Allgemeines
- Klebeignung der Beschichtung
- Lackaustritt zwischen den Lamellen während des Klebprozesses.
- Für Schnellklebungen kommt die Rollenschälprüfung (in Anlehnung an EN 1464) zum Einsatz.
- Beim konventionellen Kleben erfolgt die Prüfung der Klebeignung entweder mittels Rollenschälprüfung (in Anlehnung an EN 1464) oder mittels Zugscherprüfung (in Anlehnung an EN 1465, gestützte Ausführung).
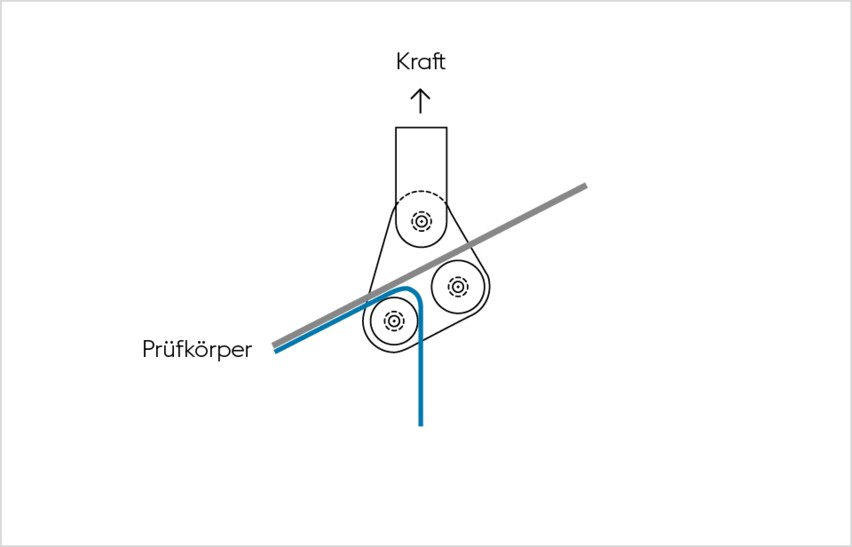
Rollenschälprüfung
Beim Rollenschälversuch nach DIN EN 1464 wird der Schälwiderstand von Klebungen bestimmt. Zwei Prüfkörper werden miteinander verklebt, wobei ein Fügepartner flexibel sein muss. Während der Prüfung wird der Püfkörper über eine Umlenkrolle in einem definierten Winkel mittels einer Zugprüfmaschine abgezogen.
Die Rollenschälprüfung ist eine etablierte Prüfmethode, deren Ergebnis jedoch nicht nur die Klebkraft der Klebung, sondern aufgrund der Versuchsanordnung auch die Festigkeit und Dicke des Stahlbandes beinhaltet.
Zugscherprüfung
Beim Zugscherversuch nach DIN EN 1465 wird ebenfalls die Festigkeit von Klebungen geprüft. Dabei werden die zu fügenden Prüfkörper miteinander verklebt. Mittels eines Zugversuchs wird die Qualität der Klebung beurteilt. In Gegensatz zum Rollenschälversuch ist die Klebkraft unabhängig von der Festigkeit und Dicke des Stahlbandes.
Als Basis reproduzierbarer Ergebnisse bei den jeweiligen Prüfmethoden ist eine entsprechende definierte Herstellung der Prüfkörper erforderlich.
