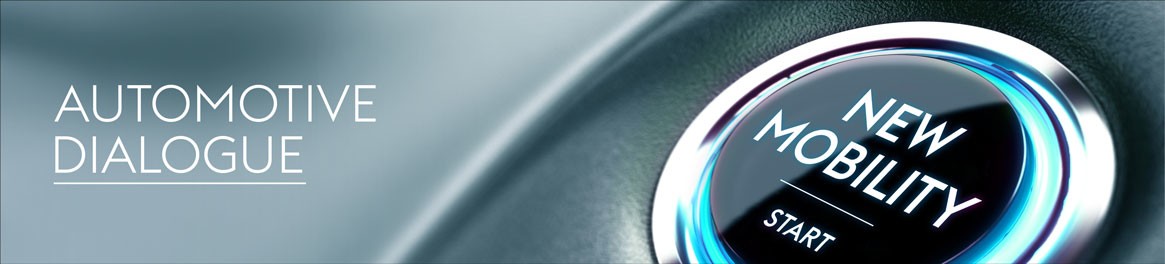
Steel meets new perspectives
Nachhaltigkeit, E-Mobility, die Welt ist in Bewegung. Was bewegt Toyota, was die Entwicklungsspezialisten von Bertrandt, die Stahlexperten der voestalpine, was Newcomer wie Fisker oder NIO? Wie ist es für Magna Steyr mit einem Startup zusammenzuarbeiten? Der Automotive Dialogue gab Antworten, Anregungen und Austausch.
Es war bereits die zweite Online-Veranstaltung dieser Art der voestalpine Steel Division. Die Resonanz gewaltig. Rund 1.000 Teilnehmer waren online dabei – an einem Nachmittag, der verband. Etablierte OEMs und Startups. Information und Inspiration. Von Experten für Experten – in kurzweiligen Vorträgen und mit der Möglichkeit für alle Teilnehmer direkt Fragen zu stellen.
Einblick und Überblick
Einen Überblick über die Inhalte der Sessions finden Sie hier. Wenn Sie Interesse am gesamten Stream haben und weitere Informationen wünschen, klicken Sie den Button.
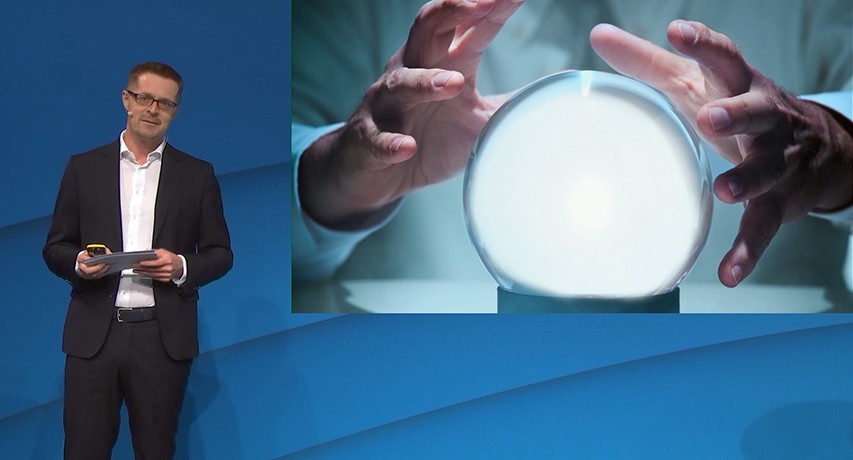
Perspectives on mobility
Wie geht es weiter – mit der Automobilindustrie, der Mobilität und generell? Grundlegende Überlegungen zum Umgang mit der Zukunft eröffnen den Automotive Dialogue.
Verlässlichkeit als Basis
Bei allen Herausforderungen der Zukunft darf eine Tugend der Automobilindustrie nicht verloren gehen: die Stabilität – und damit die Sicherheit und Fähigkeit sich aufeinander zu verlassen und planen zu können.
Konkrete Vorhersagbarkeit?
Bei konkreten Aussagen, was, wann, in welchem Umfang eintreten wird, ist Vorsicht geboten. Auch die besten Analysten übersehen Anzeichen, die vielleicht zu diesem Zeitpunkt noch klein sind, aber für die Zukunft bedeutend und groß werden. Auch können „Fortune Tellers“ ihre Vorhersagen nur auf den Erfahrungen der Vergangenheit aufbauen. Darüber hinaus fehlt uns die Vorstellungskraft für disruptive, neue Entwicklungen.
Perspektiven und Szenarien
Ein Weg mit den Unsicherheiten umzugehen, ist, statt punktueller Vorhersagen, Szenarien und Perspektiven zu entwickeln und in strategischen Horizonten zu denken – um dadurch auch flexibler zu sein.
