Next-generation stator stacks
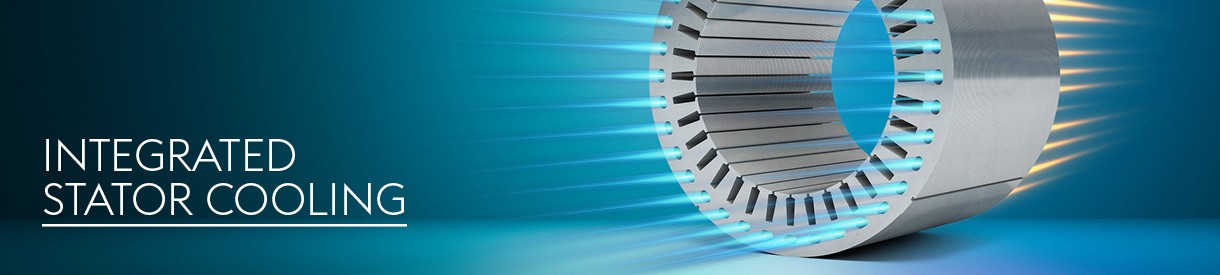
Integrated cooling for increased performance efficiency
The technical specialists at voestalpine have succeeded in developing a manufacturing process for 100% media-tight, full-face-bonded stator stacks with integrated cooling. The package of benefits is convincing.
Baseline and objectives
The target was to produce electric motors with high power density that are even more compact, that are lighter in weight and more powerful. The basis for this was the expertise at voestalpine in Backlack-coated electrical steel strip and the company’s processing know-how in the field of stator stacks. A special process in combination with an inline leak test makes it possible for the first time in the industry to produce 100% media-tight stator stacks that are fully bonded with Backlack and feature integrated cooling.
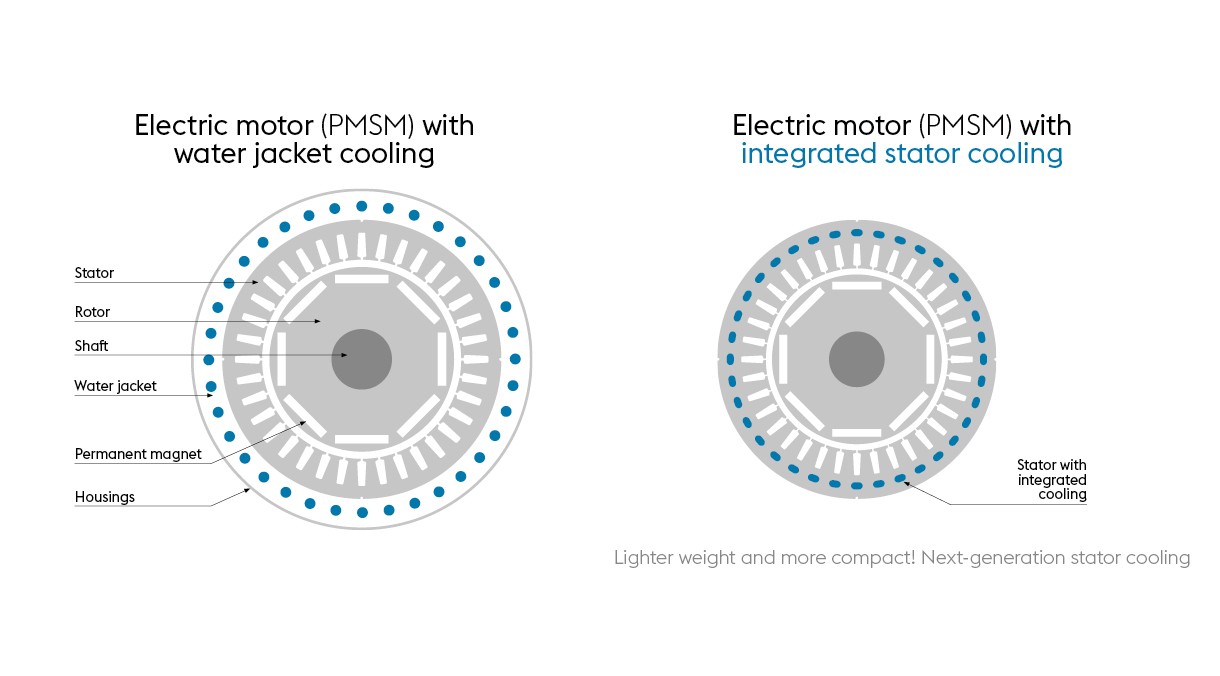
Dynamic process management
A water jacket cooling system surrounding the stator is used for the conventional cooling of electric motors. The voestalpine process does away with this. A dynamic process bonds the thin electrical steel laminations with punched holes used as cooling slots and inlets to form stator stacks. The full-surface bonding with Backlack specially developed for this application is carried out using pressure and temperature in high-precision short presses that prevent the escape of any Backlack. Inline controls ensure media tightness and minimize waste.
