Good neighborhood welds together!
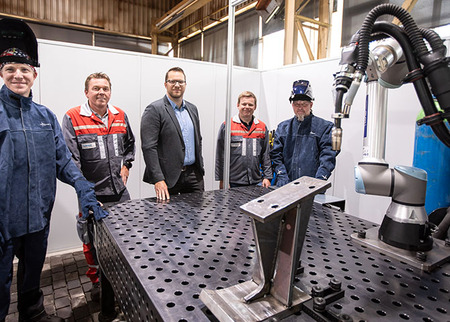
A collaborative welding robot from voestalpine Böhler Welding, a neighboring company in Kapfenberg, Austria, is now in use at our Kindberg site - an intradivisional heart project.
A collaborative welding robot from voestalpine Böhler Welding, a neighboring company in Kapfenberg, Austria, is now in use at our Kindberg site - an intradivisional heart project.
It is no coincidence that the mechanical maintenance department of voestalpine Tubulars turns to Böhler Welding when it comes to welding solutions. It is not just the proximity, but above all the excellent cooperation in many areas that brings the two Styrian metalworking companies together.
Hans Doppelreiter, responsible for mechanical maintenance at voestalpine Tubulars in Kindberg, explains how the project came about:
"We wanted to take the next step in automation and looked for use cases. One of these was the partial automation of welding processes in mechanical maintenance. With the colleagues from Böhler Welding, a solution was quickly found and then implemented just as quickly: a CO-BRO®.
Or rather, a CO-BRO® complete solution, which includes a complete package of welding machine, robotics, automation, welding consumables, personal protective equipment and service.
Working with the robotic welder brings new experiences and is especially helpful when working with large quantities.
Thomas Hold, responsible for Global Application & Welding Solutions at Böhler Welding, explains:
"The kollaborative robot is intuitive to use and gives the welder a lot of freedom.
No in-depth programming knowledge is required, only welding expertise. The tablet tells the robot arm what to do. Only certified welders know how to "teach" the robot: The welding paths, feed rates, gas flow and torch settings must be set correctly. The plug-and-play system is the ideal solution for the production of small and medium series as well as individual parts for your own requirements. After "teaching" the robot, a simulation run without arcing follows. This allows the welders to check whether the torch positioning, torch guidance and torch speed are correct and to take corrective action if necessary. The welding process then starts.
Welders use the CO-BRO® for repetitive or monotonous tasks. It is particularly useful for long welding times, joint welding tasks and job order welding.
The welders can prepare the next parts while the robot is working, and the welding process and weld quality are reproducible for similar parts. In addition, the welding robot also reduces the physical strain on the welders, since the heat radiation and welding fumes are not negligible. Last but not least, this automation also contributes to the company's attractiveness as an employer.
The implementation of the CO-BRO® is a project of the heart, because it is a prime example of the interdepartmental impact and the close cooperation between companies.
Efficiency increase and relief of the employees included!
What exactly the robot has to do is still in our hands. With our knowledge and a lot of
can positively influence the quality of the robotic process.