Miteinander im Dialog
Miteinander und in Wechselwirkung entsteht Zukunft. Der Automotive Dialogue versteht sich als Plattform, die Stahlentwickler, Anwender, Themen wie neue Mobilität und Nachhaltigkeit, Startups und etablierte OEMs vereint – um sich auszutauschen, voneinander zu lernen und zu profitieren.
Toyotas roadmap towards carbon neutrality
Toyota, eine der weltweit führenden Automarken, geht auch bei der Umweltverantwortung voran. Das Ziel ist, bis 2050 als Unternehmen inklusive den Produkten klimaneutral zu sein. Toyota setzt dazu umfassende Aktivitäten und treibt Entwicklungen voran.
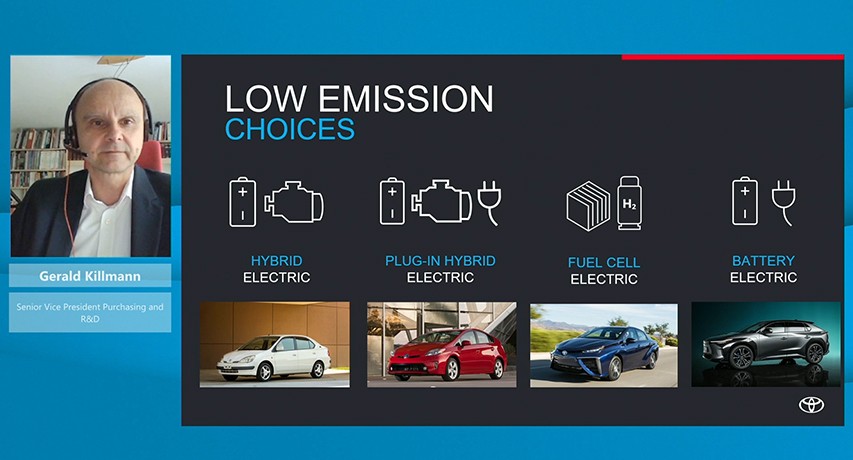
Ziele und Zwischenstand
Als einer der ersten OEMs hat Toyota schon 2015 die zu bewältigenden Herausforderungen zur Erreichung der CO2-Neutralität definiert. Heute bereits versorgt 100 % grüne Elektrizität die europäischen Produktionsstätten in Frankreich und Tschechien. Beide Standorte sollen bereits 2030 klimaneutral produzieren, 5 Jahre später sogar die weltweite Produktion. Klimaneutralität für das gesamte Unternehmen und seine Produkte soll 2050 erreicht sein, in Europa ein paar Jahre früher.
Kernfaktor E-Kompetenz
Toyota hat Erfahrung. Seit 1997 hat Toyota 20 Millionen hoch elektrifizierte Autos auf die Straßen der Welt gebracht. E-Fahrzeuge sind die Zukunft. Die ganze Palette an elektrifizierten Fahrzeugen ist im Portfolio: Hybrid, Plug-in Hybrid, Fuel Cell, Battery. Der Fokus wird auf Hybrid- und Battery-Fahrzeuge gelegt.
Toyota Bekenntnis zur Leistbarkeit
"Unser Weg ist, mit zunehmender Elektrifizierung CO2 zu reduzieren, indem wir leistbare umweltfreundliche Fahrzeuge anbieten. Damit leisten wir einen Beitrag zur Demokratisierung der umweltfreundlichen individuellen Mobilität."
Partnerschaftliche Stahlentwicklung
Besonders im Hinblick auf Crash-Sicherheit sind Festigkeit und Formbarkeit wesentliche Kriterien bei Stählen. Gemeinsam entwickelten Toyota und voestalpine TBF Stähle mit 980 MPa und 1.200 MPa . Das ermöglicht es, bei Bauteilen die Dicke zu reduzieren und ihre Form zu optimieren. Dadurch können die Bauteile leichter gemacht werden, was wiederum dem Energieverbrauch und der Umwelt zugutekommt.
Technologische Weiterentwicklungen
Die aktuelle 5. Generation der Toyota Hybrid-Fahrzeuge wird über ein um 40 % leichteres Lithium-Ionen-Battery-Pack bei gleichzeitig höherer Leistung verfügen. Bei den emissionsfreien, rein batteriebetriebenen Fahrzeugen ist man mit der Submarke Toyota bZ voran. Das erste auf einer speziellen Plattform (eTNGA) gefertigte Modell bietet mit zwei Motoren Vierradantrieb in voller SUV-Performance. Darüber hinaus ist die weltweit erste Bipolar-NiMH-Batterie in Produktion. Sie ist kleiner, leichter und benötigt weniger seltene Materialien.