Improved engine cooling and performance
Cooling takes place close to the heat source in ducts that are directly integrated into the stator (notch with copper winding). This improves the cooling effect and motor performance. The elimination of water jacket cooling and, in extreme cases, the entire aluminum housing enables lighter weight and more compact motors. This can also lead to higher cost saving potential.
- Stator stacks with integrated cooling
- 100% media-tight, fully bonded with Backlack
- For next-generation electric motors
- More compact, lighter weight, more powerful
- Optimized thermal management
- Up to 40 °C lower e-motor operating temperatures
- Higher continuous torque, approaching peak torque
- Sustainable potentials
- Cost savings (elimination of water jacket cooling, aluminum housing)
- Carbon footprint (less resources, smaller batteries, higher ranges possible)
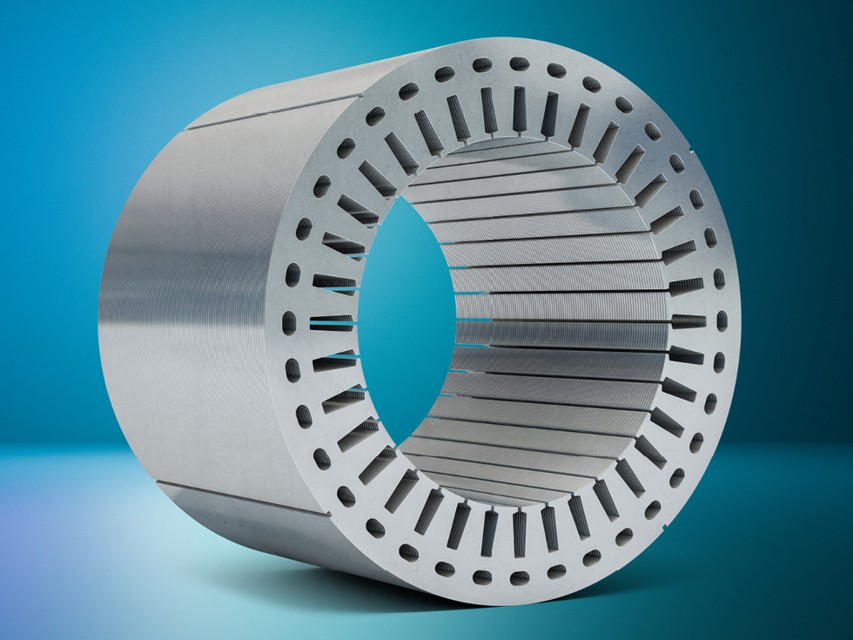
Cooling performance tested and confirmed
The proof of concept was carried out in cooperation with university institutions. Two versions of the motor were compared, one with conventional cooling and one with integrated cooling in the stator stack made by voestalpine. Based on the load range, the voestalpine innovation resulted in a reduction of temperature by 20 to 40 °C when compared to conventional cooling.
Next Step: Ready for serial production
The voestalpine stacking simulator can be used to produce series-based B samples. Development partnerships will be required in order to ensure that the dynamic production process is completely ready for serial production.
voestalpine know-how will be provided as a license order to ensure that OEMs and stamping and stacking companies can reap all the benefits in the future. The Backlack material will be made available to everyone. And of course, the high-quality electrical steel of voestalpine will also be available with Backlack coating.