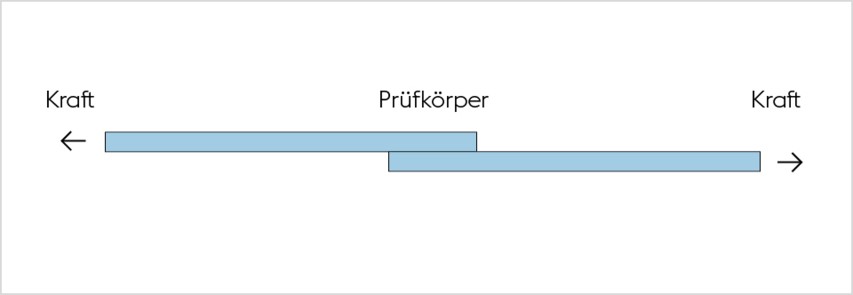
Beurteilung des Lackaustritts mittels Lasertriangulation
Eine visuelle Beurteilung von Lackaustritt zwischen den Lamellen nach der Klebung hängt von mehreren Faktoren ab und beinhaltet immer subjektive Komponenten bei der Beurteilung, wie z. B. Beleuchtung oder die jeweilige Einschätzung der Testperson. Bislang, denn von voestalpine wurde ein Verfahren für eine objektive Beurteilung zur automatisierten Detektion des Lackaustritts an geklebten Prüfkörpern entwickelt.
Mittels Lasertriangulation wird eine 3D-Punktwolke der Stirnseite des verklebten Prüfkörpers erstellt. Erhöhungen im Bereich zwischen den Lamellen, welche einem etwaigen Lackaustritt entsprechen, werden visualisiert und können so automatisch detektiert und als Fehler identifiziert werden.
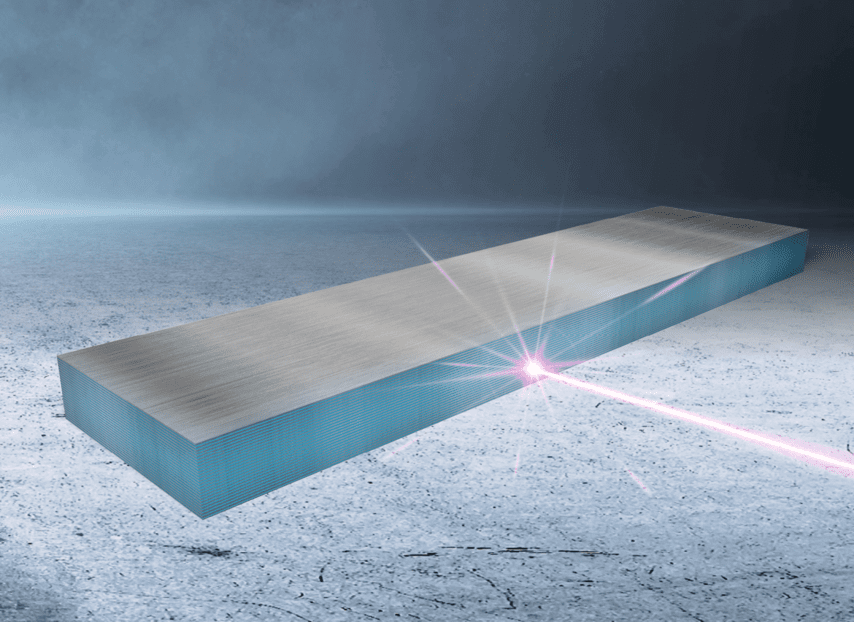

Die großen Vorteile dieser Prüfmethoden im Vergleich zur visuellen Kontrolle durch einen Operator sind:
- Automatisierte, objektive, quantifizier- und reproduzierbare Bestimmung von etwaigem Lackaustritt zwischen geklebten Lamellen
- Zuverlässige Ausgangskontrolle von mit Backlack beschichtetem Material bei voestalpine
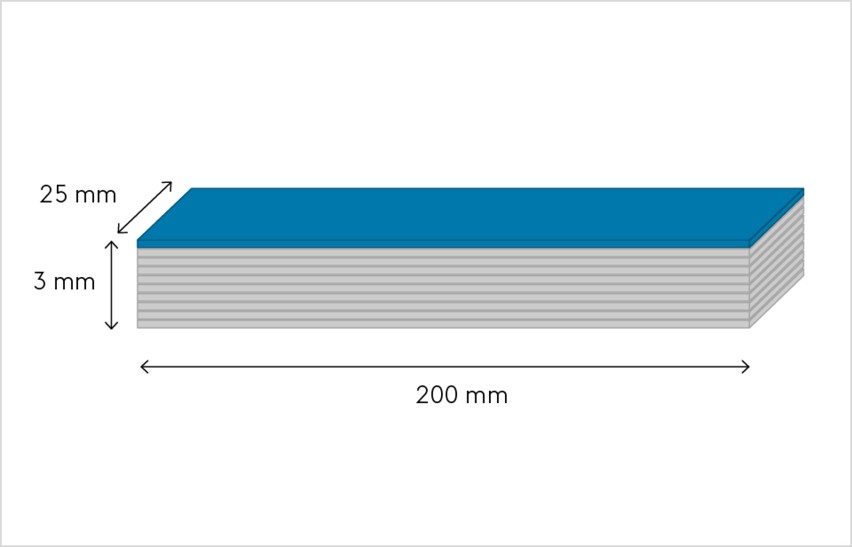