Brennstoffzellen-Technologie
Brennstoffzellenmodule der zweiten Generation sind in Produktion. Bei Energielösungen mit Wasserstoff denkt man von mobilen Anwendungen wie in Schiffen, Zügen, Bussen, PKW (Toyota Mirai) bis hin zur Versorgung von Städten. Zur Demonstration wurde jüngst der Eiffelturm mit Energie aus Toyota-Brennstoffzellenmodulen beleuchtet.
Publikumsfrage
Wie sieht die Zukunft für BEVs (Battery Electric Vehicles) aus?
Hr. Killmann: Grundsätzlich denken wir, jede Batterie, auch in Hybrid-Fahrzeugen, senkt die CO2-Emissionen. Wenn die Produktionskapazitäten bei Batterien steigen, dann ist zweifelsfrei die Zeit für BEV gekommen. Wir sind darauf vorbereitet und auf Kurs.
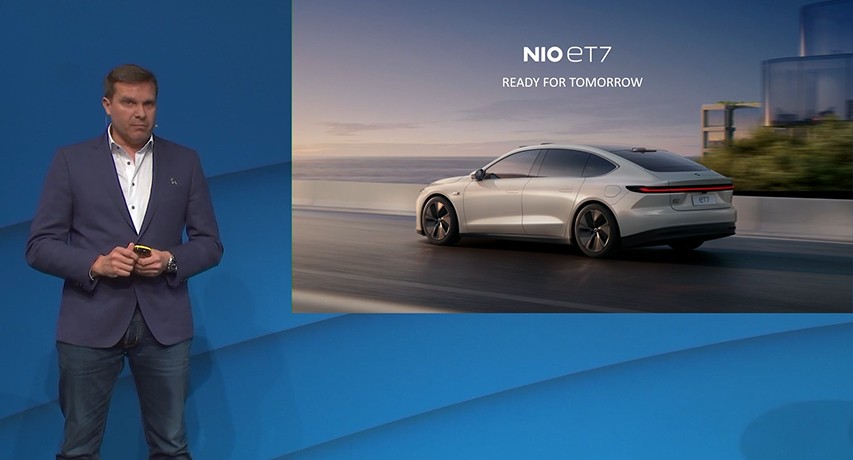
NIO – User enterprise
NIO steht für smarte elektrifizierte Autos im Premium-Segment. Innovative Technologie, ansprechendes Design und ein interessanter Stromversorgungsansatz kennzeichnen NIO ebenso wie der Anspruch: der User steht im Mittelpunkt.
Das Unternehmen
2014 gegründet ist NIO ein schnell wachsendes Unternehmen mit 16.000 Mitarbeitern. Headquarter ist in Shanghai, das globale Design-Headquarter in München. Bis April 2022 wurden bereits 200.000 Elektrofahrzeuge verkauft. Mit einer ersten Niederlassung in Oslo ist der Sprung nach Europa bereits getan.
To shape a joyful life
Dem User das Leben mit einem NIO so angenehm wie möglich zu machen, leitet NIO. So soll das neueste Modell, der NIO ET7, 1.000 km Reichweite bei purem Elektroantrieb haben. 33 Kameras und Sensoren machen den NIO fit für das autonome Fahren der Zukunft. Und seit Beginn der Firmengründung wurde für das Betriebssystem der Gedanke eines kabellosen Software-Upgrades verfolgt.
Innovative Infrastruktur
Geplant ist, ein Netz von Energieversorgungstellen aufzubauen, das mehr kann, als das schnelle Aufladen der Batterie: In 5 Minuten ist der gesamte Battery Pack ausgetauscht. Der Kunde kann zwischen verschiedenen Batterieleistungsklassen wählen. Und da man die Batterie für sein Auto auch leasen kann, ergibt sich ein Kostenvorteil. 900 dieser „Battery Swap Stationen“ sind bereits gebaut.
Nachhaltigkeit
Heuer noch verabschiedet sich NIO von Plastik in der Innenausstattung. Es wird durch ein natürliches Material aus der Rattan-Palme ersetzt. Ein deutsches Start-up brachte NIO auf die Idee, es im NIO ET7 einzusetzen. Die Europapremiere des ET7 erfolgt noch dieses Jahr. Insgesamt arbeitet NIO mit 160 Partnern zusammen, die alle an einer CO2-neutralen Mobilität der Zukunft arbeiten.
Publikumsfrage
Wo und wie soll das Netz an "Battery Swap Stations" aufgebaut werden?
Hr. Otto: 2025 werden es 4.000 sein, davon 900 außerhalb Chinas. In China arbeiten wir mit einem führenden Ölunternehmen und Tankstellenbetreiber zusammen. Eine Absichtserklärung mit Shell ist bereits unterzeichnet.
