It's time for a well-deserved retirement
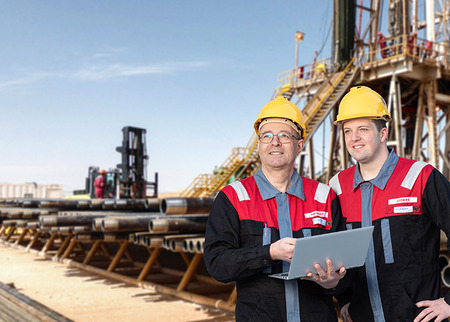
After many years with us in the company, we say goodbye to our colleague Wolfgang Pirchegger. In his big footsteps now steps our colleague Dominik Leitner and thus takes over the After Sales Service.
After many years with us in the company, we say goodbye to our colleague Wolfgang Pirchegger. In his big footsteps now steps our colleague Dominik Leitner and thus takes over the After Sales Service.
In an interview, Wolfgang Pirchegger talks about the history of the plant, his activities and some of his experiences over the past 40 years.
Wolfgang Pirchegger (PI) joined voestalpine Tubulars in Kindberg in 1983.
In 2008, he moved from the Quality department to the Sales department and in 2020 to the Business Development department.
His activities at the plant included
positions of responsibility, including materials testing, quality management and
technical sales and after sales service.
In the course of his professional career at
voestalpine Tubulars GmbH & Co KG, he can look back on more than 200 business trips to more than 60 countries in the last 25 years.
After 40 years, Wolfgang Pirchegger took his well-deserved retirement on May 1, 2023 and
handed over the After Sales Service division to Dominik Leitner.
Products, markets, owners, image, ... a lot has changed.
At the beginning of my career in the Kindberg/Krieglach plant, we almost exclusively supplied standard pipes. Today, we supply almost exclusively special pipes worldwide, i.e. pipes with special grades and special threads.
On the other hand, voestalpine had been nationalized and in the mid-1980s enjoyed a rather poor reputation in the in the media. Today, we can be justifiably proud of our company, which is listed on the stock exchange and held in high esteem internationally. Of course, a lot has changed in terms of equipment.
In general, such a service is extremely comprehensive. The rough procedure on site can be imagined as follows:
1-2 days before the planned installation, we train the installation crew in the handling, installation and characteristics of our threads.This is followed by cleaning & visual inspection of the threads. In addition, the planned equipment is checked (torque recording, friction coefficient of the screw grease, ...).
The installation itself takes between 8 and 24 hours, depending on the depth of the borehole.
Things have changed a lot in recent times. In the past, you came to the drill tower, you introduced yourself as a voestalpine employee, you had to wear a helmet and safety shoes, and you could go anywhere. Today, there are generally very extensive safety regulations, sometimes with a small medical check.
For special drilling operations, however, special courses are required, which are now covered by the worldwide Opito standard. For example, if you want to work on an offshore drilling platform, you need a BOSIET certificate (Basic Offshore Safety Induction and Emergency Training). In this course, you will learn how to fight fires, how to board a lifeboat in an emergency, how to conduct an evacuation at sea, and how to provide first aid.
There is also a simulated helicopter crash and training on how to get out of a sinking helicopter under water.
The whole thing started after the development of our own premium connections. From then on, all the parameters such as diameter, pitch, cone, ... were no longer available in a public standard, but were our intellectual property.
Repair shops are also workshops with CNC machines, which are qualified and licensed by us to be allowed to cut our premium threads. Of course, during the evaluation and certification process, we have a certain obligation to select suitable shops that can also deliver high-quality products to our customers. In order to be able to repair pipes damaged, we have licensed repair shops in strategically important countries with continuous pipe supplies.
In addition, when a pipe is assembled, accessories such as seals, valves, etc. are also screwed on, which must also be provided with our thread. There are various manufacturers of such accessories worldwide, and repair shops have been licensed in these countries as well. We currently have 39 repair shops, but have already visited more than 100 during the evaluation process.
On behalf of the Business Development Department, we wish you all the best for your retirement.
I (Dominik Leitner) have been asked to take over the After Sales Service department that you built up. What advice would you give me?
Thank you very much! We have talked about it a lot, but an old saying says it best:
Many roads lead to Rome! Find the path that is best for you, stand by your decisions and keep your eyes on the prize.