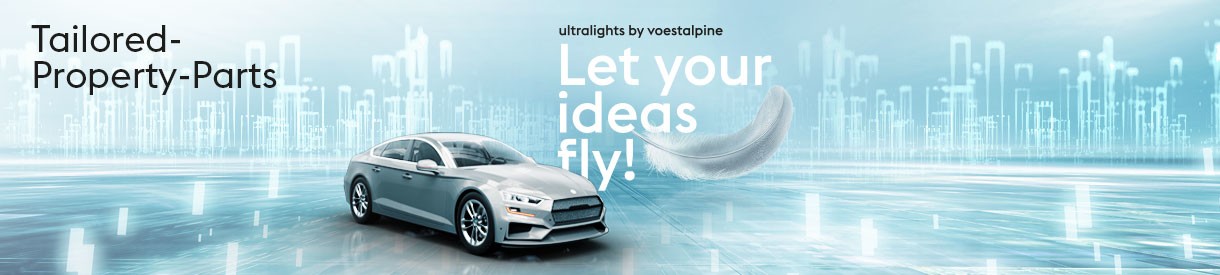
For optimum crash performance in lightweight automotive design
Crash-relevant components must meet the highest requirements in lightweight automotive design. Low weight, high strength where it is needed and defined deformation behavior in areas where it guarantees safety. The materials must be manufactured in an economical process. voestalpine is your partner for tailor-made solutions from blanks to ready-to-install components.
Highest level of expertise
voestalpine combines material and process expertise with competence in serial production. Individualization and optimization begins with the development and provision of various blank configurations. They are produced using the direct and indirect hot forming technologies to produce components with tailor-made properties, while temperature-time curves and heating and cooling processes are decisive factors. The companies of the voestalpine Automotive Components business unit are the specialists in economical serial production.
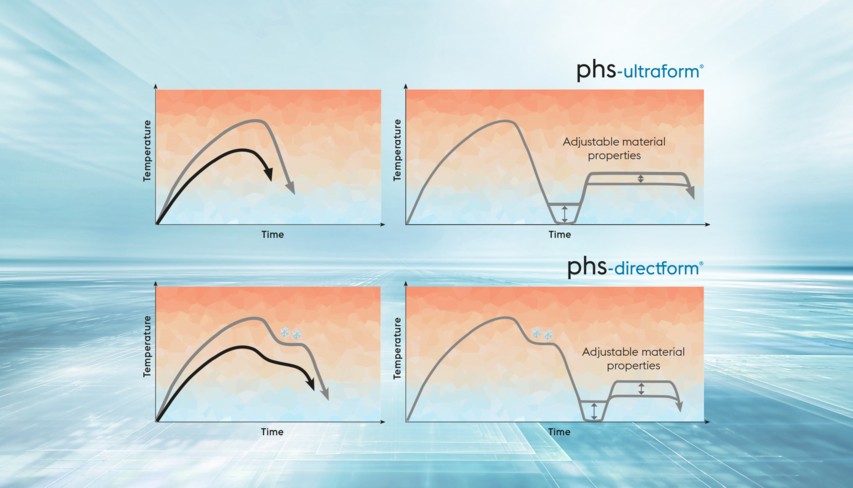
Tailor-made voestalpine advantages
- Individually optimized crash components
- Targeted adjustment of hardness and ductility
- Complex component geometries achievable with few single components
- Blanks for the direct and indirect forming process
- Joint developments
- Overall solutions from a single source
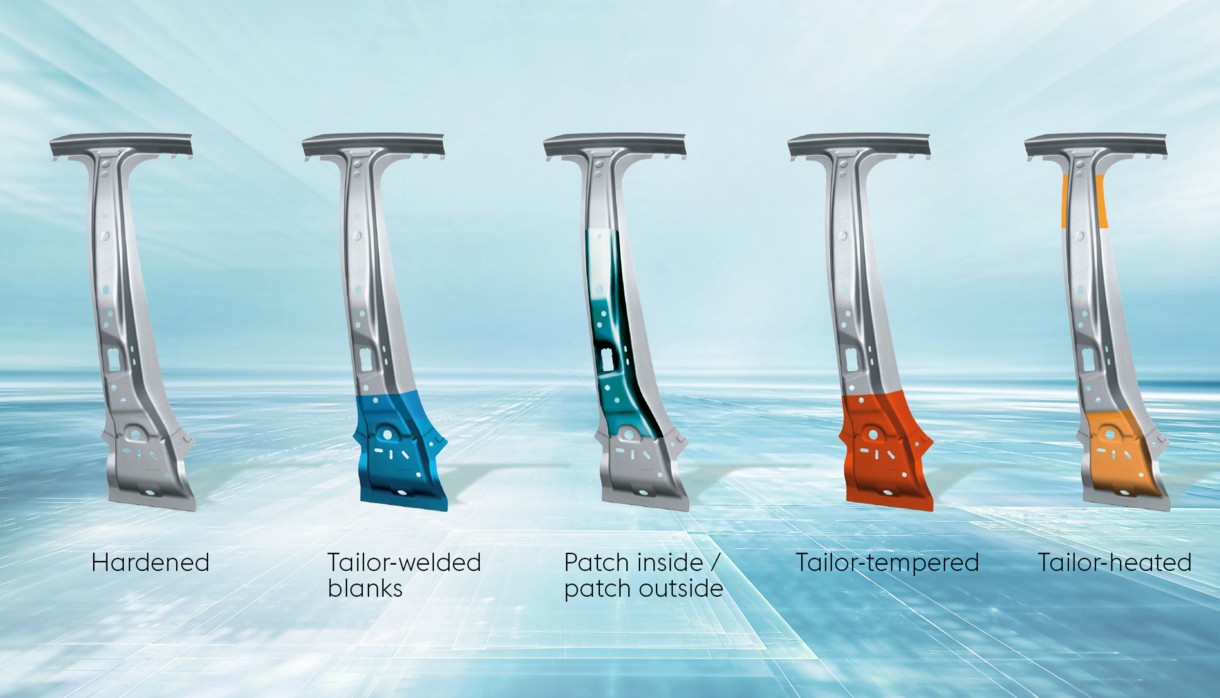
Blank diversity is the basis for individualized component properties.
Tailor-welded blanks: Welded blanks made of different steels and/or different sheet thicknesses (0.8–2.8 mm). They create harder and softer areas in the component. Edge preparation prior to welding is not necessary. For direct (phs-directform®) and indirect (phs-ultraform®) hot forming.Materials:
- phs/hardened 1500–2000 MPa
- Partner material 500 MPa
Patch inside/patch outside: Welded patches reinforce high-stress areas and increase the stiffness of the component. The patches are usually made of a phs material, while other steel materials are also possible. For direct (phs-directform®) and indirect (phs-ultraform®) hot forming. Material:
- phs/hardened 1500–2000 MPa
Tailor-heated: Areas that are meant to remain softer are not heated to austenitizing temperature during hot forming. An absorption mass is applied to smaller zones, and the areas to be hardened in larger zones are heated with heating device focused on the specific area. For indirect (phs-ultraform®) hot forming.Materials:
- phs/hardened 1500–2000 MPa
- phs/non-austenitized 500 MPa
Tailor-tempered:After hot forming, the component undergoes additional heat treatment. The additional heat treatment increases ductility and crash performance. Depending on the duration and temperature of the heat treatment, it is possible to narrow the area of reduced strength to between 1000 and 1500 MPa. For direct (phs-directform®) and indirect (phs-ultraform®) hot forming. Materials:
- phs/hardened 1500–2000 MPa
- Hardened phs + annealed below 1500 MPa