Strategy for sustainable battery lifecycle
Mit mehr als 50 Sandorten zählt die Bertrandt-Gruppe zu den international führenden Engineering-Unternehmen. Die Projekte und Inhalte ändern sich: E-Mobilität und Nachhaltigkeit nehmen einen großen Stellenwert ein.
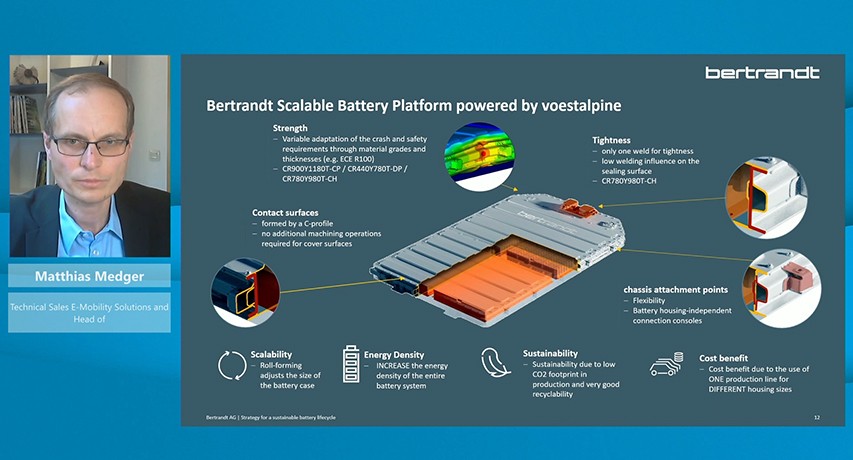
Leistung und Branchen
Bertrandt verfolgt einen ganzheitlichen Ansatz und bietet die komplette Produktentwicklung von der ersten Idee bis zum serienreifen Produkt und den gesamten Lifecycle. Kundenbranchen sind, als größter Bereich, der Automotive-Sektor, ergänzt von der Luft- und Raumfahrt sowie die Medizintechnik.
Megatrends
Megatrends, die auch Projekte und Produkte verändern, sind Digitalisierung, autonomes Fahren, die Konnektivität (d.h. die Verbindung mit dem Software-Elektronik-Bereich) sowie übergeordnet E-Mobilität und Nachhaltigkeit.
Nachhaltigkeit bei Hochvolt-Batterien
Im Bereich der Elektromobilität ist die Entwicklung von Hochvolt-Batterien das Kerngeschäft. Der Bertrandt-Ansatz ist Lebensdauermaximierung und Kostenreduktion durch eine ganzheitliche Betrachtung des Batterielebens. Wobei dabei das Thema Nachhaltigkeit heute einen weitaus höheren Stellenwert als noch vor wenigen Jahren einnimmt.
Vor wenigen Jahren galt es, eine für die Produktion und den Einsatz optimale Batterie zu entwickeln. Heute sind vom ersten Entwicklungsschritt an zusätzlich die Wiederaufbereitung, die Ersatzteillogistik und das Recycling einzuplanen.
Bertrandt Scalable Battery Box – powered by voestalpine
voestalpine brachte bei diesem Projekt ihre Kompetenz in Stahl und Stahlverarbeitung ein, Bertrandt die Entwicklungskompetenz. Das Ergebnis ist eine skalierbare Modullösung für einen Batteriekasten, der auch wirtschaftlich hergestellt werden kann, und damit maßgeblich zu Nachhaltigkeit und Kostenreduktion beiträgt.
Beispielhaftes Rüttel-Prüfsystem
Bertrandt entwickelt Hochvolt-Batterien und sorgt auch dafür, dass sie effizient und nachhaltig validiert werden können. Mit dem von Bertrandt entwickelten "Multi Axis Shaker Table" kann der Lebenszyklus einer Batterie simuliert werden, egal ob kalte Winter oder heiße Sommer. Lasten bis zu 850 kg können in allen 6 Raumachsen aufgebracht werden und die Batterie kann mit bis zu 1.200 Volt und +/– 1.200 Ampere bei einer Gesamtleistung von 400 kW dauerhaft geladen werden.
Publikumsfrage
Warum verwendeten Sie Stahl als Material für das Projekt „Scalabe Battery Box“?
Hr. Medger: Nachhaltigkeit und Kosteneffizienz waren die Gründe. Mit Stahl kann man auf einer Linie verschiedene Größen von Batteriekästen erzeugen. Darüber hinaus ist Stahl für die Massenproduktion im Rollforming-Prozess ideal geeignet.
