcke auf 1.400 Grad. Der Ofen ist dabei besonders platzsparend: Wäre ein gestreckter Ofen im Einsatz, wäre dieser fast 75 Meter lang.