Probengeometrie der Rollenschälprüfkörper
Der Rollenschälprüfkörper wird in Anlehnung an die EN 1464 gefertigt. Der Prüfkörper hat die Dimensionen 25 mm x 200 mm und ist mindestens 3 mm hoch (unabhängig von der Stahlbanddicke). Die Längsseite der einzelnen Lamellen liegt quer zur Walzrichtung.
Von jedem Prüfkörper wird – unabhängig von der Stahlbanddicke – exakt eine Lamelle unter Verwendung der in EN 1464 skizzierten Rollenschälapparatur geschält.
Herstellung eines Rollenschälprüfkörpers
Probengeometrie der Zugscher-Prüfkörper
Die Geometrie zur Herstellung der Prüfkörper wird in Anlehnung an EN 1465 gewählt. Der Zugscherversuch wird für alle Banddicken in gestützter Ausführung durgeführt, indem das eingetlich zu prüfende Fügeteil mit zwei Lagen des gleichen Materials verstärkt wird. Dies dient dazu, die tatsächliche Qualität der Klebung zu beurteilen und eine etwaige plastische Deformation oder einen Bruch des Fügeteils zu verhindern (siehe Abbildung 4). Der Überlappungsbereich beträgt 12,5 mm x 25 mm (Probenbreite). Zur Vermeidung von Probendeformation während der Prüfung müssen die Stützbleche aneinanderstoßen – ein Spalt ist nicht zulässig.
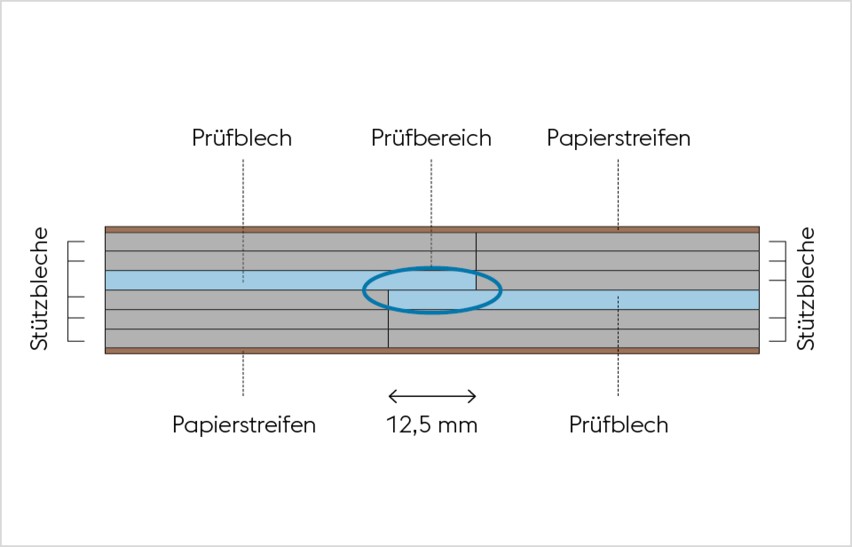