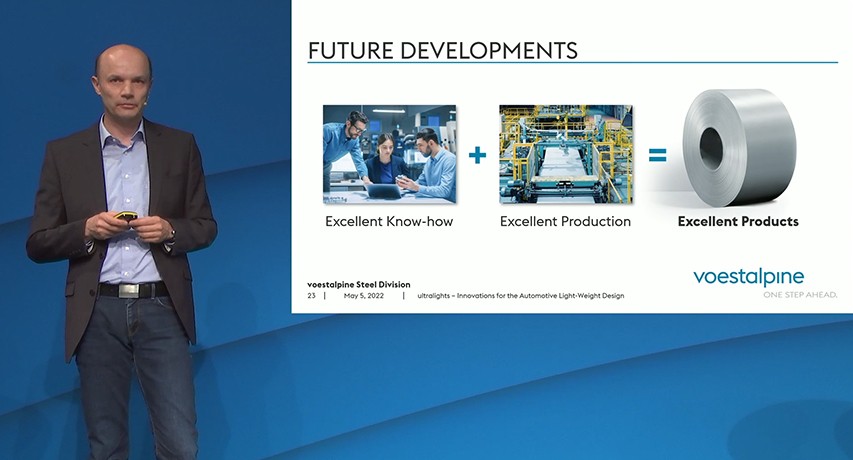
ultralights by voestalpine -innovations for lightweight automotive design
Im Kompetenzfeld ultralights bündelt die voestalpine ihre Werkstoffexpertise mit ihrem Know-how für den automobilen Leichtbau und bietet ein Stahlportfolio, das die höchsten und unterschiedlichsten Anforderungen erfüllt. Permanente Weitentwicklung ist Programm.
Kaltumformstähle
Mit über drei Jahrzehnten Erfahrung im Bereich der Advanced HighStrength Steels (ahss) ist voestalpine Entwicklungspionier und Experte bei hochfesten Kaltumformstählen. Das Portfolio bietet
- ahss classic – mit Complexphasen-Stählen, die sich durch hohe Bieg- und Bördelbarkeit auszeichnen, und mit Dualphasen-Stählen, die hohe Zugfestigkeit, Gleichmaß- und Bruchdehnung sowie ausgezeichnete Tiefzieheigenschaften aufweisen.
- ahss high-ductility – eine voestalpine Weiterentwicklung der klassischen ahss-Stähle mit einer bisher unerreichten Balance aus Festigkeit, Biegbarkeit und Schweißeignung.
- martensitic steels –wenn noch höhere Festigkeiten gefordert sind. Sie empfehlen sich für das Rollprofilieren. Coming soon: der voestalpine martensitc steel mit 1.500 MPa.
- hot-rolled drive – wenn mehr Dicke benötigt wird. Sie erfüllen die Anforderungen der VDA 239-100 und umfassen Güten mit ausgezeichneter lokaler wie globaler Duktilität.
Warmumformstähle
Wenn es im automobilen Leichtbau um Bauteilfertigung aus verzinkten presshärtenden Stählen (phs) mittels Warmumformung geht, ist voestalpine der Partner. Das Spektrum ermöglicht Bauteile von höchster Festigkeit, komplexen Geometrien, hoher Maßgenauigkeit und bestem Korrosionsschutz:
- phs-ultraform® – für große und komplexe Bauteile in indirekter Warmumformung
- phs-dircform® – für eine breite Palette an Bauteilen in direkter Warmumformung
- phs-multiform® – für hohe Produktivität in einem Mehrschrittprozess
- phs-scalefee® –der erste Warmumformstahl bis 2.000 MPa, sowohl für die direkte als auch indirekte Warmumformung mit dünner Zinkbeschichtung
Anschauliche Gewichtsersparnis
Anhand eines Modell-Mittelklassewagen haben voestalpine Experten die verwendeten Originalstähle mit möglichen ultralights-Alternativen verglichen. Die Ergebnisse dieser „SLIMulations“ sprechen für sich: Innovative ultralights-Stähle bieten dieselbe Crash-Performance bei deutlich reduziertem Gewicht. Die gewichtigen Ersparnisse finden Sie hier: https://www.voestalpine.com/ultralights/Anwendungen/Slimulations
Fit für die Zukunft
Ein neues Lab Center für die "Physical Simulation" ist im Entstehen. voestalpine kann die gesamte Prozesskette von der Stahlschmelze bis zum fertigen Produkt in Laborgröße ausführen. "Trial und Error" bekommt so eine neue reale Dimension.
Mit dem Projekt "TransVer" erfolgt das Upgrade der Feuerverzinkungsanlagen 4 und 5. Nach dem Umbau wird es möglich sein, Stähle von noch höheren Festigkeiten mit weiter optimierten Dehnungswerten in einem noch größeren Abmessungsspektrum zu liefern.
