Lamination bonding
Bonding requirements depend on the respective application and size of the manufactured components:
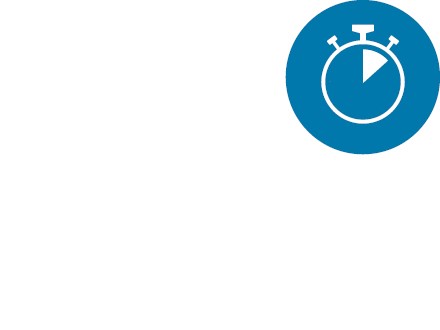
Quick bonding
Components produced in high quantities require high process speeds, and stacks can be produced using the rapid bonding process when such high speeds are required. Heating is inductive. The holding time for a stack is in the range of minutes but requires high temperatures.
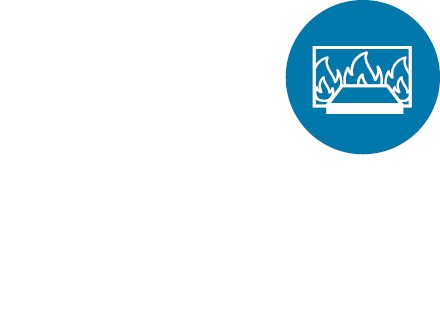
Conventional bonding
Larger components such as motors or generators are suitable for conventional bonding processes that can be carried out at lower temperatures than during rapid bonding, but such processes increase the processing time. The sample is typically heated in furnaces. Very large stacks such as those used in generators are bonded using a conventional bonding process, and it is advantageous to use the lowest possible bonding temperature to account for the size of the component. The lower bonding temperature leads to a more rapid heating of the stacks as well as a shorter cooling period. A varnish specially developed for these requirements is backlack-v®.
An overview of the bonding processes, their areas of application and special features is provided in the following schematic diagram:
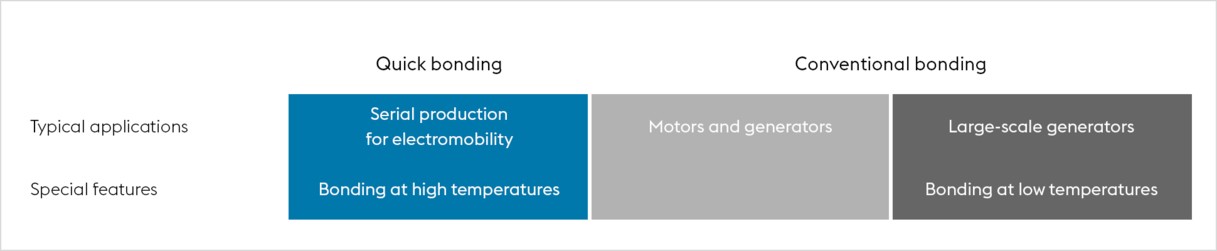
The relationship between bonding temperature and bonding duration for the various bonding methods is illustrated in the diagram below. The exact bonding parameters depend on component size and backing device.
Processing windows for stack assembly using the respective bonding technology are included in the Backlack Processing Guidelines PDF4.19 MBeng-GB.
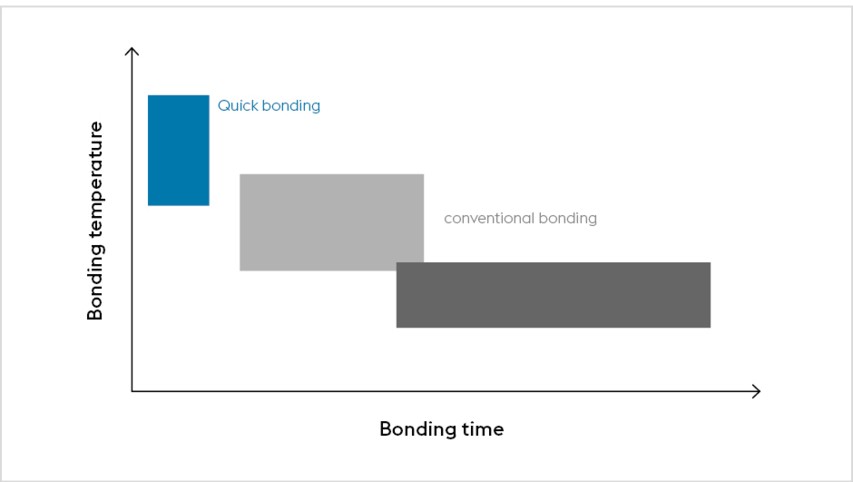
The achievable bonding strengths depend on various parameters such as the applied layer thickness or the testing method used.