„DHO Heat4Future”
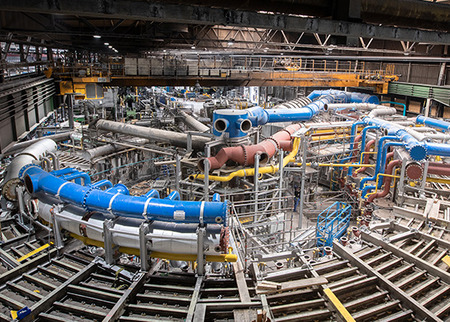
After three months of preparation and meticulous planning, between 10. August and 11. September, up to 200 internal and external people worked on the upgrade.
After three months of preparation and meticulous planning, between 10. August and 11. September, up to 200 internal and external people worked on the upgrade.
In a record time of only four weeks, we have successfully completed the overhaul of our rotary hearth furnace. After three months of preparation and meticulous planning, between 10. August and 11. September, up to 200 internal and external people worked on the rebuild. The volume of the 24.5-meter diameter furnace was doubled and a new generation of regenerative burners with lower emissions and the same output was installed. The project team went to great lengths to keep the implementation time as short as possible: prefabricated components for assembly, a sophisticated warehouse logistics system, a specially built infrastructure on site.
The project would not have been possible without the great team spirit, our partner companies and the trust and support of the management.
For three quarters of a year, the team planned everything down to the last screw. 43 wall elements, each weighing five tons, were pre-fabricated so that as many complete parts as possible could be assembled. They were stored in a logistically optimized way. For the many different parts and materials, a high-bay warehouse with 900 pallet spaces was built on the green meadow.
With an interior temperature of 1,400 degrees, the furnace initially needed four days to cool down. Even after this cooling phase, the work could only be carried out with special protective equipment at a residual temperature of around 60 degrees. Dismantling and reassembly took place almost simultaneously during the overhaul: cooling phase, dismantling of the pipes, opening of the roof for even faster cooling, dismantling and rebuilding of the steel structure, rebuilding of the walls, laying of the pipes and electrical installation, commissioning. It took five days to carefully bring the furnace back up to the required operating temperature.
Heating up had to be done slowly to avoid damage to the complex five-layer furnace wall structure. Around 1,000 tons of refractory material were installed during the overhaul, doubling the volume of the furnace. The new generation of regenerative burners installed not only produces lower emissions at the same output, but is also suitable for all future fuels such as hydrogen or ammonia.
There were so many professionals and absolute experts that there was never a problem because there was always a solution.
Up to 200 people were involved in the DHO Heat4Future project:
With so many additional people on the site, the project team also got creative with the infrastructure for daily catering: To avoid wasting time waiting in line at the cafeteria, everyone was provided with meals directly on the construction site, and covered two-story container villages housed social rooms, showers, and toilets on site.
In two 12-hour shifts, the trades worked around the clock to complete the project. "The great teamwork and the fact that we were able to hire companies we trusted was the key to success," says Heinz Teuschl. "We were a really good team and everyone involved was always solution-oriented," adds Christian Schnitzler.
In the circular furnace with a diameter of 24.5 meters, the pre-cut blocks are heated to the forging temperature of 1,280 degrees. For this purpose, the blocks are placed in the rotating furnace, where they reach the optimum temperature for further processing after one revolution and a dwell time of 130 minutes. The flame temperature is 2,000 degrees, and the blocks are placed at 1,400 degrees. The furnace is particularly space-saving: If an elongated furnace were used, it would be almost 75 meters long.