Publikumsfrage
Sehen Sie bei der Entwicklung von Stählen Festigkeitsgrenzen?
Hr. Hebesberger: Bei Stählen für die Kaltumformung werden sie bei 1.500 MPa oder vielleicht 1.700 MPa liegen. Bei Warmumformstählen wahrscheinlich bei 2.000 MPa. Entwicklungspotenzial sehen wir bei der Formbarkeit und Verarbeitbarkeit, zum Beispiel bei der Schweißeignung.
The Toolbox – How the Metal Forming Division meets the challenges of mobility
Innovative Stähle sind eine Kompetenz der voestalpine – Verarbeitungskompetenz und Innovationskraft die anderen. Die "Metall-Former" der voestalpine begegnen den Herausforderungen der Zukunft mit einer umfangreichen Toolbox.
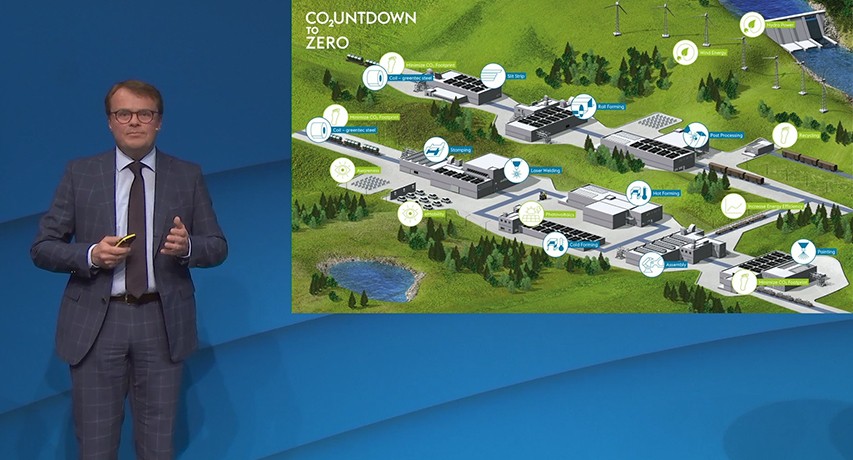
Verändernde Herausforderungen
In der Automotive-Welt sind aus Sicht der Metal Forming Division die Themen Leichtbau, Sicherheit und Leistbarkeit treibende Parameter. Für den Mobilitätsweg in die Zukunft kommt Flexibilität sowohl in der Produktion als auch bei der Supply Chain hinzu. Und last but not least: Nachhaltigkeit.
Nachhaltigkeit
Mit "CO2untdown to Zero" verfolgt die Metal Forming Division das Ziel, bis 2035 CO2-neutal zu sein. Die gesamte Wertschöpfungskette wird überprüft, Potenziale definiert und Maßnahmen umgesetzt. Bereits heute kommt umweltfreundlicher Strom aus dem eigenen Wasserkraftwerk und durch Sonnenenergie.
Innovative Produktlösungen
Zwei aktuelle Beispiele aus dem Bereich E-Mobilität:
- voestalpine hat vollflächig verklebte Lamellenpakete für Rotoren und Statoren in E-Motoren entwickelt. Sie sorgen für leiseren Lauf, erhalten die vollen magnetischen Eigenschaften, tragen zur Leistungssteigerung bei und sind ideal für eine wirtschaftliche Großserienfertigung.
- Batteriekästen sind entscheidende Elemente für die Sicherheit elektrifizierter Fahrzeuge. voestalpine hat im Bereich Batteriekästen bereits seit etlichen Jahren gezielt Kompetenz aufgebaut und bietet sichere Lösungen mit hochfesten und ultrahochfesten Stählen.
Stähle und Umformtechnologien
Im Fokus bei allen Stahlentwicklungen ist auch stets die Umformbarkeit. Kaltumformung, Warmumformung, Rollformen – voestalpine bietet ein komplettes Portfolio bei hochfesten und ultrahochfesten Stählen. Mit der Entwicklung des Warmumformstahls phs-scalefreeâ ist die Festigkeit von 2.000 MPa nun Realität.
Auch bei Außenhautstählen sind ultrahochfeste Stähle in Entwicklung und werden das Portfolio ergänzen.
Fertigung
"Wir können auch essen, was wir kochen!" Die Unternehmen der Metal Forming Division sind der wirtschaftliche Fertigungspartner von Teilen und Komponenten. Die Flexibilität und Leistungsfähigkeit wird –mit einem umfassenden Ansatz bis zum Einsatz künstlicher Intelligenz – permanent optimiert.
Publikumsfrage
Macht die voestalpine einen Unterschied in der Zusammenarbeit mit etablierten OEMs und Newcomern am Markt?
