WE TAKE ACTION!
We are bursting with energy, preferably in the form of gas. We use the top gas we produce during steelmaking as an important source of energy. Our added value is high and flare loss low. This is the definition of efficiency.
ONE STEP AHEAD IN ENERGY MANAGEMENT
The global climate objectives foresee a climate-neutral European economy by 2050, with an 80 to 95 percent reduction in CO2 emissions. This requires steps in every different direction. One of the many measures taken by voestalpine is optimum use of the top gas we produce during steelmaking.
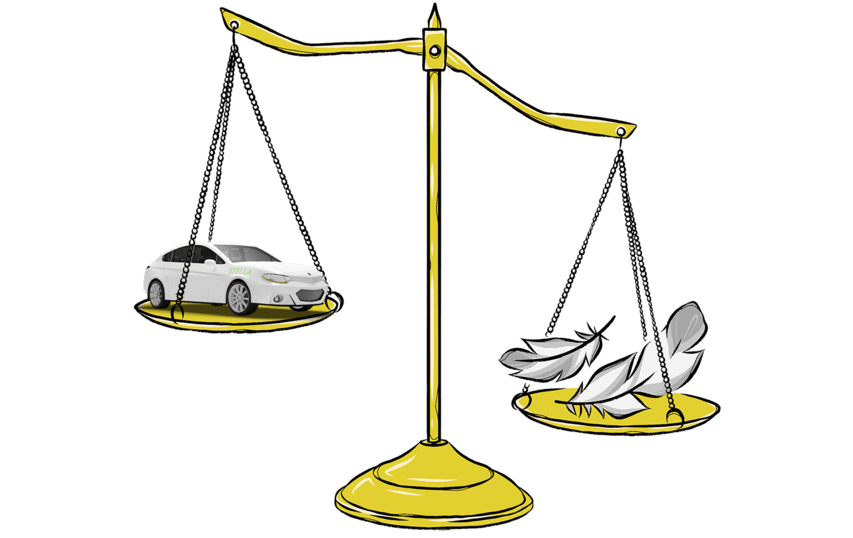
LIGHTWEIGHT PRODUCT SUCCESS
The innovative advanced high-strength steels developed by voestalpine are an important high-strength part of our mission to improve the future of lightweight automotive design. The fuel-saving reduction of weight in car bodies by up to 35 percent ensures up to 70 percent less CO2 across the entire lifecycle. The good processability of advanced voestalpine steel components also reduces energy and cost input in component production.
DURING PRODUCTION: FULLY ENERGY EFFICIENT
Sustainably increasing the energy efficiency of our production lines and technologies is another core mission of voestalpine and its employees. Over the past few years alone, 700 creative ideas have been introduced in the fields of energy and energy efficiency.
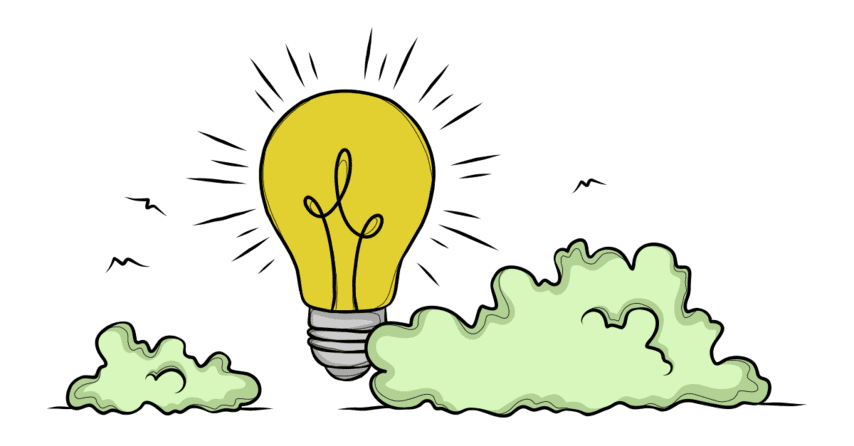
NOTHING GOES UP IN SMOKE.
The energy management of top gas is only one example of many. In the steelmaking process, coke oven gas is produced in the coking plant, while blast furnace and converter gases are produced in the blast furnace and steelmaking plant. These gases are generally referred to as top gas and are processed as soon as they are extracted. They are stored in gasometers and used in the voestalpine power plant to generate energy. The process requires closely coordinated control of the energy system. Sometimes, when a malfunction occurs in the system, the top gas must be burned in a flare stack, resulting in so-called flare loss. Modern measuring technologies, digital intelligence, digital controls and infrastructural network optimizations have substantially increased efficient energy use in recent years, and flare losses have been minimized considerably. Here are some of the figures: In 2020 we reduced the energy of flare losses by roughly 380 GWh as compared to 2009. That corresponds to the annual heating energy requirement of approximately 20,000 households. This is an enormous amount of conserved energy.
PURCHASE OF GREEN ENERGY AS AN ADDITIONAL BENEFIT
A lot is going on in the electricity market of today. Electric power that is discontinuously generated by means of renewable energy sources such as photovoltaics has also made a contribution to this increased activity. But the sun doesn't shine all the time. This leads to a constant fluctuation in the electric power market. When the level of power supply is high, the share of power supplied from renewable sources is also high, and this is when voestalpine purchases electricity. This is when our top gas is placed in interim storage. When less electricity is available on the market, meaning that the proportion of green electricity is also lower, we use surplus top gas to generate our own electricity at voestalpine. This is how we indirectly support the generation of electricity using renewable sources.
PS: THE FUTURE IS HYDROGEN
The optimization of existing forms of energy and solutions is only one of our focuses in the Group. But we will have to take a completely new path if we truly want to leave a green footprint. This is why the largest pilot plant in the world for the CO2-free production of hydrogen has already been put into operation at voestalpine in Linz. The H2FUTURE project, which is funded by the European Union, is where voestalpine and partners are researching the industrial production of green hydrogen that can replace fossil fuels in a new steelmaking technology. More about this in the future.
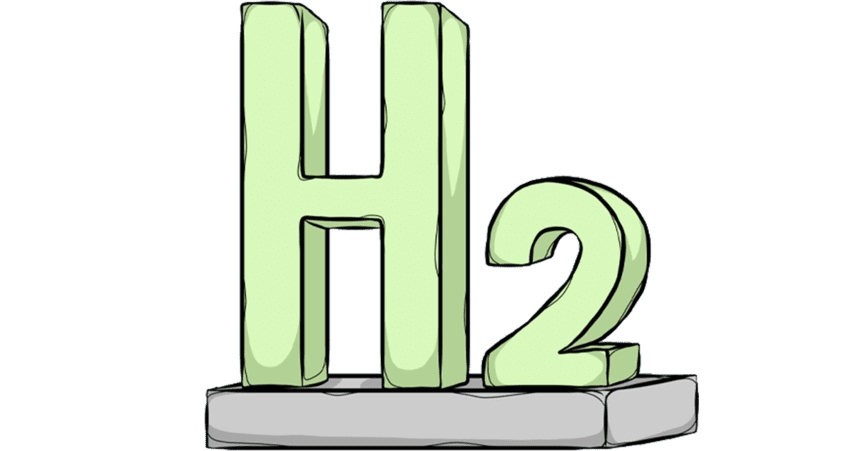