voestalpine and ArcelorMittal globally launch galvanized, presshardened steels for direct hot forming
voestalpine and ArcelorMittal are introducing galvanized, press-hardened steels for hot-formed automotive components to the market. Galvanized, press-hardened steels can now be applied in direct hot-forming and are becoming the innovation driver of the industry.
Today's first-class steel must be extremely robust, highly formable, corrosion-resistant and lightweight. The most modern response to this demand is voestalpine's self-developed phsdirectform®. Higher strength is coupled with lower material weight while at the same time maintaining the excellent level of crash performance.
Two of the world's most experienced providers of special steels for hot forming, voestalpine and ArcelorMittal, are bundling their expertise to globally market galvanized, press-hardened steels for direct hot forming.
The ground-breaking development of phs-ultraform® by voestalpine made it possible to indirectly hot-stamp galvanized press-hardened steel components. phs-directform® is the next step in making galvanized press-hardened steels also suitable for the direct hot forming process.
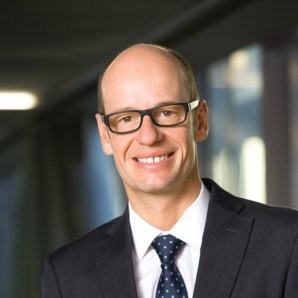
Based on many years of experience in the serial production of galvanized press-hardening steels, voestalpine and ArcelorMittal now market the voestalpine-innovation phs-directform®, a hot-dip galvanized and directly hot-formable steel strip for corrosion-resistant light-weight components.
Wolfgang Mitterdorfer, Member of the Management Board/Sales of voestalpine Steel Division
Hot forming has become very important to the automotive industry in meeting specific crashperformance criteria and low overall weight. Numerous automotive manufacturers use the process to produce structural autobody parts such as B pillars, roof frames and roof bows, bumpers, stiffeners, sills, crossmembers, etc.