Hr. Traxler: Nein. Ein Kunde ist für uns ein Kunde. Wir wollen bei allen Kunden mit unseren Produkten und unserem Know-how bestmöglich zu ihrem Erfolg beitragen – von der Fertigung, dem Supply-Chain-Management bis hin zur Logistik.
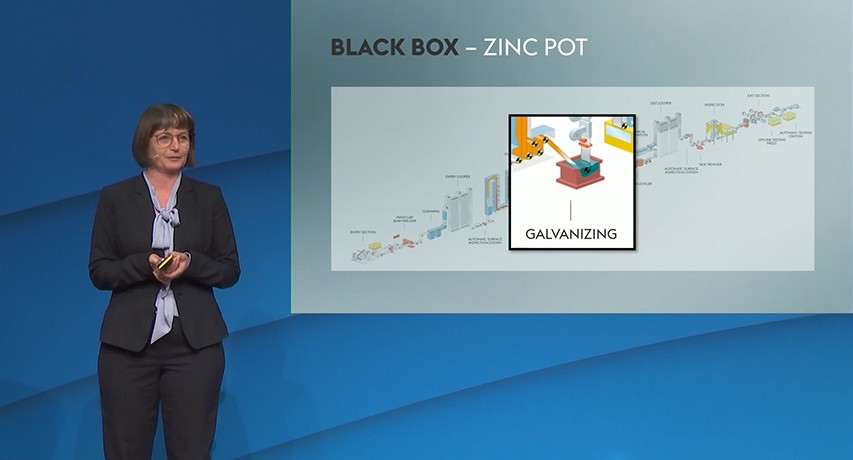
Exposed panels in the change of time
Innere Schönheit ist nicht alles. Bei Automobilen spielt auch die äußere Schönheit eine wichtige Rolle. Eine Zeitreise zeigt, wie sich die Schönheit von Außenhautteilen entwickelt hat. Heute gilt: perfekte Oberflächen sind ein Muss, doch müssen Außenhautteile auch dem Zahn der Zeit rostfrei widerstehen.
Hölzerne Anfänge
Die ersten selbstfahrenden Fahrzeuge wurden, wie die Kutschen, in Handwerksarbeit aus Holz gefertigt. Schnell hat man erkannt: Holz splittert, kann nur gedämpft und in einfache Rundungen gebogen werden. Schon im ersten Jahrzehnt des 20. Jahrhunderts kamen Metalle im Karosseriebau auf – nahezu parallel dazu neue Fertigungstechniken, wie das Schweißen. 1914 brachten die Dodge-Brüder das erste All-Steel-Auto auf den Markt.
Salz fördert die Stahlverzinkung
Für mehr Wintersicherheit auf den Straßen sorgte nach dem zweiten Weltkrieg die Salzstreuung. Das Ergebnis für die Automobile: eine schockierende Rostbilanz. Die Verzinkung des Stahls warf aber vielfältige Probleme auf. Das Punktschweißen und die Lackierung funktionierte nicht wie gewünscht und die Oberflächen waren uneben. Bis in die 1970iger Jahre wurden verzinkte Bleche deshalb fast nur für nicht sichtbare Karosserieteile verwendet. Neue Technologien (Air Knives) verbesserten die Situation. 1985 ging der erste vollverzinkte Audi in Serienproduktion.
Ab etwa 1990 wurde für Außenteile verstärkt Aluminium verwendet. Nach der Jahrtausendwende wurde die Beschichtungspalette mit der neuen ZnMg-Beschichtung erweitert.
Dünnere Lackschichten, neue Herausforderungen
Integrierte Lackierprozesse ermöglichten eine Verringerung der Lackdicke. Durch diese Reduzierung verringerte sich jedoch die tolerierbare Defektgröße innerhalb der Lackschicht deutlich. Die kritische Partikelgröße wurde auf etwa 20-30 µm reduziert – das entspricht rund der Hälfte der Dicke eines menschlichen Haares. Die Bildung dieser Eisen-Aluminium-Partikel kann leider nicht vollständig vermieden werden, da Eisen kontinuierlich aus dem Stahlband in das Zinkbad gelöst wird.
voestalpine Strömungsdynamik-Prozessmodell
Ein von voestalpine entwickeltes computergestütztes Strömungsdynamik-Prozessmodell ermöglicht die grundlegenden Prozesse im Zinkbad zu verstehen. Wir wissen, wann, warum und wie viele der vorhin erwähnten Eisen-Aluminium-Partikel ausfallen. Darauf aufbauend können optimierte Produktionspläne erstellt und Oberflächen in höchster Perfektion erzielt werden.
Im nächsten Schritt wird das Modell zu einem digitalen Zwilling des industriellen Zinkbades weiterentwickelt. Dann können kritische Bedingungen im Zinkbad früher erkannt werden. Der Bediener kann verschiedene Szenarien simulieren, um die besten Gegenmaßnahmen zu finden, bevor kritische Fehler auf dem Band erkennbar sind.
Publikumsfrage
Wer wird das Rennen bei Außenhautteilen machen: Stahl oder Aluminium?
Fr. Traint: Vor 20 Jahren hätte ich noch gesagt Aluminium. Heute sehen wir immer mehr und mehr Stahl. Ich denke, beide Materialien bleiben in Verwendung.
Leading by disruption: the Fisker story
"Teamwork makes a dream work." Henrik Fisker, mit einem disruptiven Ansatz als Autobauer, und Kurt Bachmaier von Magna Steyr über die Zusammenarbeit eines Newcomers am Markt mit einem etablierten Automobilzulieferer.
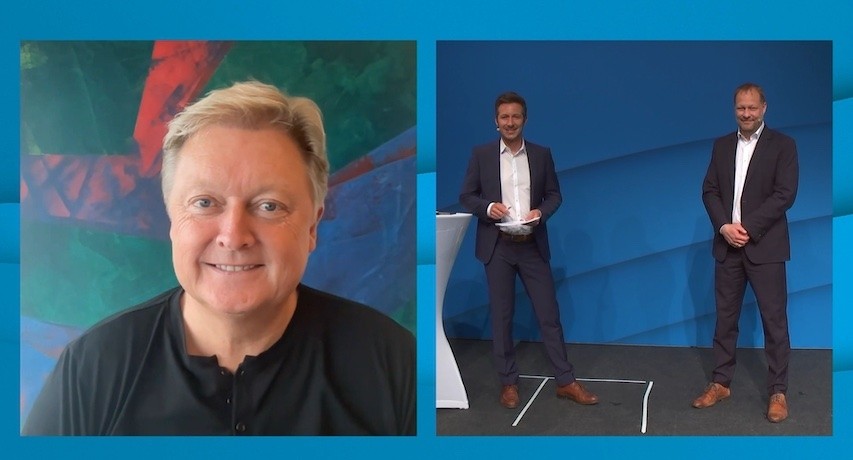
Die Fisker Autophilosophie
Elektrisch, nachhaltig, schnell. Wenn man heute das neueste Auto kauft, ist die Technologie ca. 4 Jahre alt. So lange dauert es von der Konzeption bis zur Serienrealisation. „Das geht schneller, auch bei einem revolutionär nachhaltigem Fahrzugkonzept“, ist die Philosophie von Henrik Fisker.
Der Fisker Ocean
Der Fisker Ocean (das erste Fisker Modell) ist ein 100 % elektrischer SUV, der von Magna Steyr in Rekordzeit zu Marktreife gebracht wurde. Gebaut wird das Modell im Magna Werk Graz. Aktuell werden Prototypen gefertigt. Die Serienproduktion startet am 17.November dieses Jahres.
MAGNA Steyr
Der erfahrene Automobilzulieferer hat bereits über 3,7 Mio. Fahrzeuge gefertigt, über 40 davon selbst entwickelt und bietet die gesamte Wertschöpfungskette – von der Vision des Auftraggebers bis zur Serienrealisation. Auch wenn etwas ganz Neues geschaffen wird, nützt Magna die Erfahrung, die Infrastruktur und das vorhandene Equipment. Damit verkürzt sich der Time-to-Market Zeitraum und die Investitionskosten können entsprechend reduziert werden. Darüber hinaus ist Magna nachhaltig ausgerichtet. Das Werk in Graz produziert bereits CO2-neutral. Weitere Werke folgen weltweit. Gründe für das Start-up Fisker, sich für Magna als Partner zu entscheiden.
Zusammenarbeit mit Start-ups
Die Zusammenarbeit mit einem Start-up unterscheidet sich von der mit einem traditionellen Automobilhersteller. Kurt Bachmaier von Magna Steyr: "Ein Unterschied ist die Schnelligkeit, mit der Entscheidungen fallen. Sie müssen keine Ebenen durchlaufen. Start-ups haben keine großen Organisationen und Back-ups. Sie hinterfragen alles, ob man es nicht schneller und effizienter machen kann. Das gibt auch uns als etabliertem Unternehmen neue Impulse.“
Publikumsfrage
Was sind in Zukunft die größten Herausforderungen für etablierte OEMs und Startups?
Hr. Fisker: Der Preis. Viele Hersteller von Elektrofahrzeugen zielen auf das Luxussegment ab. Wir müssen leistbare elektrische Fahrzeuge bauen, wenn wir auf Erfolg abzielen und für unsere Welt etwas ändern wollen.